3. Capture
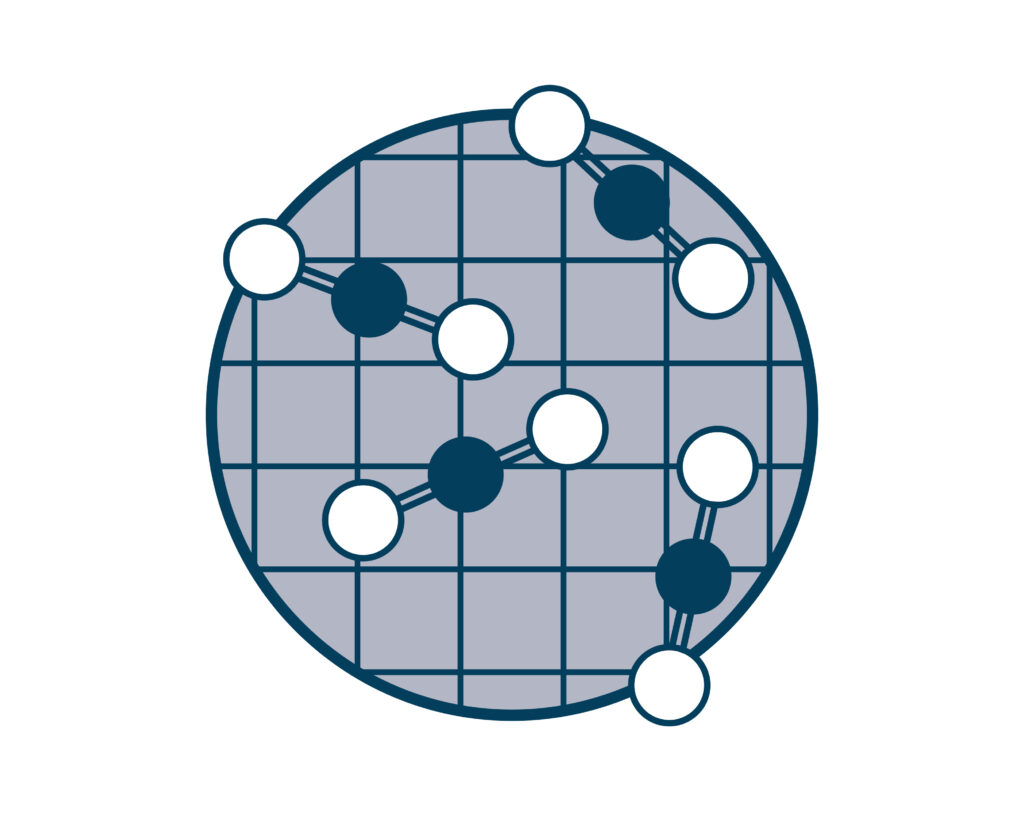
CLIMIT is the national programme for research, development and demonstration of CO2 management technology. For two decades, the programme has been a key actor in the development of technology for carbon capture and storage (CCS). From early laboratory studies to commercial solutions, the programme has supported over 800 projects, making significant contributions to reducing emissions from the energy and industrial sectors. The programme today plays a key role in taking technologies from the lab to market.

“By focussing on innovation, industrial testing and international collaboration, CLIMIT has been able to contribute to Norwegian-developed technology being amongst the best in the world.”
Arvid Nøttveit, Chair of the Programme BoardCapturing CO2 from energy and industrial sources requires efficient separation processes. Existing technologies are facing challenges such as energy requirements, material resilience, gas selectivity, and the cost of capture and associated support processes. Through its work, CLIMIT has supported technology development in all these areas.
For the first ten years, CLIMIT focussed primarily on supporting technology developers.
“Over the course of the last ten years, the programme has expanded its focus to include technology users – including industrial operators such as cement producers and waste incineration plants – who test CCS technologies at their own facilities. This has also included extensive pilot studies and techno-economic analyses.”
Arvid Nøttveit, Chair of the Programme BoardRead more about industry consortia and cluster work.
Throughout its 20 years, CLIMIT has contributed to solvent-based technologies reducing their energy requirements by 35-40 percent. Norwegian-developed technology has progressed from laboratories to international markets, with companies such as SLB Capturi and Baker Hughes having invested in Norwegian solutions.
Traditionally, carbon capture has been divided into three main categories:
- Post-combustion: Capture of CO2 after combustion.
- Pre-combustion: Separation of CO2 and hydrogen before combustion.
- Oxy-combustion: Combustion in an oxygen-rich atmosphere for easier carbon capture.
CLIMIT has supported projects within these categories and has prioritised solutions such as solvents, sorbents, membranes and oxy-fuel technology. Cryogenic processes are less prominent in CLIMIT’s portfolio, as these are commercially avaiable and typically used in the liquification of CO2 before transport.
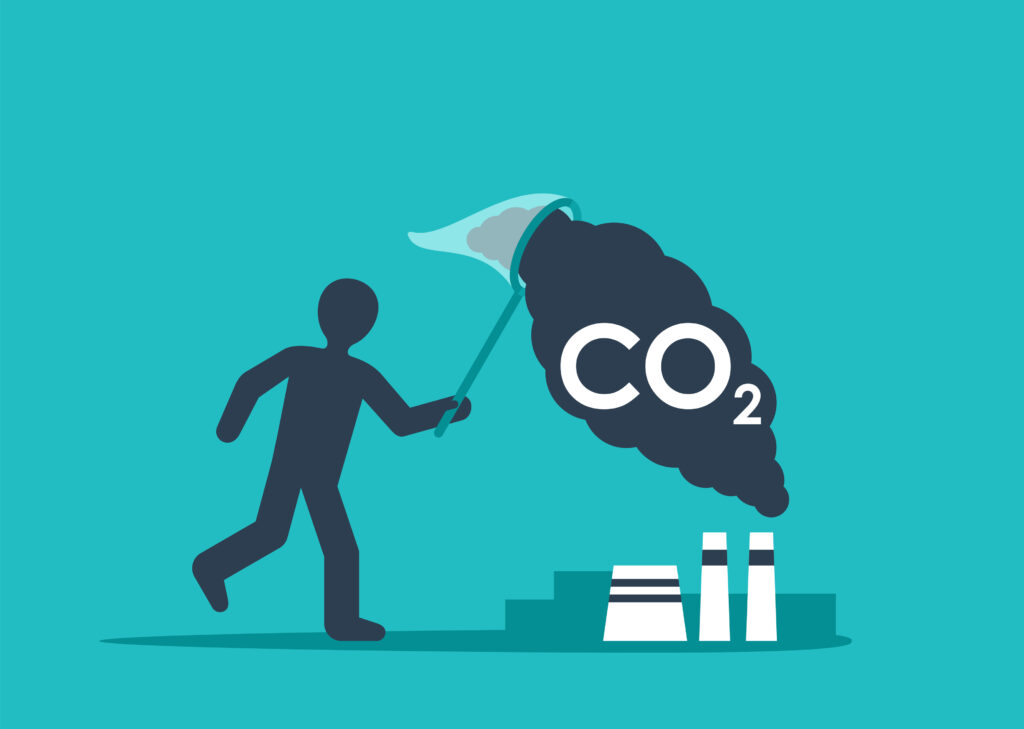
While solvent technology has matured quickly, membrane and looping technologies have received increased attention as energy-efficient solutions for sectors without access to surplus heat.
Solvent-based technologies have been a key focus area since CLIMIT’s inception. This method, which uses liquids to absorb and release CO2 are the most commercially mature technologies for post combustion capture. Solvent projects have reduced energy requirements significantly during the last years, and more than 50 projects have received support from CLIMIT Demo for testing of solvents in pilot facilities such as SINTEF’s Tiller pilot and the Technology Centre Mongstad (TCM).
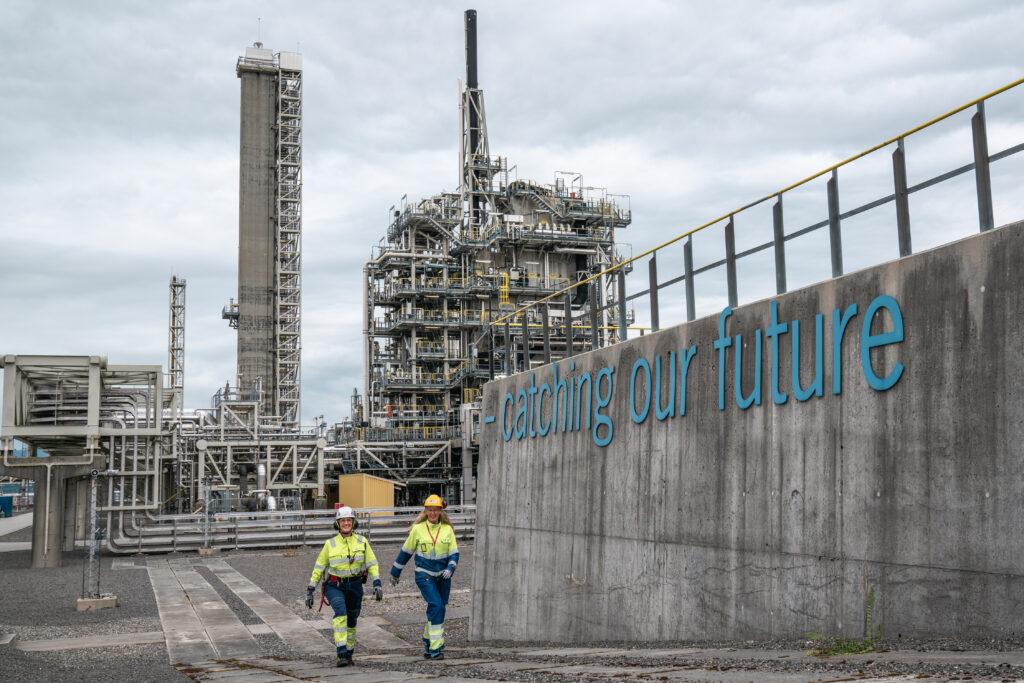
CLIMIT has supported mobile pilot testing, such as SLB Capturi’s mobile unit, testing their solvent technology capturing CO2 from industries such as cement, waste-to-energy, refinery, and others. SLB Capturi’s mobile unit has, by testing in real industrial environment, verified the performance of amine-based solvents at various industries, which has accelerated the commercialisation of the technology.
Sorbent technologies, such as carbonate looping, use solid materials that capture CO2.
The Moving Bed Carbonate Looping technology developed by Fjell Technology Group with support from CLIMIT uses lime-based materials that are recognised and cost-effective. The technology could be well-suited for the cement and lime industry being familiar with the lime-based material at high temperature operations.
Membranes are an exciting option for industries without surplus heat, such as cement production, and have the potential to be a cost-effective solution. CLIMIT has supported a range of projects for the development of membranes, including as a technology tested at the Heidelberg Materials test centre in Brevik.
Air Products has also carried out membrane testing at Returkraft with support from CLIMIT. The project assessed the efficiency of the membranes by capturing CO2 from Returkraft’s flue gas.
Membranes, which separate gases without chemical regeneration, is particularly suitable for emission sources with high concentrations of CO2, such as the lime or cement industries.
