New ACT announcement
The purpose of the call is to support research and innovation that leads to implementation of technology for large-scale carbon capture, utilisation and storage (CCUS).
A secondary goal is to strengthen international cooperation in CCUS.
About the call for proposals
ACT stands for “Accelerating CCS Technologies” and is an international collaboration where funding agencies from several countries collaborate on joint calls for CCUS projects. ACT’s fourth call for proposals, ACT4, will be published in spring 2022 with the deadline 12 September 2022.
Grant applications for the international ACT4 call can be submitted as described on ACT’s website. Norwegian partners who participate in applications for the international ACT4 call must in addition submit an application under this call, which is the Norwegian ACT4 call.
Applications for the Norwegian ACT4 call must only include Norwegian partners and Norwegian activities that form part of a bigger international ACT4 project.
The applications must fall under the topics described in CLIMIT’s work programme.
The Norwegian-language call for proposals is the legally binding version.
CLIMIT support means Preem is ready for CCS
CLIMIT, together with the Swedish authorities, has supported Preem, one of Sweden’s largest CO2 emitters.
The company has two refineries on the west coast of Sweden, one in Lysekil and one in Gothenburg. Preem is exploring the possibility of fullscale CCS using storage in Norway.
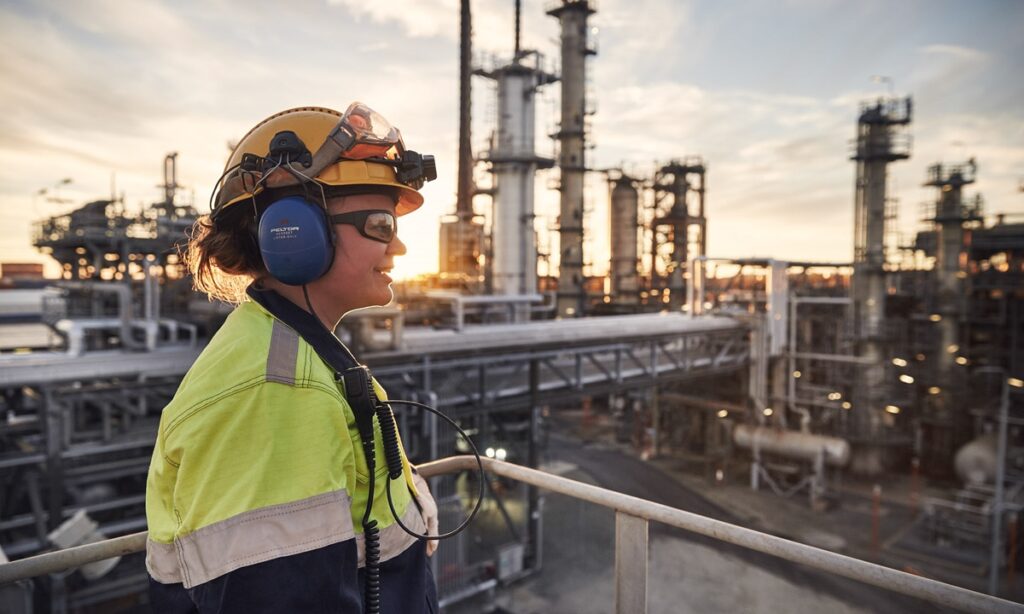
Implementation at existing facilities
The primary goal of the project was to research the possibility of implementing fullscale carbon capture from Preem’s hydrogen production unit (HPU) at Preemraff Lysekil in Sweden and to produce liquid CO2 for permanent storage underneath the west coast of Norway in accordance with specifications and requirements set out in the Longship initiative.
SINTEF Energi AS, Equinor Energy AS, Aker Carbon Capture AS and Chalmers University of Technology have all been involved in the project in one way or another, and publications have been and continue to be released and a number of webinars relating to the project have also been held.