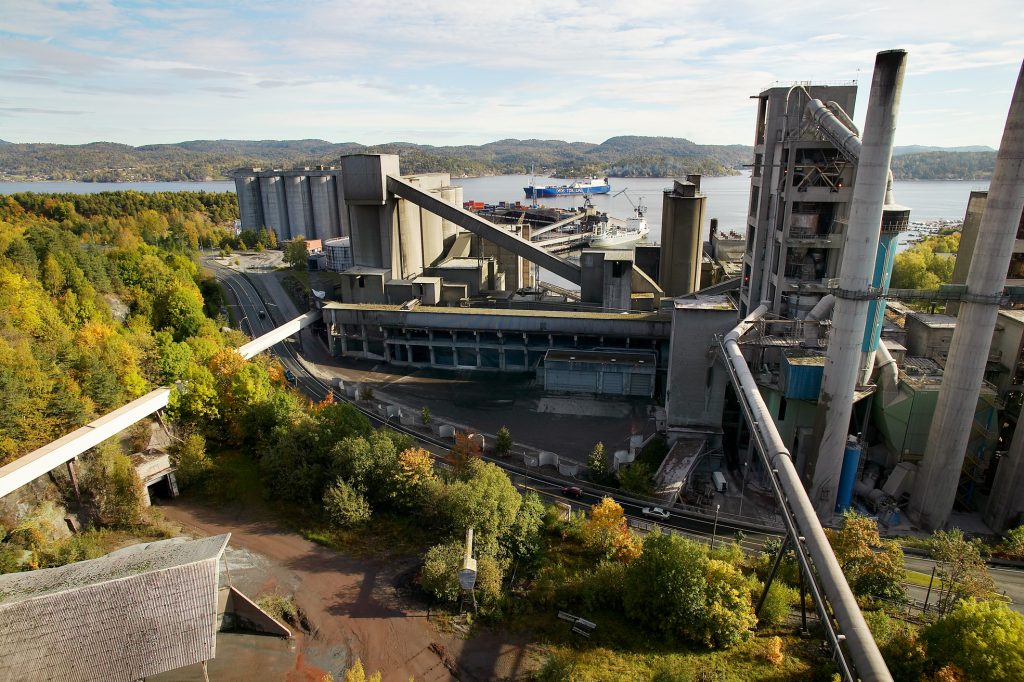
CLC technologies, which uses metal oxides to create an oxygen-rich combustion atmosphere, have received over NOK 70 million in support from CLIMIT. This method reduces the need for a separate capture facility, which will be positive financially for certain industries.
Read more about the application of CLC technology, SINTEF
Over 270 capture projects have received support from CLIMIT, totalling over NOK 1.7 billion in funding. CLIMIT’s contribution has not only triggered equivalent investments from industry, but also helped create a robust CCS ecosystem in Norway.
Multiple projects have been led by SINTEF, which has built up knowledge and world-class expertise within CCS. SINTEF’s Tiller pilot in Trondheim has played a crucial role in qualifying technologies for industrial emission sources. Testing at TCM has further validated these technologies for global implementation.
CLIMIT has strengthened collaboration between academia and industry by funding projects led by SINTEF and NTNU. This has created a platform to connect basic research to practical technological development. CLIMIT’s financial contribution has acted as a catalyst for taking CCS technology from research to commercial application.
Read more about SINTEF’s work on solvent development and pilot testing with CLIMIT support.
Many projects have had international significance, including:
- SLB Capturi (formerly Aker Carbon Capture): Technology developed with CLIMIT support is now used commercially, including by Heidelberg Materials at their plant in Brevik.
- Compact Carbon Capture (3C): Technology developed by Fjell Technology Group and continued by Baker Hughes.
- Hydrogen MemTech: Membrane technology that is attracting international capital.
For 20 years, CLIMIT has been an important driver of CCS technology development. With support for research, pilot projects and commercial implementation, the programme has contributed to Norway becoming a leading stakeholder in the global effort to reduce greenhouse gas emissions.
CLIMIT’s contribution has facilitated Norwegian-developed technologies being used commercially in projects such as Heidelberg Materials’ plant in Brevik and international efforts for cement and waste incineration.
“CLIMIT’s support has not only accelerated the development of cost-effective solutions, but also helped build bridges between research, industry and public authorities. With a strong foundation and successful projects behind it, CLIMIT continues to be a driver of future CCS solutions. This is crucial for meeting the world’s climate goals.”
Arvid Nøttveit, Chair of the Programme BoardThrough the Longship project, Norway has taken a leading international role in carbon capture and storage (CCS). The journey to realising the project has been long and challenging, particularly when it came to the development of practical fullscale carbon capture technology. Support from CLIMIT has been vital for the development and testing of technology that can now be implemented at the Heidelberg Materials capture facility at its cement factory in Brevik.
This article presents two of the largest CLIMIT-supported projects: The SOLVit programme and Heidelberg Materials’ test centre in Brevik.
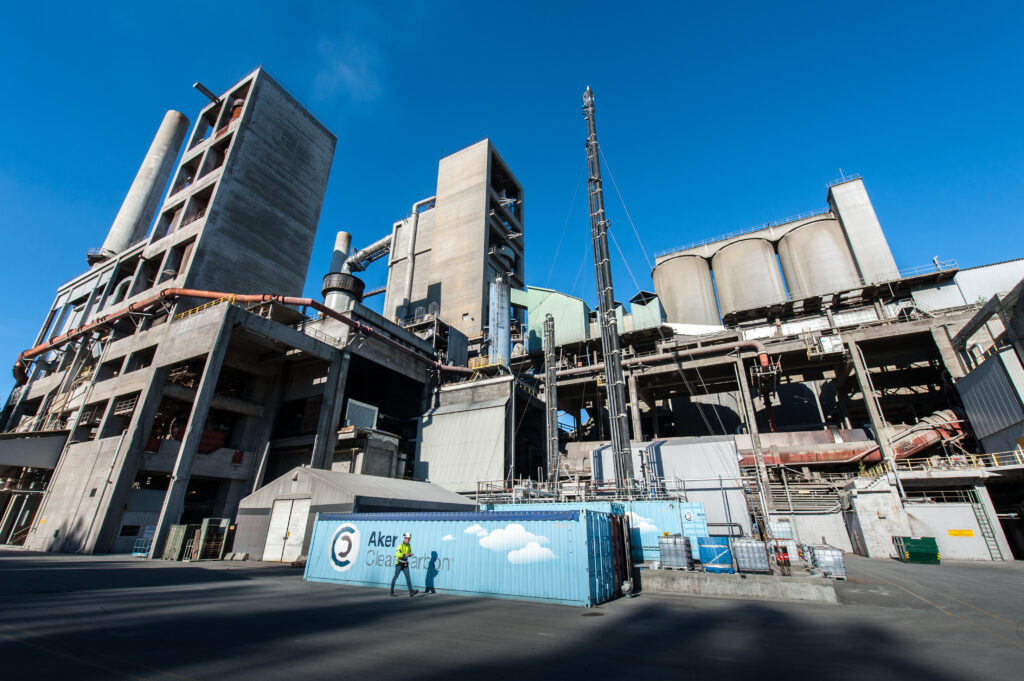
SLB Capturi (formerly Aker Carbon Capture) developed its amine technology through the SOLVit programme. After extensive testing at the Heidelberg Materials (formerly Norcem) test centre in Brevik, the technology was chosen as the preferred solution for fullscale demonstration of carbon capture at the cement factory. The capture facility is a core part of the Norwegian CCS demonstration project Longship.
The SOLVit programme (2008-2015) was a major research and development programme that focussed on improving carbon capture solvent and process technologies. The programme was led by Aker, with research activities carried out by SINTEF Industry in Trondheim in collaboration with Aker and the Department of Chemistry at NTNU. A number of industry partners and potential end users of carbon capture technologies, including EnBW, E.ON, Scottish Power and Statkraft, contributed actively to various parts of SOLVIT
The programme was partially funded by CLIMIT and the Research Council of Norway, with a budget of NOK 332 million, of which NOK 132 million (40 percent) came from CLIMIT.
The primary goal was to reduce the cost of carbon capture from emission sources through the development of more energy-efficient solvent systems and adjusted process technologies. Other goals included developing more environmentally-friendly solvents and demonstrations of performance improvements of the new solvents at pilot scale.
The SOLVit programme was implemented in three phases, with each phase building on experience from the previous ones:
- Phase 1 (2008-2010): The development of functional solvents, establishing laboratory facilities and a stationary pilot facility at SINTEF Tiller.
- Phase 2 (2011-2012): Characterisation and pilot testing of first-generation solvents, focussing on the development of new, ground-breaking environmentally-friendly solvents and a reduction in the environmental impact of the carbon capture process.
- Phase 3 (2013-2015): Qualification of solvents through pilot testing of various industrial waste gases, demonstration at the Test Centre Mongstad, as well as the development of technology for cost reductions for carbon capture.
SOLVit’s work was organised into four main areas: Basic studies, modelling, technology development, and pilot testing and demonstration. Through the SOLVit project, highly sensitive LCMS methods were also developed for quantifying degradation products in solvents, with sensitivity of less than 1 ng/ml. Methods were developed for over 50 amines, as well as specific methods for alkylamines, nitrosamines and other degradation products.
A training programme was also introduced at NTNU, which contributed to basic research on solvent-based capture processes. Many doctoral and masters students carried out their studies through this programme, contributing to the training of qualified researchers within carbon capture technologies.
“The SOLVit programme and CLIMIT’s support contributed to the maturation of SLB Capturi’s capture technology, in particular our energy-efficient and robust solvent which was developed to have the smallest possible environmental impact. The further testing at the Heidelberg Materials cement factory in Brevik demonstrated that our amine technology was mature and ready for fullscale implementation. Now in December 2024, the plant in Brevik is complete and ready for start-up and testing, and the carbon capture will begin over the course of 2025. A fantastic development from the SOLVit programme so far.”
Jim Stian Olsen, CTO, SLB CapturiPilot testing showed that SOLVit solvents were robust, energy-efficient and environmentally friendly. An improvement of up to 35 percent in energy consumption compared with MEA (Monoethanolamine) was demonstrated, as well as significantly lower solvent consumption and degradation rates. Amine emissions and degradation products could be kept at far lower levels, reducing uncertainty related to the environmental impact of amine-based capture processes.
In summary, the eight-year-long SOLVit programme provided increased understanding of solvent-based capture processes at both the basic and industrial level. Many new solvents for carbon capture from waste gases were developed. The programme contributed significantly to the maturation of Aker’s carbon capture technology, and reduced the risks related to scaling up and large-scale implementation.
For more information about SOLVIT, see here:
- SOLVit – climit.no
- Highlights and Main Findings from the 8 Year SOLVit R&D Programme – Bringing Solvents and Technology from Laboratory to Industry
The primary aim of the test centre was to evaluate and compare selected carbon capture technologies to find the most suitable option for emissions from the Heidelberg Materials cement factory in Brevik. The project had a total budget of NOK 93 million and received NOK 70 million (75 percent) from CLIMIT Demo. ESA (European Surveillance Authority) approved the high level of state support. The project ran from 2013 to 2015.
The project focussed on the capture part of the CCS chain, with a focus on CO2 capture capacity, energy consumption, impact of pollutants and costs. The utilisation of residual heat from the factory was also important.
“CLIMIT’s support for our test centre in Brevik has been key to our work on developing and implementing ground-breaking carbon capture and storage technologies. The support has been a vital driving force in Heidelberg Materials’ development of the world’s first CCS cement, evoZero, which will allow the construction and engineering sector to cut out significant volumes of CO2 by using climate-neutral cement.”
Pia Prestmo, Manager Public Affairs Norway, Heidelberg MaterialsThe test centre project consisted of two main parts:
1) Pilot testing:Testing under real-world conditions on emission sources from the cement factory in Brevik
2) Fullscale evaluations: Field testing and modelling for fullscale implementation
In Phase I, four technologies were selected: Aker Carbon Capture Amine Technology, RTI Solid Sorbent Technology, KEMA GL/NTNU & Yodfat Engineers Membrane Technology, and Alstom Power Regenerative Calcium Cycle. In Phase 2, RTI Solid Sorbent Technology Phase II and Air Products & NTNU Membrane Technology were studied.
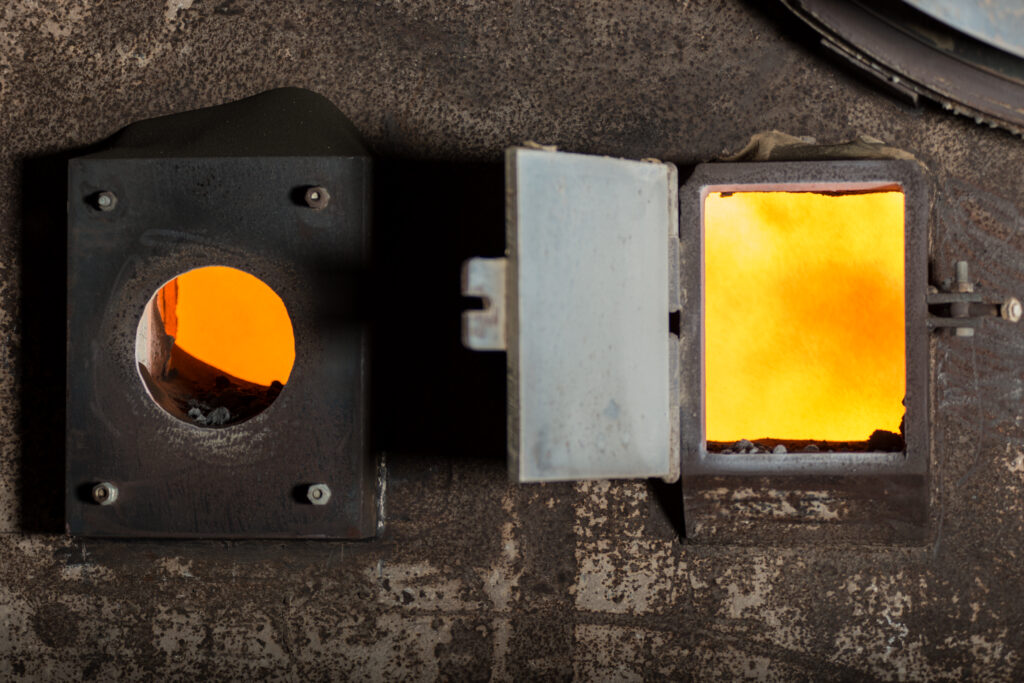
Testing covered needs for technological optimisations. Aker’s amine technology was identified as the most mature and ready for fullscale demonstration. As a result, SLB Capturi (formerly Aker Carbon Capture) is chosen as the technology supplier for Heidelberg Materials’ fullscale carbon capture project, which is today a part of Longship.
For more information about the Norcem test centre (Heidelberg Materials in Brevik)
Over the past 20 years, CLIMIT’s support of carbon capture projects have reflected a major change in emission sources. Initially focusing on fossil-fuel power plants, the scope has expanded to hard-to-decarbonize industries and now to direct air capture. These developments underscore the importance of diversity in technology in delivering efficient and sustainable carbon capture and storage solutions.
The article ”CLIMIT has contributed to the development of carbon capture technology for 20 years” highlights the most significant carbon capture technologies and CLIMIT’s role in their development. This article discusses general trends and and anticipates key factors for carbon capture and CCS in the coming years.
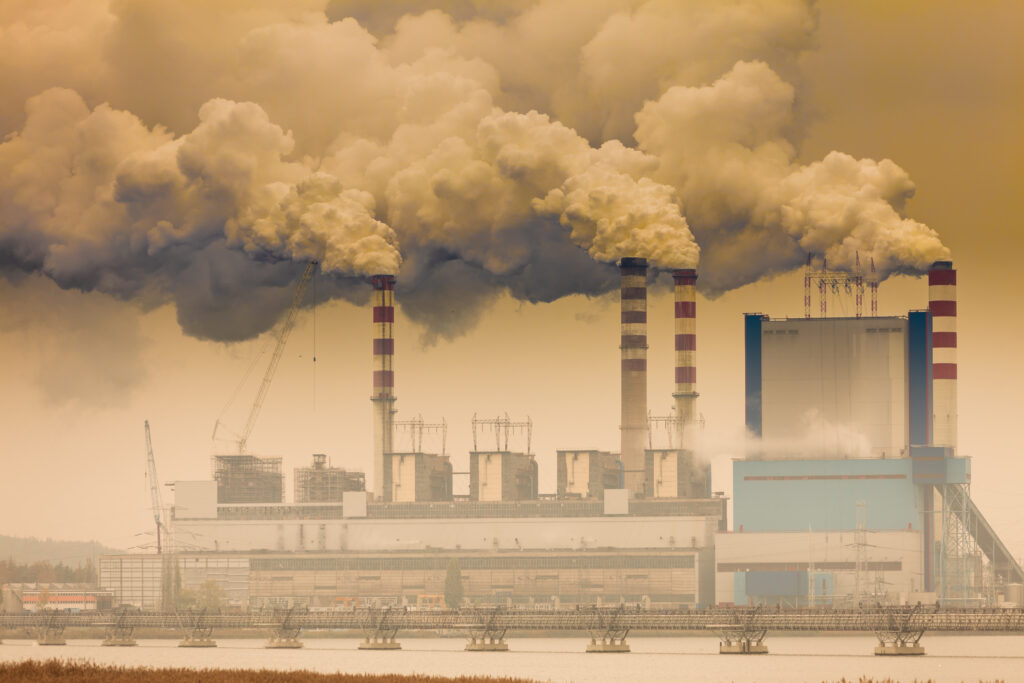
CLIMIT began as a programme supporting development of carbon capture at gas-fired power plants. In 2008 it expanded to also include coal-fired power plants, and by 2010 capture from energy intensive industry was incorporated. In 2021, the programme removed the requirement to specify emission sources, allowing support for technologies capturing CO2 from the atmosphere.
This evolution in the CLIMIT programme illustrates the change in the market and the need for flexible capture technologies capable of handling a broad range of emission sources, which vary significantly in annual emission quantities, CO2 concentration, and other pollutants. Integrating capture technologies with different emission sources presents unique challenges that must be addressed individually.
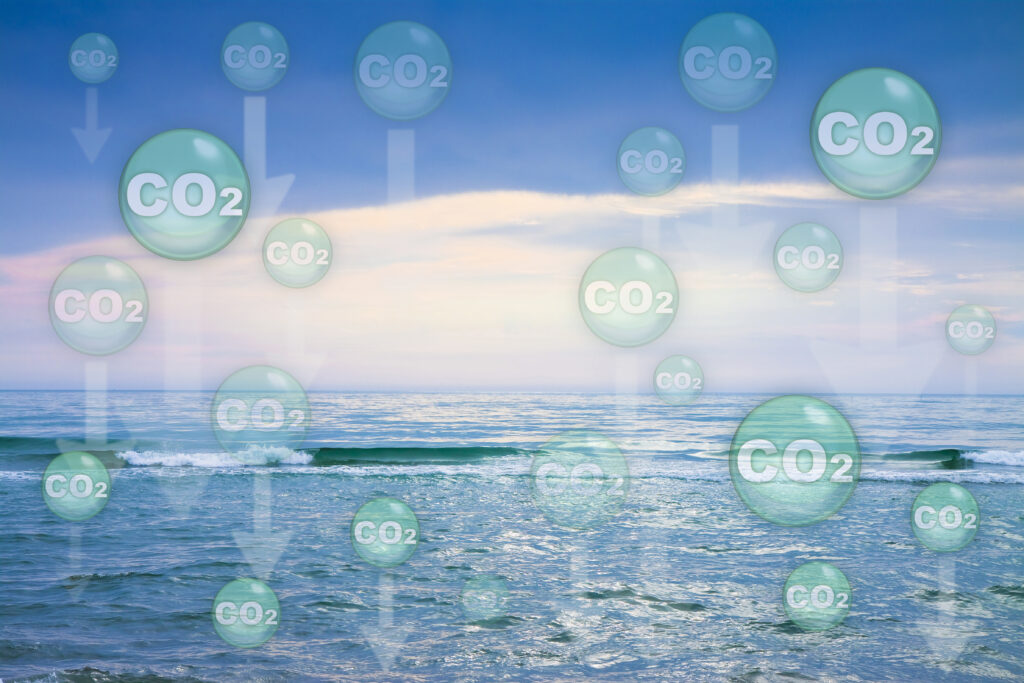
Another trend is the shift from large, site-specific capture facilities to more cost-effective, modular solutions that can be quickly deployed and adapted to different needs. A notable example is SLB Capturi (formerly Aker Carbon Capture) with its Just Catch solution which may simplify the implementation of capture facilities and reduce costs.
Amine technology is renowned its broad applicability and adaptability to different CO2 concentrations, ranging from 2% to 30%, making it a flexible solution for numerous emission sources. For waste gas with around 10 percent CO2 content, the energy consumption for many commercial amine-based capture facilities is around 2.5-3 GJ/tonnes of CO2. This efficiency, coupled with the technology’s ability to utilise surplus heat in the desorption process, makes amines the preferred solution for emission points where surplus heat is available, reducing both operating costs and energy consumption.
In recent years, capture rate has become an increasingly important KPI for industrial facilities with point source emissions. Previous requirements typically demanded a 85-90 percent capture rate, allowing at least 10 percent of CO2 in waste gases to be emitted into the atmosphere. Now, requirements often exceed 95 percent, with the goal of approaching 100 percent.
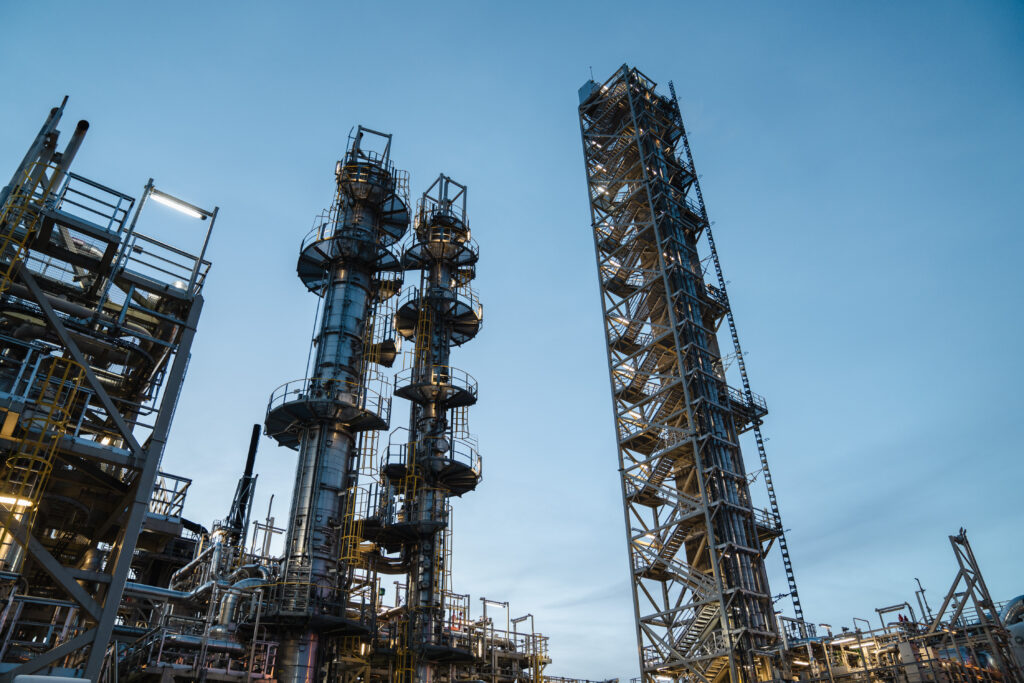
Amin plant at Technology Centre Mongstad. Photo: TCM
Amine technology excels in this area. Many suppliers, including SLB Capturi, have demonstrated the ability to achieve capture rates over 95 percent. This was confirmed through the CO2 Hub North project, which tested increased capture rates from point source emissions – a more cost-effective and environmentally-friendly strategy compared to combining lower capture rates from emission sources with the use of DACCS to achieve net zero emissions. CLIMIT provided financial support to this project.
For many years, Norway has been a leader when it comes to environmental aspects and controlling emissions in relation to carbon capture. Internationally, there is a growing demand for environmentally friendly solutions. Amine emissions have been a significant research focus in Norway. This work has garnered increasing international interest.
Other solvents, such as K2CO3 or membrane technology, are particularly appealing for industries without access to surplus heat and with relatively high CO2 partial pressure in the waste gas, such as the cement industry. These solutions offer low to no amine emissions but may struggle to achieve capture rates over 95 percent.
There is also a heightened focus on facilitating capture by pre-treating the waste gas and including liquefaction as a part of the capture concept, including at pilot facilities. Improved heat utilisation in the capture process through various heat exchange methods has also gained attention.
Industries with significant CO2 emissions are exploring options to modify process steps to remove CO2 in a more concentrated form (“ready captured”), avoiding the need for expensive capture facilities that require separate resources and new expertise. This approach will necessitate changes to existing production facilities and require extensive testing and development of new technologies and process steps. For most, this will be a post-2050 solution.
Examples of such projects at CLIMIT Demo include:
- Devleopment of HAL ZERO Technology by Hydro Aluminium
The project that led to Hydro Aluminium’s HAL ZERO focus: Project 618242 LowCO2Al with NOK 16.25 million support from CLIMIT, covering 65 percent of total costs. Project period: 2019-2021.
A CLIMIT supported project that are a part of HAL ZERO and run parallel with the HAL ZERO pilot supported by Enova: 622124 HalZero CO2 to CO – concept studies. The project received NOK 4.5 million from CLIMIT, covering 50 percent of total costs. Project period: 2022-2024. - Electrification of the calcination process – Heidelberg Materials
Project 617333 Combined Calcination and CO2-capture in Cement Clinker Production by Use of CO2-neutral Electrical Energy (6CP) – Phase 1. The project received NOK 1.7 million from CLIMIT, covering 65 percent of total costs. Project period: 2018-2020.