Activities completed during the project
- Carbon capture demonstration at the hydrogen production unit at the Preem refinery in Lysekil. The production unit is based on steam methane reforming (SMR). For the demonstration, pilot-scale carbon absorption was tested through the use of Aker Carbon Capture’s mobile testing unit (MTU).
- Extrapolation of the results of the demonstration so that they can be understood in connection with the work on the fullscale implementation of carbon capture from HPUs and other major emissions sources at the Lysekil refinery and Preem’s refinery in Gothenburg.
- In-depth examination of opportunities around energy efficiency in the CCS value chain, including recycling and the use of residual heat at the refinery which can be used to run the process for solvent recovery as well as using alternative solvents for carbon capture.
- Evaluation of the technical feasibility and cost to the CCS value chain, including carbon capture and transport by ship to storage facilities off the west coast of Norway.
- Research into relevant legal and regulatory aspects of carbon transport and storage across borders and national goals for emissions reductions in Norway and Sweden.
Two publications are publicly available:
- D5.1 Preem CCS – Synthesis of main project findings and insights
- Available online in the Chalmers archive: https://research.chalmers.se/publication/528685
- D4.2 Legal and regulatory framework for Swedish/Norwegian CCS cooperation
- Available online in the SINTEF archive: https://hdl.handle.net/11250/2984155
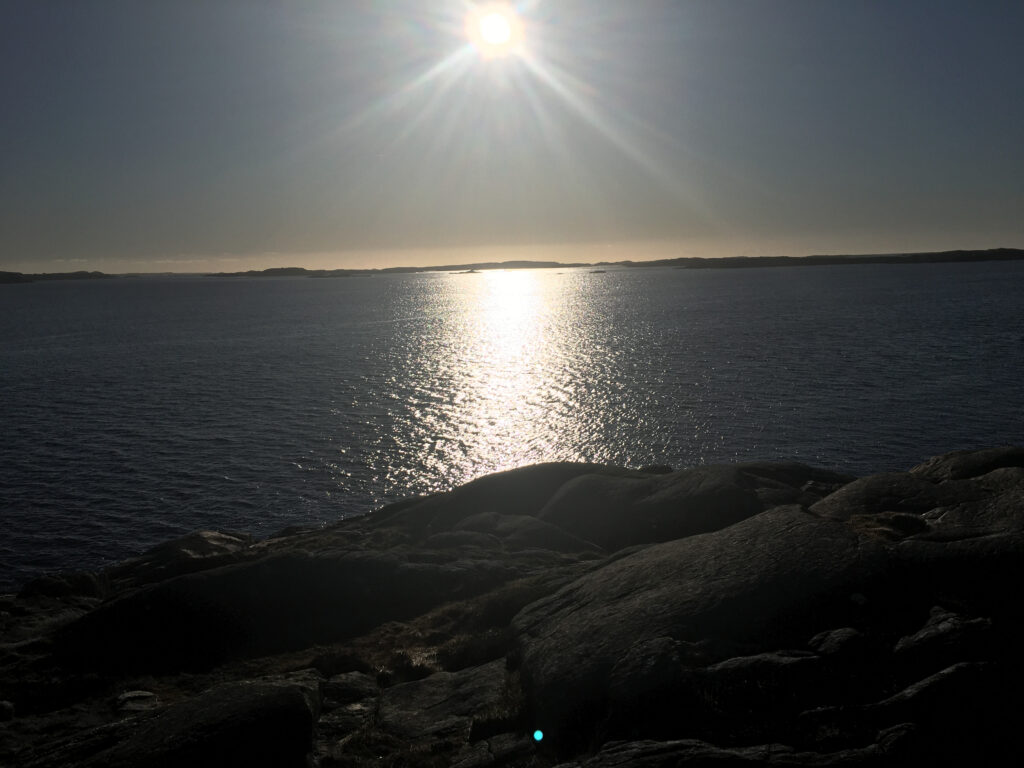
Clean waste incineration
Combustion of waste produces large amounts of CO2 that is emitted directly to the atmosphere. Statkraft’s plant at Heimdal gives off 240 000 tonnes annually.