Project 620035 Combined calcination and CO2 capture in cement clinker production by use of CO2-neutral electrical energy – Phase 2. The project received NOK 6.25 million from CLIMIT, covering 62 percent of total costs. Project period: 2020-2024.
The work in the above-mentioned projects led by Heidelberg Materials have now progressed further in the project ELECTRA, supported by the EU, cf. https://www.electra-horizon.eu
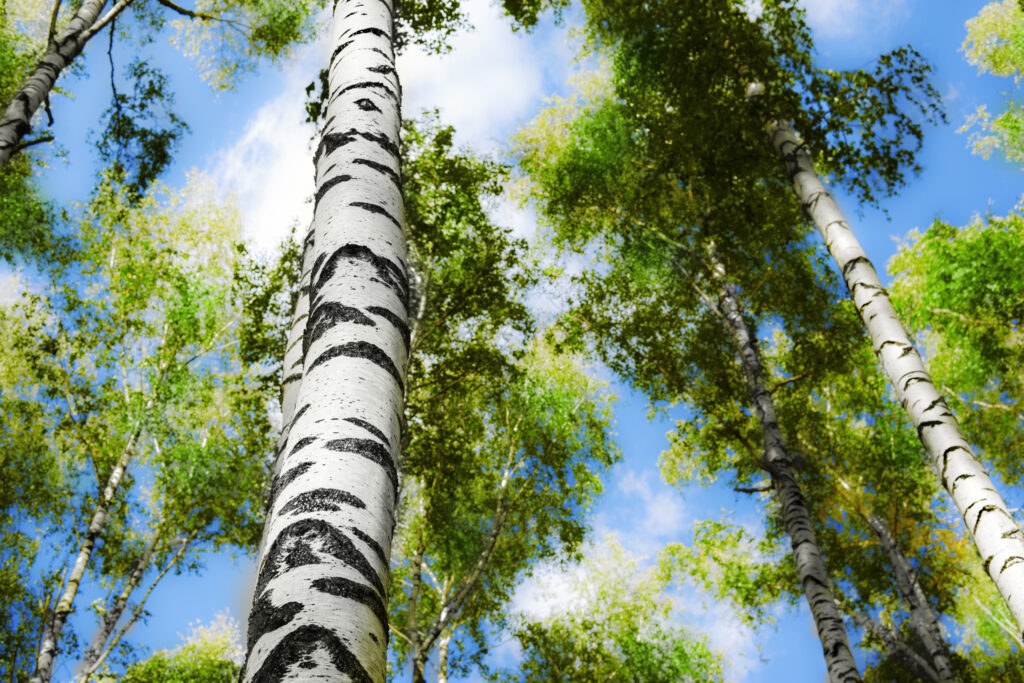
Carbon Dioxide Removal has gained significant attention over the past five years. CDR involves targeted capture of CO2 from the atmosphere for permanent and secure storage, as outlined in Innovation Roadmap – Mission Innovation CDR
CDR technology can be categorized into three areas:
- Direct Air Capture (DAC)
- CDR from biomass, known as Biomass Carbon Dioxide Removal and Storage (BiCRS)
- Enhanced Mineralisation (EM)
CLIMIT has supported some smaller air capture studies. However, BiCRS has been the primary recipient of program funds for industries exploring options for capturing and storaging biogenic CO2 from combustion or processing of biomass (bioCCS).
BioCCS is as a methodology that facilitates CCS through improved business models with revenues from the sale of carbon credits. There is also an increasing interest in CDR from smaller emission sources of pure biogenic CO2 emissions (no or little content of fossile CO2) through bioCCS.
The waste incineration industry has approximately 50 percent biogenic CO2 in its waste gas. Capture ad stored biogenic CO2 may allow for the sale of credits if the carbon calculations show that more CO2 equivalents are captured than emitted. See also information about the KAN collaboration in the Waste-to-Energy industry in the article Industry consortia and cluster work (Norwgian)
Norwegian companies in the Energy Intensive Industry such as Elkem and Eramet have also received support from CLIMIT for carbon capture projects and feasibility studies at separate facilities. These industries replace coal with biomass to reduce fossil-fuel emissions. As Waste-to-Energy facilities, these will have a mixture of fossil- and biogenic carbon emissions.
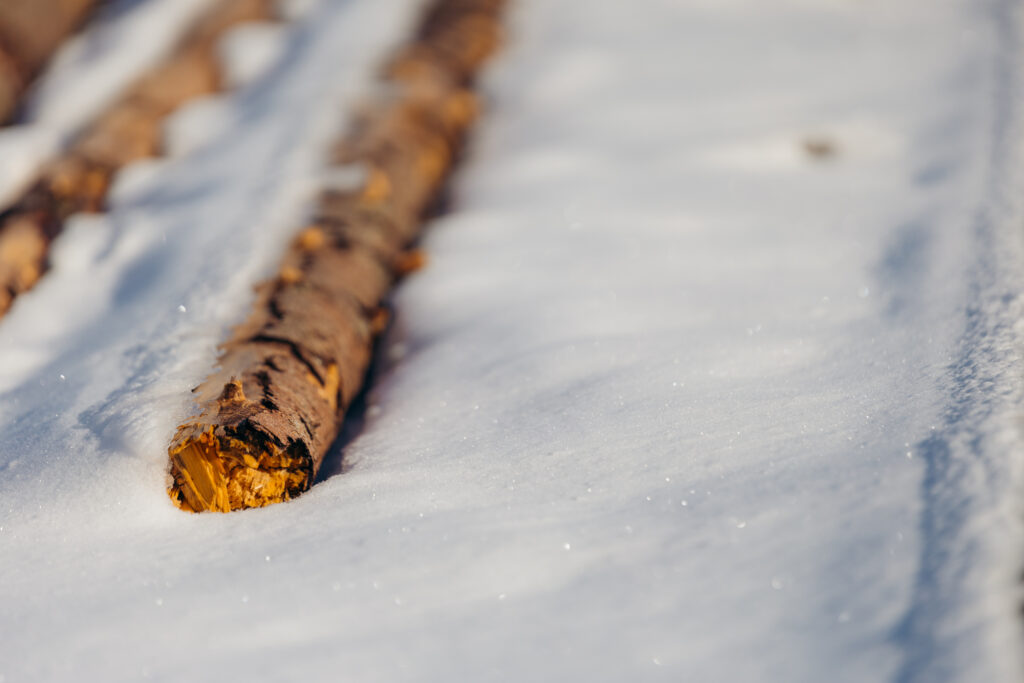
One of the largest challenges for implementing carbon capture and storage (CCS) in Norway is the lack of infrastructure and transport solutions. The long distances to storage sites also create complexities that require innovative solutions, according to a report from Oslo Economics, “Virkemidler for karbonfangst fra industri og avfallsforbrenning” (Norwegian).
Norwegian emission sources, such as the Energy Intensive Industry and Waste-to-Energy Industry, have relatively low carbon emissions per point source, typically ranging from 100-450 kilotonnes per year. This is significantly lower than emission points in other European countries, where emissions can reach millions of tonnes annually. Norwegian industry is also geographically dispersed, increasing the need to capture CO2 from more sources to achieve sufficient volume for transport and storage.
Lyse, alongside partners in Rogaland, is working on developing smaller, emission-free ships that can collect CO2 from various emission points and transport it to intermediate storage sites before further pipeline transport to storage sites.
This project, supported by CLIMIT, demonstrates how technology and cooperation can overcome logistical barriers. Many other important transport projects, also supported by CLIMIT, are under development and address similar needs.
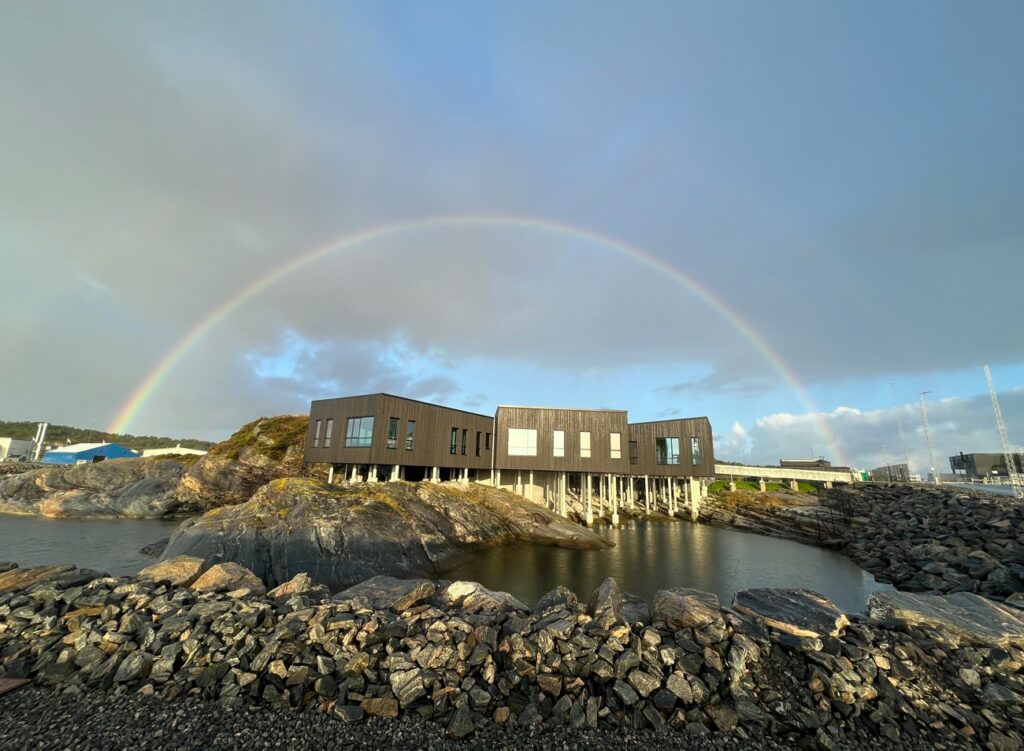
For some time, Northern Lights in Øygarden has been the only available storage option for CO2 in Norway. Now with more operators and storage areas on the market, transport to several new storage sites with carbon capture from multiple sources is planned. This includes expanded infrastructure that facilitates the integration of CCU (carbon capture and utilisation) as well as opportunities to handle emissions from smaller sources such as biogas facilities. Several municipalities and county councils have adopted ambitious targets to achieve net-zero emissions by 2050, further increasing the need for robust CO2 infrastructure.
Interest in onshore geological storage of CO2 in Norway is also increasing. Although this is still in the research and development stage, it represents a potential future solution and an important supplement to offshore storage.
Technologies such as artificial intelligence (AI), machine learning, advanced models and the development of 3D, 4D and 5D printing will be of increasingly importance for carbon capture and storage in the coming years. These tools offer new possibilities to optimize processes, reduce costs, and improve performance across the entire CCS value chain.
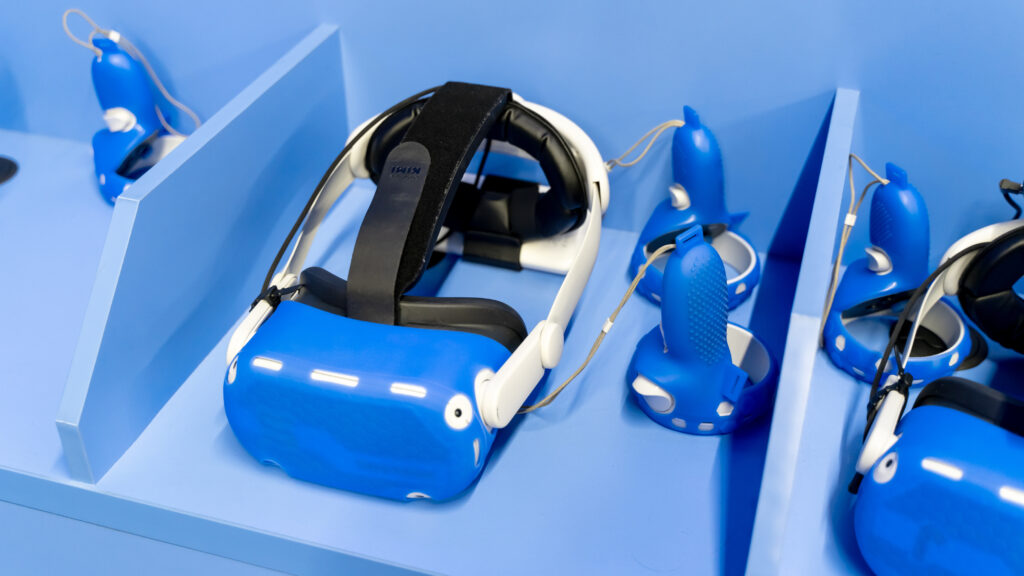
The development of new materials also enables more efficient and sustainable solutions. Materials such as amorphous alloys, metal foam, nanocrystalline materials, self-repairing materials and advanced alloys may have the potential to revolutionize carbon capture, transport and storage technologies. These materials can enhance performance of existing systems and facilitate the design of more robust and flexible solutions.
Technological progress by use of AI will not only impact CCS, but also contribute to the transformation of the energy market. The increasing integration between CCS technologies and future energy systems highlights the need for innovation and cross-sector collaboration. More information on this can be found in the report ICEF-AI-Climate-Roadmap-Second-Edition-2024.pdf
With technological diversity as a driving force and focussing on innovation, CCS is one of the keys to achieving global climate goals. With support from CLIMIT, Norway continues to be a leader in the development of groundbreaking solutions.
“CCC technology has the potential to reduce the costs of CO2 capture. This is important for decarbonization in general and our ambitions in transport and storage. The technology will still require testing and development before it is market-ready.”
Gelein DeKoeijer, Specialist R&D CO2 Capture at EquinorThe development of compact facilities for carbon capture from small to medium-sized point emissions is crucial for the success of CO2 management, driving the additional CO2 emissions reduction needed to meet global climate targets large parts of the carbon-intensive industries, including oil and gas and broader industrial operations. CLIMIT therefore provides significant support to technology projects that pave the way for the commercialization of such facilities.
One of CLIMIT’s areas of focus are the development of innovative technology and solutions. This is also one of CLIMIT’s performance targets which focuses on the development of new ground-breaking CO2 handling technologies.
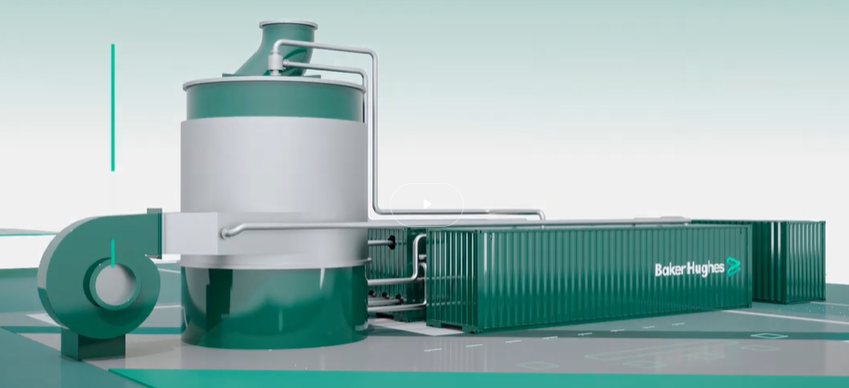
Baker Hughes Compact Carbon Capture technology is a CO2 capture solution that uses centrifugal forces to distribute solvents, improving mass transfer and efficiency in the capture process. This technology has been developed to reduce the space required for a carbon capture plant. This can help reduce the “footprint” by up to 75 percent, which in turn reduces investment costs by up to 50 percent compared to conventional technologies. The compact size makes it possible to offer easier retrofittable, modular and scalable units for small to medium-sized point emissions that can be more easily integrated into existing facilities in industry and on offshore installations.
Innovation from idea to finished commercial product requires time and resources. CLIMIT-Demo answers this challenge with financial contributions to the development of solutions that can make important contributions to cost reductions and the wide international spread of CO2 management. The developers of the Compact Carbon Capture technology received the first pledge of support in 2007 and until 2024 have received a total of NOK 88 million. On average, this support has accounted for 54 per cent of total development costs. An ongoing project is supported with NOK 20 million, which constitutes 47 per cent of the development costs.
Traditional carbon capture involves the use of relatively tall absorption columns (towers) where the flue gas meets CO2-binding solvents. This method often requires large facilities with tall structures, which limits the areas of application and entails significant investment costs.
Fjell Technology Group, together with partners, has developed a compact solution by using rotating technology that increases the contact surface between the solvent and the exhaust gas. With this method, the time the flue gas needs in the capture unit (absorption part) is reduced, and provides more efficient and faster regeneration of solvent in the desorber part. In this way, the plant becomes smaller and more efficient. The technology is solvent neutral, meaning it can use different types of solvents, including those that are more concentrated and viscous, to absorb CO2 more efficiently. See sketch of the technology below from Baker Hughes.
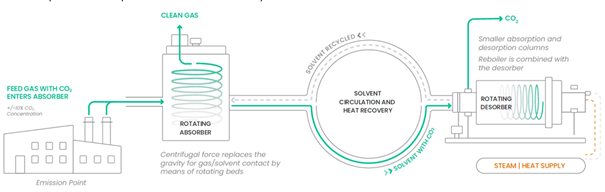
The collaboration between Fjell Technology Group, Equinor, Sintef, and CMR Prototech started in 2007. The group developed a compact desorber that separates CO2 from the solvents after capture. After a break in the development of the absorber part, Fjell Technology Group took up the task again in 2015, with support from the CLIMIT program and funding from Equinor. An international recognition of the solution occurred in March 2020 when the Compact Carbon Capture technology was recognized as an Energy Innovation Pioneer during IHS Markit’s CERAWeek (Cambridge Energy Research Associates).
This was decisive for the progress of the project, and led to the establishment of the company Compact Carbon Capture AS which became part of Baker Hughes later in 2020.
“Baker Hughes focus is on improving the economic viability of CCUS projects at scale and applying our core technologies across other industrial sectors. We have capabilities in post-combustion capture, compression, subsurface storage, and long-term integrity and monitoring of reservoirs. Compact Carbon Capture technology complements our strategy, technology and manufacturing strengths in the area of carbon capture.”
Torleif Madsen, Venture leader in Baker HughesIn November 2020, Baker Hughes announced that it had entered into an agreement to purchase the company Compact Carbon Capture AS. This was part of the company’s strategy to lead the way in the energy transition, by offering solutions for the decarbonisation of carbon-intensive industries. Baker Hughes isaccelerating the development of the Compact Carbon Capture technology for commercial use globally, with the aim of being able to offer one of the industry’s lowest costs per tonne of captured CO2.
The collaboration with Equinor and Sintef continues in an ongoing CLIMIT-supported project led by Baker Hughes’ Norwegian subsidiary, Compact Carbon Capture AS.
Protonic Membrane Reformer (PMR) technology was developed through projects 618191 [1] and 620208 [2], led by CoorsTek Membrane Sciences. This is a single-stage process for converting natural gas into hydrogen.
Steam methane reforming and water-gas shift occur inside catalytic membrane tubes and the separation of hydrogen occurs by electrolytically pumping it across the membranes so that hydrogen is transported as protons to the outside of the membrane. This allows carbon capture to become an integrated part of the process and also involves a high degree of heat integration. The project results were published in a 2022 Science article [3], “Single-step hydrogen production from NH3, CH4, and biogas in stacked proton ceramic reactors”.
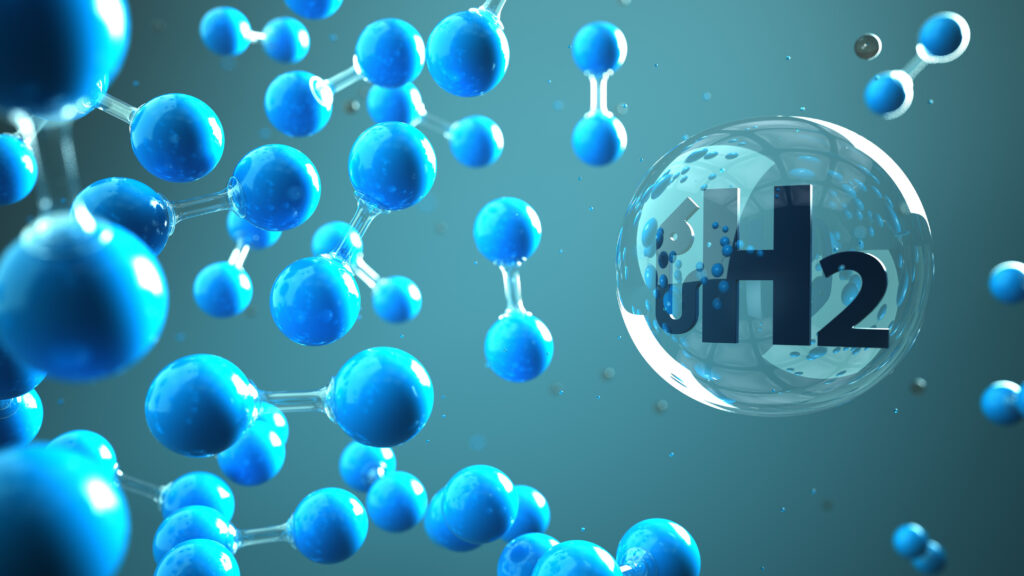
Project 618191, which was carried out over the period 2019-2020, aimed to increase the maturity of this technology. The project’s three work packages focussed on: the development and production of membranes, performance testing and developing simulation models. The production method for complete membrane stacks was developed and the devices produced were tested under industrial conditions.
Project 620208, which was carried out from 2020 to 2022, built further on the results from Phase I. The primary goal was to scale up the technology through pilot testing. The project included performance and lifetime testing and engineering, building and testing of two pilots with a capacity of 2kg of hydrogen per day. Lifetime testing reached 3,100 hours, and the results confirmed high performance in the production of high purity hydrogen.
CoorsTek Membrane Sciences’ most recent initiative with protonic membrane reformer technology focuses on ammonia as an energy carrier. The EU Horizon project “Electrified Single Stage Ammonia Cracking to Compressed Hydrogen” (2023-2026) [4] aims to further develop the technology for converting ammonia into hydrogen through a single-step process.
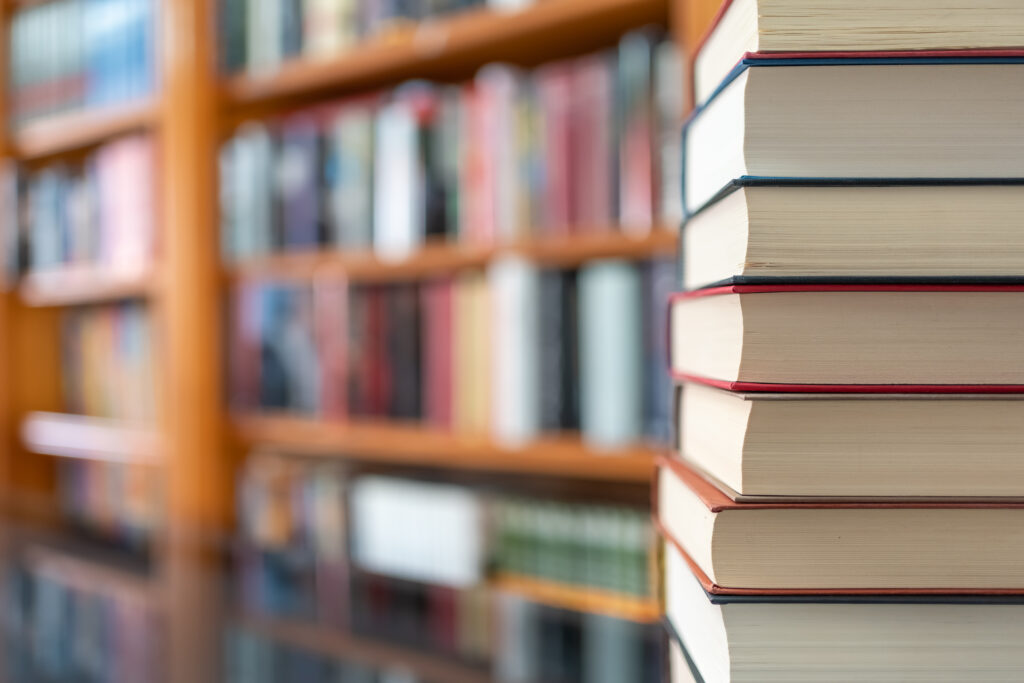
- 618191 Protonic membrane reformer technology for conversion of natural gas to hydrogen and CO2. https://climit.no/en/project/protonic-membrane-reformer-technology-for-conversion-of-natural-gas-to-hydrogen-and-co2/
- 620208 Conversion of natural gas to hydrogen and compressed CO2 using protonic membrane reformer technology — PROTONIC Phase II. https://climit.no/prosjekt/conversion-of-natural-gas-to-hydrogen-and-compressed-co2-using-protonic-membrane-reformer-technology-protonic-phase-ii/
- Science publication; Electrochemical production of hydrogen from natural gas. https://climit.no/en/news/science-publication-electrochemical-production-of-hydrogen-from-natural-gas/
- Electrified Single Stage Ammonia Cracking to Compressed Hydrogen. https://prosjektbanken.forskningsradet.no/en/project/EU/101112144?Kilde=EU&distribution=Ar&chart=bar&calcType=funding&Sprak=no&sortBy=date&sortOrder=desc&resultCount=30&offset=60&Organisasjon.3=SINTEF+AS&source=EU&projectId=101112823
Since its establishment in 2005, the CLIMIT programme has supported the development of carbon capture and storage technologies. This also includes technology development for the use of fossil-free fuels. Under the BIGH2 umbrella, SINTEF has worked, together with research partners and industry, on the use of hydrogen and ammonia in gas turbines since 2007. These projects have contributed to new knowledge and new gas turbine burner designs. The technology is now ready to take the next step to full-scale demonstration.