Currently, the company is heading a feasibility study on how CO2 from incineration can be captured, transported and stored.
Statkraft’s plant at Heimdal incinerate waste from the entire mid-Norway. The district heating plant sends heated water in pipelines to housing associations and institutions such as St. Olav’s Hospital, the Norwegian University of Science and Technology, Lerkendal Stadium and the Nidaros Cathedral.
These days, Statkraft is conducting a feasibility study in cooperation with national and international players, the industrial cluster CCS Mid-Norway, Trondheim Port Authority and Trondheim Municipality.
«The content of the feasibility study is three-fold,» explains Statkraft’s Bjørn Hølaas, director of CCS. «In the technical part, we are evaluating different technologies for capture, and intermediate and permanent storage. In the commercial part, we are analysing how the framework of incentives, markets, sources of income, taxes, etc., is developing. Finally, we are investigating how the growth of the circular economy will reduce fossil content in waste – mainly plastic – since this will cut fossil emissions.»
Mature technology
Statkraft has chosen to divide the feasibility study in two parts. In one part, a technical basic concept was developed in cooperation with Rambøll Denmark, Project Invest and TCM. The second part encompasses verification, improvement and optimisation of the basic concept together with suppliers.
«We have focused on establishing a robust concept,» says Bjørn Hølaas. «Since we selected a standard monoethanolamine (MEA) solution, we don’t have to consider patent issues. The amine technology has been widely proven and is comprehensively documented. We wanted to ensure that the concept was buildable, so that the work in part two – verification, improvement and optimizing the concept – ran smoother.
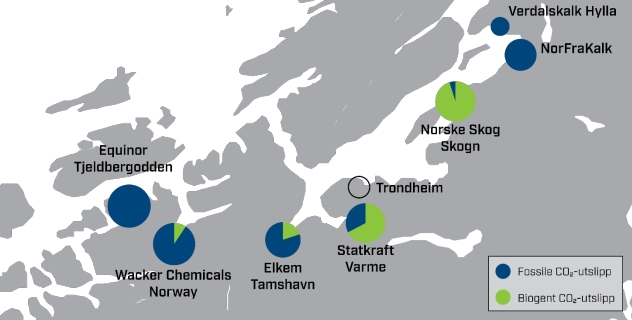
Location of players included in value chains for CO2 transport. Circles are scaled by total CO2 emissions in 2018. Ill. SINTEF / Statkraft
The value of cooperation
One of the main challenges of implementing CCS at the district heating plant at Heimdal, concerns transport and intermediate storage. Still, almost 40 percent of the costs of the basic concept is related to transport, intermediate and permanent storage. And this cost must be reduced.
Whether Statkraft chooses to hook up to the Northern Lights infrastructure – or opts for a different alternative – the company will need an intermediate storage for captured CO2. The basic concept includes an intermediate storage of 3600 tonnes. Which is about half a ship load from Northern Lights.
«As a consequence, we have sought to collaborate with other players in CCS Mid-Norway. If we can work together to identify solutions for transport and intermediate storage in Trøndelag – and this way reduce costs for all of us – implementing solutions for transport and intermediate storage, will be a realistic option,» says Bjørn Hølaas.
CCS Mid-Norway springs from the Mid-Norway industrial cluster. Companies such as Franzefoss, Elkem Thamshavn, Wacker and Equinor at Tjeldbergodden, participate in this initiative, seeking to develop a regional infrastructure for transport and intermediate storage of CO2 from the production processes.
Regulatory framework in process
An important part of the feasibility study is dedicated to developing a comprehensive overview of the commercial framework for CO2. There is great interest in EU’s certification scheme for handling CO2, which will be announced towards the end of 2022.
«EU’s new directive will give us important instructions on how we shall monitor, and report on, critical parameters along the value chain. It’s also interesting to observe how Sweden, Denmark, the Netherlands and Great Britain have organized their CO2 handling regulation regimes.»