The first two projects under BIGH2 started in 2007: “Enabling Pre-Combustion CCS Plants (SP 1 and SP 2)” (1820701 and 1820702). The projects focussed on hydrogen combustion with low NOX formation and had a long-term goal of developing new gas turbine burner technology for hydrogen combustion with NOX emissions of less than 10 ppm. Numerical flow simulations, together with literature studies and laboratory studies, were a central part of these projects. This also included direct numerical simulation (DNS) of the turbulent flow around the fuel nozzle. An important result of “BIGH2 Innovation / Phase I” was the understanding that traditional fuel injection through fuel nozzles and crossing jets is a critical design problem for hydrogen-fired combustion systems.
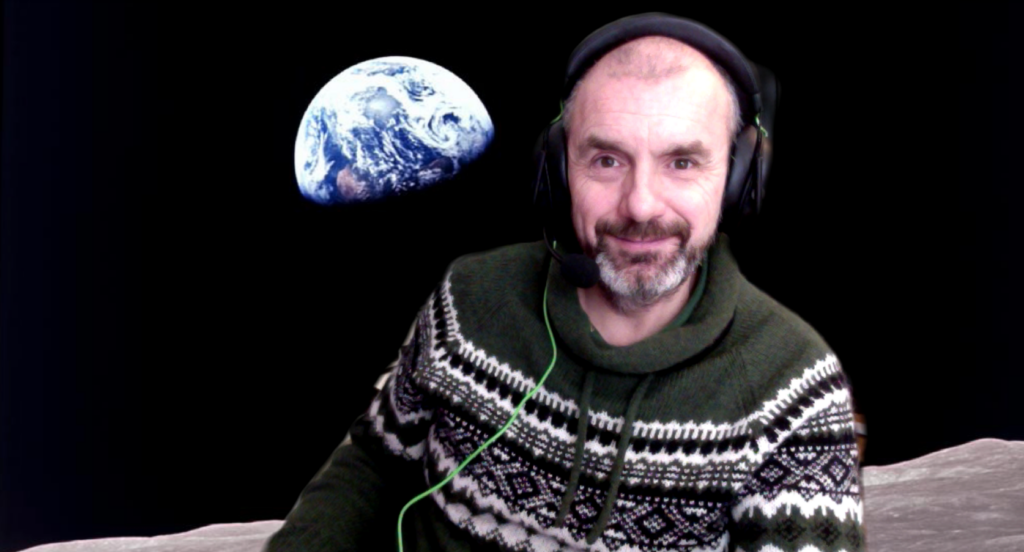
In 2012, “BIGH2 Innovation / Phase 2 (203716)” began with a focus on developing a new burner concept for Alstom’s GT24/26 gas turbine. This involved lean premixed combustion of hydrogen-rich fuels in stationary gas turbines. The ambition for low NOX emissions as well as the efficiency of the turbine was maintained and continued. The project carried out numerical simulations and tested burner models, as well as full-scale demonstration of Alstoms B-EV gas turbines fired with up to 47% (vol.) hydrogen mixed with natural gas.
In the project “BIGH2 / Phase III (617137)”, which started in 2017, the focus was expanded from hydrogen as a fuel to also include ammonia. The goal was the same as the previous projects – use hydrogen-based fuels in gas turbines with low NOX emissions without reducing efficiency. The project started by developing a chemical kinetics scheme for hydrogen/ammonia flames adapted to combustion in gas turbines. The research demonstrated, through advanced numerical simulations and laboratory experiments, that the optimal method for burning ammonia in a gas turbine is through the use of a Rich-Quench-Lean (RQL) strategy in the design of the combustion chamber. Finally, the project also demonstrated low NOX hydrogen firing in a Siemens industrial gas turbine (SGT-600).
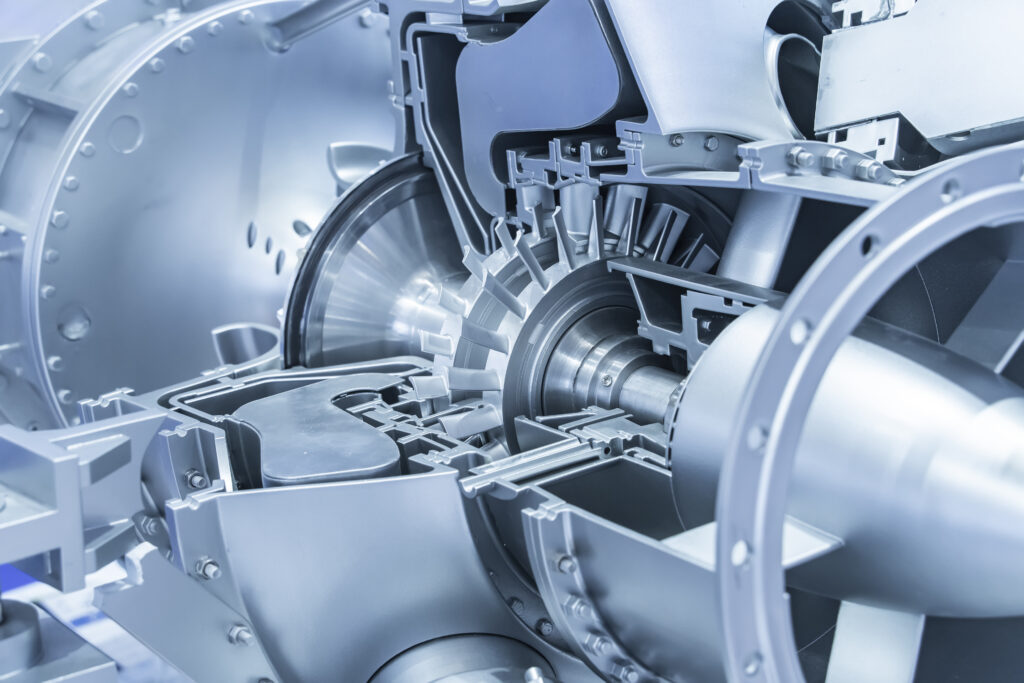
The last project in the series, “BIGH2 Innovation / Phase 4 (623349)”, was approved in 2023 and is still ongoing. This project continued the collaboration with Siemens and aims at full-scale demonstration. The project will develop, test and demonstrate the safe, efficient and clean combustion (low-NOX) of hydrogen and ammonia as fossil-free energy carriers in an advanced and state-of-the-art gas turbine combustion system, as well as the unaffected ability to burn natural gas cleanly and efficiently as a back-up fuel in the same combustion system. This will require a radical redesign of the gas turbine’s combustion system, with axial fuel injection in two combustion stages. This approach is the key to achieving the desired flexibility for different types of fuel such as hydrogen, ammonia and natural gas. This enables the removal of CO2 from gas turbines without loss of efficiency and with clean combustion (low-NOx). It will provide important contributions to the CO2 value chain by decarbonising industry and energy resources, at the same time as also laying the foundation for new technology and solutions.
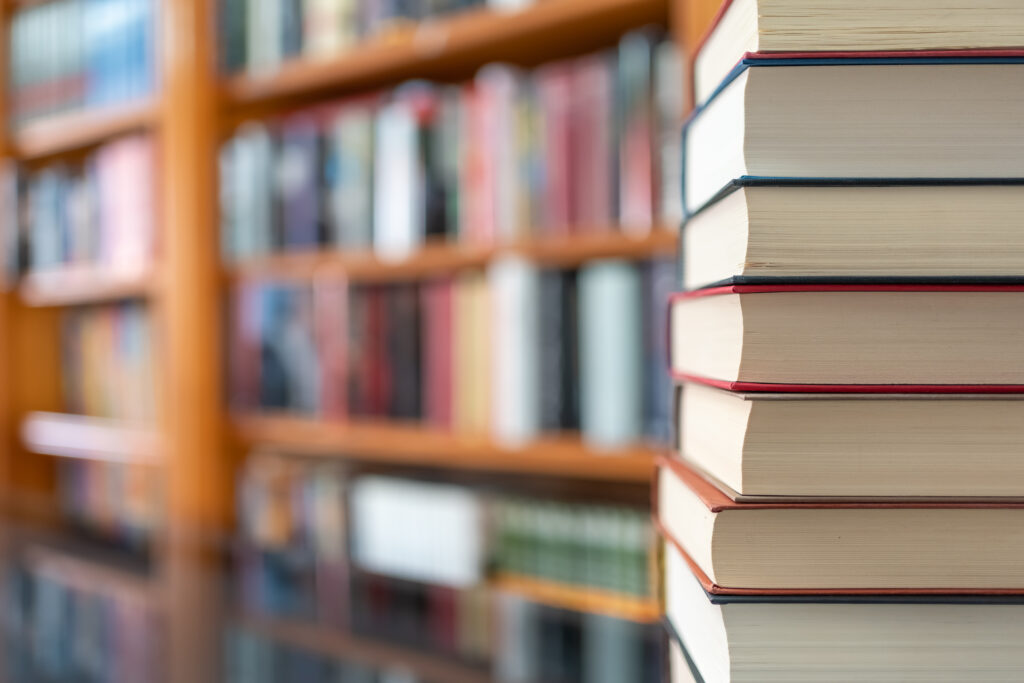
Hydrogen Mem-Tech AS (Reinertsen New Energy), in collaboration with SINTEF, has developed a palladium-based membrane technology to separate hydrogen from natural gas or biogas-based hydrogen production. CLIMIT has supported this work since 2011 and the technology is now commercialised.
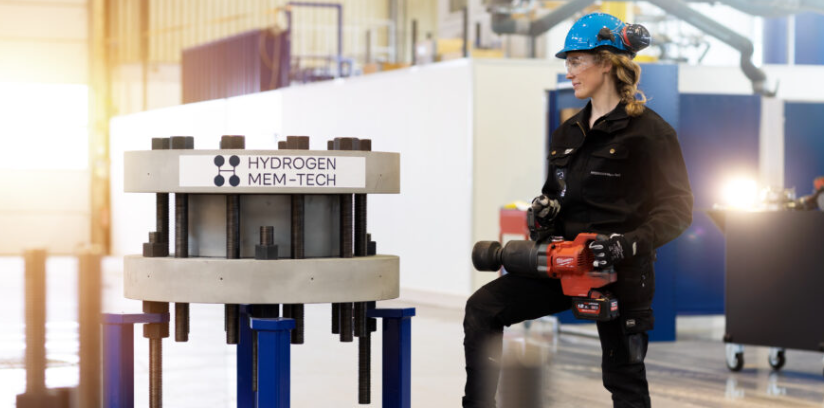
Support was first provided in 2011 for the project “CO2 purification using hydrogen membranes (212745)”. This initiative was based on SINTEF’s patented technology for the production of palladium membranes with a thickness of down to 1-2 µm. Membranes are used to separate hydrogen from other gases during hydrogen production based on natural gas or biogas. In 2015, work started on scaling up and establishing a pilot facility at Equinor’s methane production facility at Tjeldbergodden, “CO2-capture and hydrogen production by use of Pd-membranes (241447)”.
“It is fair to say that CLIMIT has played a central role in the development of the technology that laid the foundation for creating a separate company, which has attracted interest and support from investors. Today, the company has 17 employees, and employs more FTEs at home and abroad. Our most important areas right now are markets within oil and gas-related industries, steel production and shipping.”
Thomas Reinertsen, CEO, Hydrogen Mem-TechIn 2017, Hydrogen Mem-Tech was established and the technology was further developed through the project “Further development and long-term testing of palladium membranes for the production of CO2-free hydrogen (619114)”. This also includes pilot testing at Tjeldbergodden. CLIMIT has also supported “Enhanced lifetime of Pd-based membranes (281824)”.
Ammonia is an interesting hydrogen carrier and Hydrogen Mem-Tech’s latest initiative is in converting ammonia to hydrogen (“PALLAMONIA (332357)”).
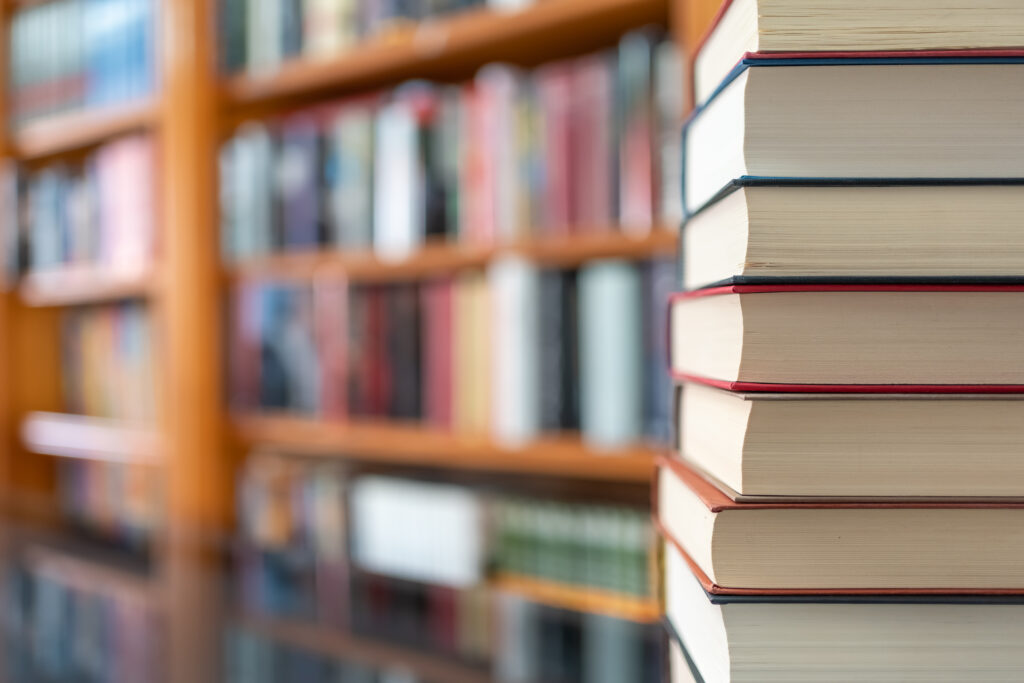
- CCS creates new industries
- 241447 CO2 capture and hydrogen production by use of Pd-membranes
- 281824 Enhanced lifetime of Pd-based membranes
- 332357 PALLAMONIA
Most products shipped to the market are produced through industrial processes that often involve significant carbon emissions. To achieve our climate goals, it is therefore important that industry finds good solutions to remove or reduce environmentally harmful emissions as much as possible.
“For more than 20 years, the CLIMIT programme has helped create change. Funding for the development of carbon capture technologies and pilot-scale testing under real-world conditions has been and is still of great importance to the industry.”
Senior Adviser at Gassnova, Jørild Svalestuen.For several years, CLIMIT has funded pilot testing at stationary facilities such as SINTEF’s carbon capture pilot project at Tiller in Trondheim, Technology Centre Mongstad (TCM) and at mobile testing facilities owned by various technology providers.
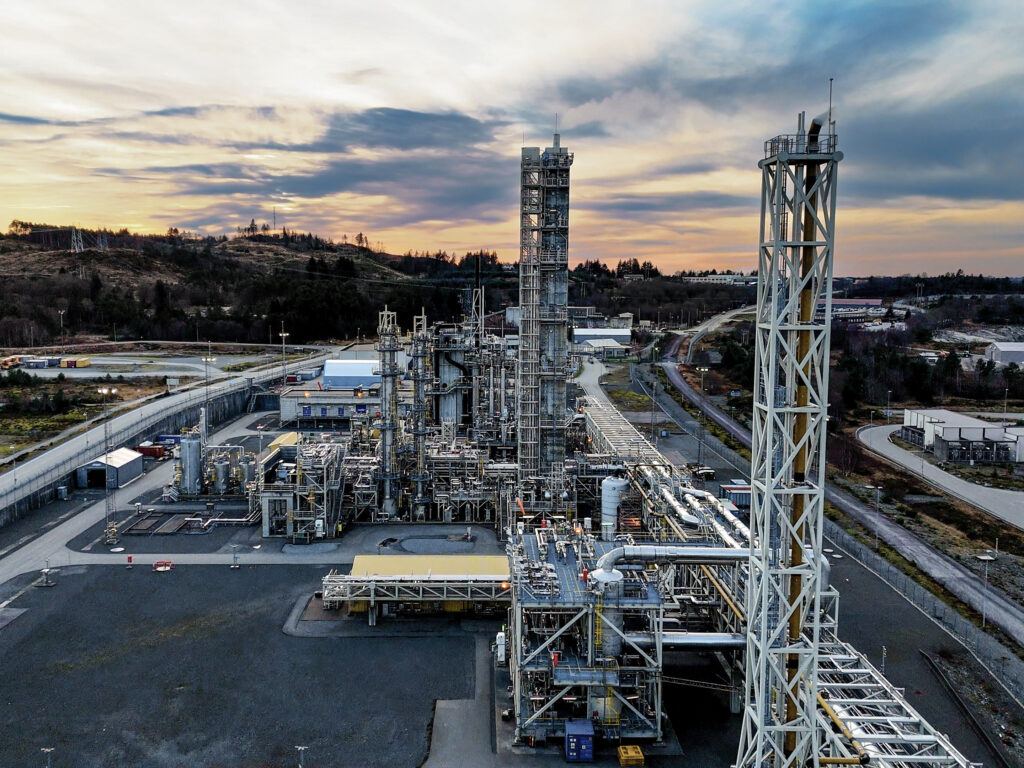
Below are examples of technology suppliers who have tested their own technology with the support of industry and CLIMIT:
- SLB Capturi (formerly Aker Carbon Capture) has, in response to industry, demonstrated its capture technology for numerous businesses using its mobile testing unit. These include Heidelberg Materials in Brevik, Hafslund Oslo Celsio, Preem AB in Sweden, Polchar in Poland, and Elkem and SMA Mineral in Mo Industrial Park. In previous phases, the amine-based solvent technology was tested and optimised in collaboration with NTNU and SINTEF. The technology has been further tested, developed and qualified at TCM for larger scale use.
- Hydrogen MemTech technology, which separates hydrogen from CO2, has been tested under real-world conditions at Equinor’s Tjeldbergodden plant.
- Baker Hughe’s Compact Carbon Capture technology was developed in Norway trough a collaboration between Fjell Technology Group, Equinor and SINTEF – with the support of CLIMIT. The technology was previously tested at Equinor’s pilot facility in Porsgrunn.
- The Moving Bed Carbonate Looping technology from the Fjell Technology Group is being developed in collaboration with NTNU and SINTEF. This will be tested through a pilot project, and a mobile unit is under construction for testing under real-world conditions.
- Air Products in Kristiansand has tested two types of membranes for carbon capture at Heidelberg Materials in Brevik. They have also recently completed long-term testing at Returkraft in Kristiansand. SINTEF’s patented carbon capture technology CSAR (Continous Swing Absorption Reactor), will be piloted at BIR – Bergensområdets Interkommunale Renovasjonsselskap (Bergen-area Intermunicipal Renovation).
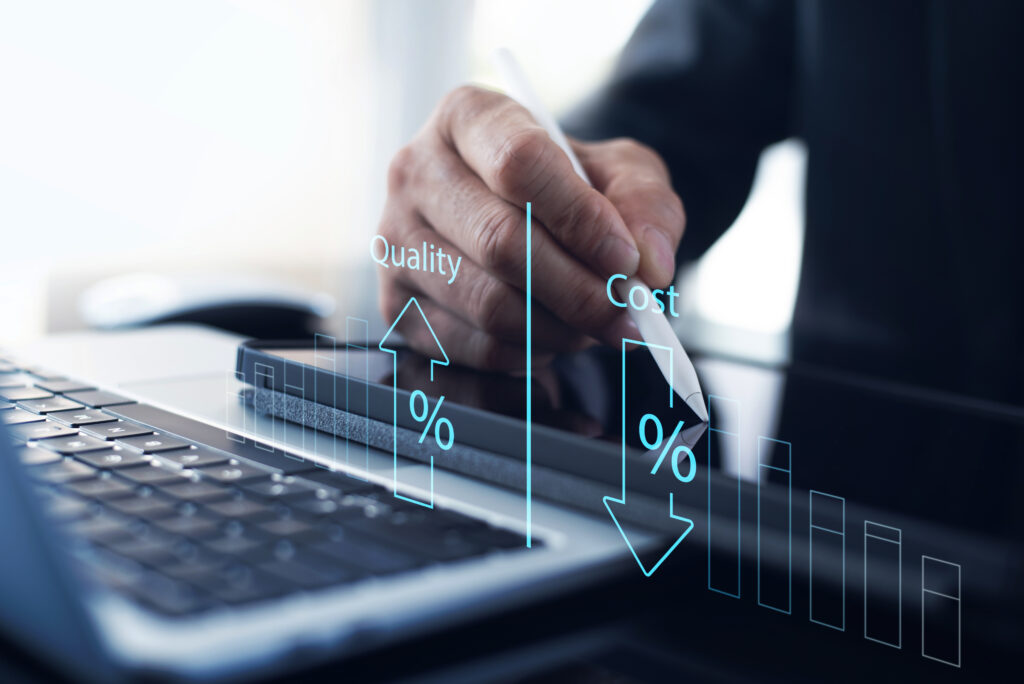
Pilot facilities are small-scale processing facilities where technology providers can test out their technology on a smaller scale. For a technology to advance up the TRL (Technology Readiness Level) scale and succeed in commercial competition, the use of pilot facilities is a vital tool for fine-tuning the technology. Challenges can be identified and resolved on a smaller scale, reducing the risk of costly mistakes when scaling the technology up for fullscale facilities. This also allows for improvements and innovations that can make technology even more cost-effective over time.
This also applies to carbon capture, where both stationary and mobile pilot facilities are used to test important parameters for the performance and operation of a capture facility.
To meet climate goals, carbon capture technology is a key component for large parts of the processing and waste industries, nationally and internationally. For technology providers, it is essential to test technology under real-world industrial conditions. It is not possible to simulate or predict all the challenges that a technology will face in a real-world industrial context. As such, thorough testing at pilot facilities can avoid costly mistakes.
Testing at pilot facilities also provides valuable knowledge and learning, both for technology providers and technology users (industry). It is important to understand how the technology reacts under real-world conditions, especially concerning the rate of carbon capture, energy consumption, potential environmental emissions, and other operating conditions of the capture facility. This gives technology providers and their customers the opportunity to evaluate and optimise the performance of their capture facility. This ensures that the technologies are sufficiently robust for fullscale implementation on a given industrial waste gas/flue gas.
It is also important for the customer buying a CCS facility to remove their emissions to understand the knowledge and resources required to operate such a facility, and how its operation is affected by changes in the waste gas from the production process. Changes in the waste gas as a function of changes in the production process may affect the performance of the capture facility.
It is also important for the customer purchasing a CCS facility to understand the kind of knowledge and resources required to operate such a facility, and how its operation is affected by changes in the flue gas from the production process. Changes in the flue gas as a function of changes in the production process may affect the performance of the capture facility.