Voluntary marketplaces for CO2 quotas and biogenic emissions – like Puro Earth and other arenas – are growing steadily, and will eventually play a decisive role.
«In Statkraft, we see the importance of partnering up with key players – in a broad cooperation with relevant authorities – in order to promote a sustainable framework,» says Bjørn Hølaas.
A robust regulatory framework ensures a level of predictability that is necessary for the industry in order to implement CCS technology. But more is needed from governmental authorities.
«Putting CCS technology to use, is crucial in order to learn from practical and operational experience – which, in turn, translates into cost reductions. In commercial terms, it will take some time before CO2 capture will be economically sustainable, so it’s imperative that governments contribute with public funds.»
CLIMIT support creates results
So, what role has CLIMIT’s played?
«The financial support is definitively crucial. But maybe even more important is it that CLIMIT supports such a wide array of CCS projects. The accumulated knowledge that is channelled through CLIMIT, is as valuable as the support we receive for our own projects. And it’s a great advantage that CLIMIT emphasizes the external communication of project results. Moreover, I believe that for those of us who work in the different industrial companies, public funding through CLIMIT gives the internal projects we propose higher legitimacy,» says Bjørn Hølaas.
The voyage towards carbon capture
Together with partners, Elkem has instigated a project for testing technology that captures CO2 from smelters. This is the first time such technology is applied to flue gas emissions in the ferroalloy industry.
The project draws on a goal-oriented, systematic effort to build competence in the field of carbon capture.
The process industry must play a central role in the struggle to achieve the overarching goal of the Paris agreement: Limiting long-term temperature increase to well below 2℃. A shift from fossil fuels to green energy, will not alone suffice to cut emissions. In fact, many industrial companies produce more CO2 than finished product. Therefore, high costs become the bottle neck for implementing carbon capture plants. This means that the research community and the industry together must find pragmatic solutions that the industry can adopt rapidly.
And one of the drivers behind CCS in the Norweigan process industry is Elkem, one of the world’s leading provider of advanced silicon–based materials.
A necessary collaboration
Bringing about substantial changes requires knowledge in new areas.
«Elkem’s voyage started around 2017,» says Elkem’s climate director Trond Sæterstad. «At that time, Elkem joined CO2 Hub Nord.» This initiative for collaboration on CCS and infrastructure, consists of industrial players in Mo i Rana industrial park and companies further north, as well as in the county of Trøndelag.
Since Elkem has production plants at several locations in Norway, the company has been a proactive contributor in an array of CCUS industrial collaborations – such as the Eyde cluster, the Mid-Norway cluster, in addition to CO2 Hub Nord. The latter is currently starting up tests of CO2 capture from the flue gases of Elkem and SMA Mineral.
In these cluster projects – all of which receives financial support from CLIMIT – the member companies are investigating solutions for CCS, local infrastructure and logistics.
«It’s a huge advantage for adjacent industry to collaborate in order to establish sound solutions for local infrastructure and logistics. That’s why the cluster projects are so important. This way, it’s possible to source large volumes of CO2 for storage, and the companies can share costs related to infrastructure and transport,» says CLIMIT’s Jørild Svalestuen.