“This is why it is essential for industry to acquire knowledge about the technology they will use in their factories or waste facilities. This also applies to the knowledge required about the preparatory work and changes in infrastructure at and around the industrial facility,” says Svalestuen. She emphasises that the “Lesson Learned Report” from the Longship project shows that 34 percent of costs associated with carbon capture are related to infrastructure (“Utility and Support Systems”). An early phase of pilot testing is very useful for both technology providers and technology users. This is especially true for industries where carbon capture has not been tested before.
Elkem is a world-leading manufacturer of advanced silicon-based materials. Carbon capture is part of Elkem’s climate strategy to reach net zero emissions by 2050.
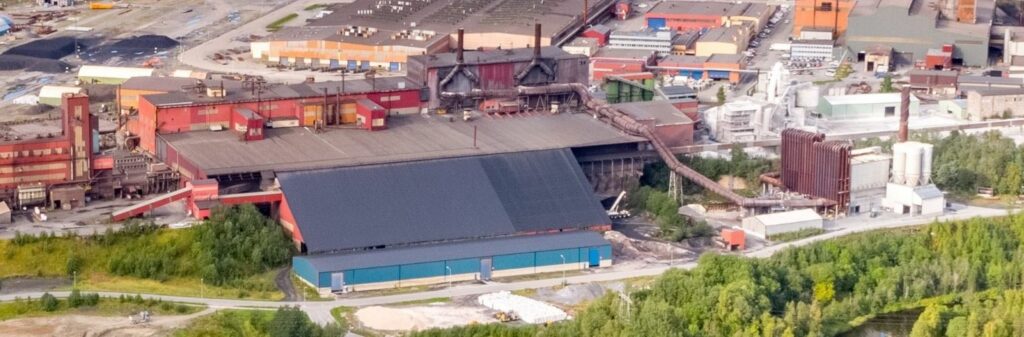
At the Rana facility, the company has completed a carbon capture pilot project using capture technology provided by SLB Capturi (formerly Aker Carbon Capture). The pilot recorded high capture rates, up to 95%, demonstrating that the technology is practical and viable at a smelting plant.
“The high capture rates, combined with low amine degradation, show the technical efficiency of the technology.”
Elkem’s Climate Director, Trond SæterstadThe flue gas from silicon smelters has low and varying CO2 concentrations. The fact that the pilot project successfully captured this CO2 offers invaluable learning for further development. This CCS pilot project was in operation for around 3,000 hours from November 2022 to June 2023.
The results of the pilot will be used to continue the maturation of the technical and commercial aspects for the potential future implementation of CCS.
“Reducing implementation costs and attracting competitive framework conditions are also key elements of this process,” Sæterstad says.
The project received funding from CLIMIT and was a collaboration between Elkem and Mo Industrial Park, SINTEF, Alcoa, Celsa, Ferroglobe, SMA Mineral, Norcem, Norfrakalk, Arctic Cluster Team and SLB Capturi.
Since 2005, the CLIMIT programme has been a key financial supporter of the development of cost effective carbon capture and storage (CCS) technologies.
The SOLVIT project, which started in 2008, laid the basis for environmentally-friendly solvent development, and the solutions from this are now used commercially. Through many projects, including SOLVIT, Aerosolve and the ACT/CEPT project Scope, SINTEF has developed world-leading expertise within solvent development and environmental impact.
CLIMIT’s support has also facilitated bilateral support from CLIMIT and the US Department of Energy, which has led to further technological progress.
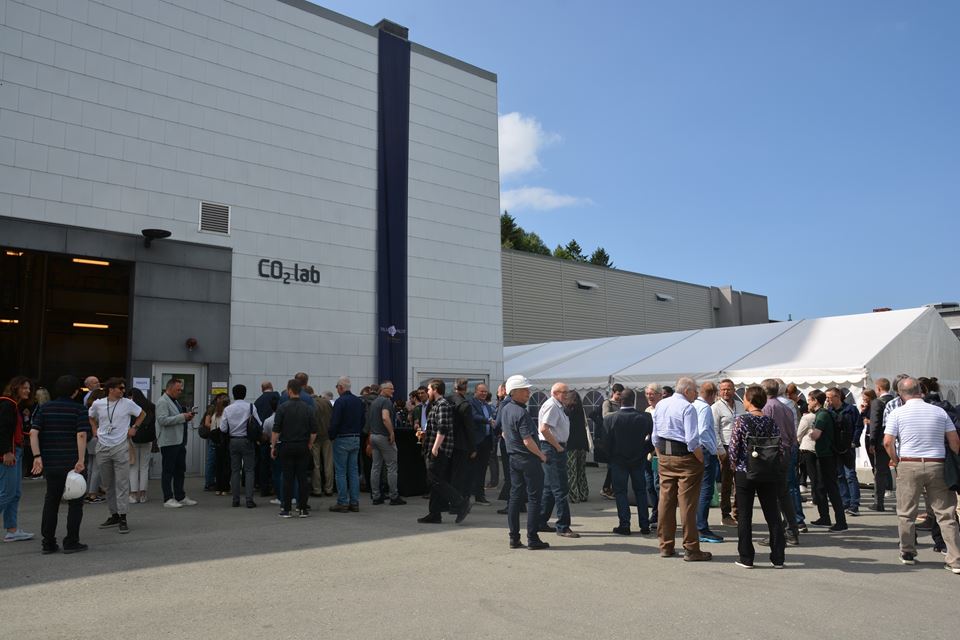
In June 2023, SINTEF marked 100,000 operating hours at its Tiller plant for researching carbon capture. This milestone work underscores SINTEF’s role as an important centre for expertise within carbon capture in particular, but also all areas of CCUS and CDR. SINTEF’s expertise within these areas has been important for Norway’s long-term focus on CCS as a key technology for achieving both national and global climate goals.
The pilot plant at Tiller was originally developed by SINTEF in collaboration with SLB Capturi (formerly Aker Clean Carbon). With a test plant that can capture up to 50 kg CO2 per hour, SINTEF has tested and optimised carbon capture technologies under real-world conditions. The plant is able to take precise measurements for energy requirements, capture rate, degradation of solvents and environmental impact, which has provided researchers with valuable data for optimising large-scale plants.
“The plant at Tiller provides direct insight into how carbon capture works at industrial scale. This allows us to uncover challenges, reduce risks and ensure that the technology works as best as possible, before further testing and verification at the Test Centre Mongstad (TCM) and implementation in major projects.”
Eirik Falck da Silva, Research Manager at SINTEF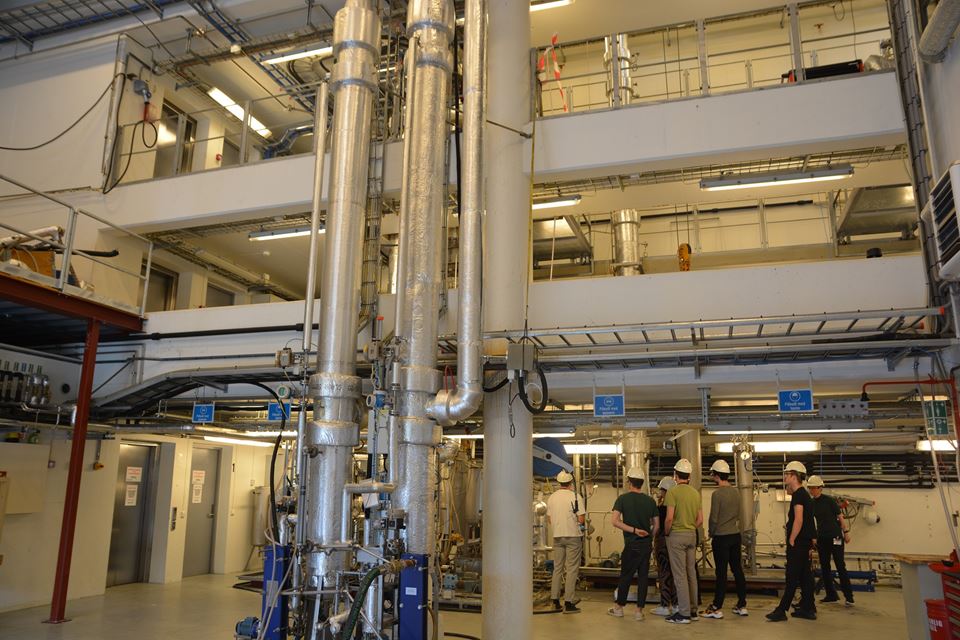
“The Tiller plant has proven to be an optimal scale for testing and developing technology, as it is owned and operated by a leading research community, which develops solutions from laboratories and in the form of models. As such, experience from Tiller can be reused in further work and also lay the foundation for further testing at a larger scale.”
Karl Anders Hoff, SINTEFSINTEF has played a key role in the development of a number of key capture technologies, such as:
- SLB Capturi’s technology, which is now used industrially, including at Heidelberg Materials’ cement factory in Brevik and in the planned capture project at Hafslund Celsio, both of which are part of the Longship project.
- CESAR1 technology, an open technology developed in collaboration with the Test Centre Mongstad (TCM) and international partners.
- NAS technology, developed by RTI International and tested at Tiller and TCM and later licensed to SLB.
SINTEF’s work at Tiller has contributed to the development of methods for monitoring and avoiding emissions from capture facilities and increased understanding for how operational variations and dynamics in flue gas can be best managed by the capture facility. These are solutions that are crucial for the cost-effective operation of capture facilities.
“The CLIMIT programme has supported the development of many of the solutions now adopted for full-scale carbon capture. This has placed Norwegian academic communities in a position to deliver high calibre research and technology development. These solutions will facilitate significant reductions in carbon emissions from industry.”
Karl Anders Hoff, SINTEFWith support from the CLIMIT programme, SINTEF has achieved ground-breaking results which has both contributed to Norway’s CCS ambitions and international development within the field. Their research and development have been crucial for taking CCS technologies from the laboratory to full-scale use.
As an expert within CCS, SINTEF is important for both technology suppliers and users. SINTEF’s test laboratories, which include analysis equipment with low detection levels, and stationary test pilots have been vitally important to the development of carbon capture technology.
The CLIMIT programme has shown how collaboration between research, industry and the authorities can accelerate the development of solutions that contribute to meeting the world’s climate challenges.
“Stable funding over time has been incredibly important for developing our position within carbon capture research. CLIMIT has played a central role in this context.”
Eirik Falck da Silva, SINTEFCLIMIT’s support for CCS projects
The CLIMIT programme, led by Gassnova in partnership with the Research Council of Norway, is Norway’s national funding programme for the development of cost-effective carbon capture and storage (CCS) projects. For 20 years, CLIMIT has funded almost 800 projects to the tune of NOK 5.2 billion. This support has triggered equivalent investments from industry. The programme has been crucial for the development of CCS technologies, both nationally and internationally.
Both the Test Centre Mongstad (TCM) and SINTEF’s pilot plant at Tiller in Trondheim and have been an important Norwegian arena for testing and developing carbon capture technology. Many projects have received significant funding from CLIMIT to carry out research and testing at Tiller in Trondheim. These technologies were later tested at TCM. Some of these include:
-
- The SOLVIT programme
-
- Support from CLIMIT: NOK 132 million
-
- Share of total project costs: 40%
-
- The SOLVIT programme
-
- The Aerosolve project
-
- Support from CLIMIT: NOK 23 million
-
- Share of total project costs: 50%
-
- The Aerosolve project
-
- The ACT/CEPT project Scope
-
- Support from CLIMIT: NOK 6.9 million
-
- Share of total project costs: 65%
-
- The ACT/CEPT project Scope
-
- The Non Aqueous Solvents (NAS) projects
-
- Support from CLIMIT: NOK 12 million
-
- Share of total project costs: 63%
-
- The Non Aqueous Solvents (NAS) projects
By funding research, pilot projects and technology development, CLIMIT has played a crucial role in promoting CCS as an instrument for reducing greenhouse gas emissions. CLIMIT’s contribution has not only accelerated the development of cost-effective solutions but also strengthened Norway’s position as a leading stakeholder within CCS globally.
The programme contributes to building bridges between research communities and industry.Support from CLIMIT has facilitated the testing of new technologies under real-world conditions at SINTEF’s pilot facility, TCM, and at industry facilities in Norway and abroad. This is an important link in ensuring the commercialisation of new solutions that can contribute to achieving national and international climate goals.
CLIMIT continues to be a central driving force for innovation within CCS and an important contributor in the development of solutions for a sustainable future.