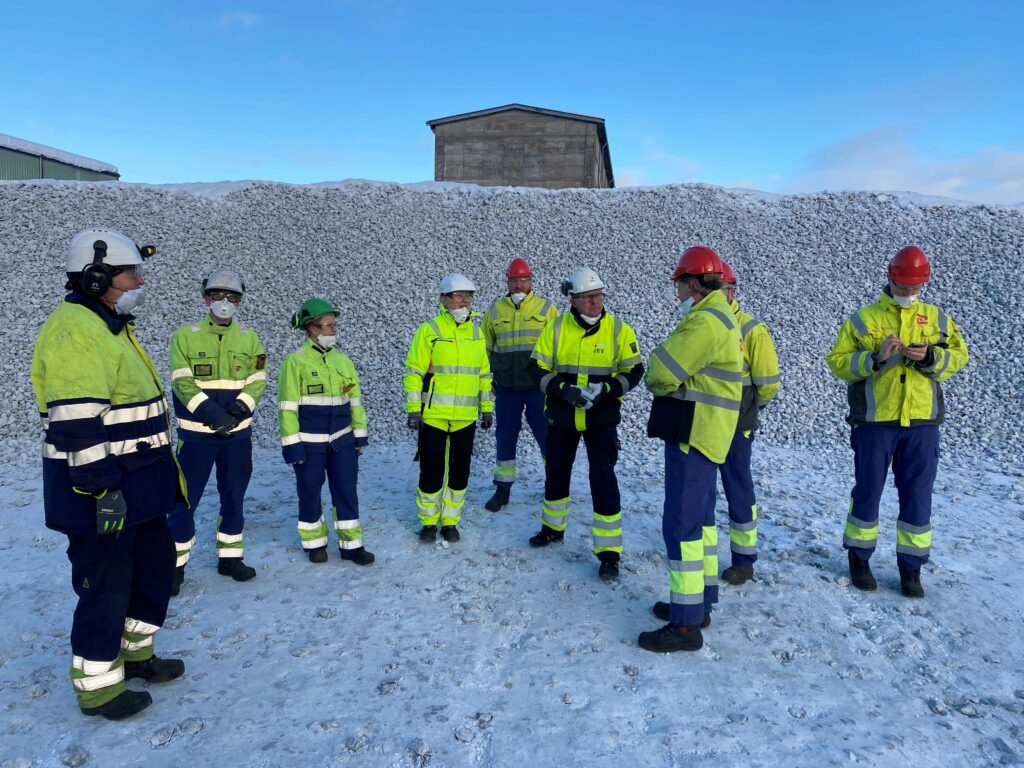
A learning process
Elkem has focused on several areas.
Between 2015 and 2019, the company participated in the CLIMIT-supported project CO2stCAP, a cooperation between Norwegian and Swedish industrial companies and research communities. The purpose was to analyze processes and identify factors that drive down costs in carbon capture projects.
Elkem also participated in Process 21, a cooperation and knowledge sharing initiative between Norwegian companies. The forum directed attention toward identifying solutions to reduce the total emission of the national process industry. The steering committee was headed by Håvard Moe, Elkem’s senior vice president for technology.
In 2021, Elkem launched the Global Climate Roadmap. This strategy defines CCS as central to reaching the company’s goal of sustainable production of materials.
A study of opportunities
Through this multi-faceted work, Elkem acquired the competence required to take the next step. The company was ready to investigate practical, operational carbon capture solutions for its smelter plants. In parallel with CO2 Hub Nord, the company executed a feasibility study, which was completed in 2021.
The purpose of the study was to devise a business model for the installation of CCS technology at Elkem’s smelter plants. The model evaluates all critical factors related to operating such technology. By closely considering a diverse set of operating conditions – such as technical status – at the smelter plants, the model calculates with a high level of precision, what it will cost to implement capture installations at the local plants.
Two solvent technologies – from Saipem and Aker Carbon Capture – were evaluated according to the needs of the smelter plants. How could the technologies be adapted to the operational environments? How well suited were they to extract CO2 from the flue gas emitted during the production process?
«It was an incredibly exiting exercise,» says Ragnhild Jensen, project director in Elkem. «We needed to learn more about the practical aspects of CCS. What do we have to do on our side of the interface? How must the plants prepare and facilitate the installation of the new technology? What happens in the capture process? What’s the output? And – not least – what is required in terms of energy integration?»
Elkem brought in Norsk Energy, a consultancy specializing in environmentally friendly and safe use of energy, in order to evaluate the energy integration aspects of the technology from the two suppliers.
«The project gave us a better understanding of the efficiency of capture, the technical requirements that the vendors specified for Elkem’s flue gas, and the output of the technologies,» says Ragnhild Jensen.
The result was a significantly improved process design for the implementation of CCS technology.
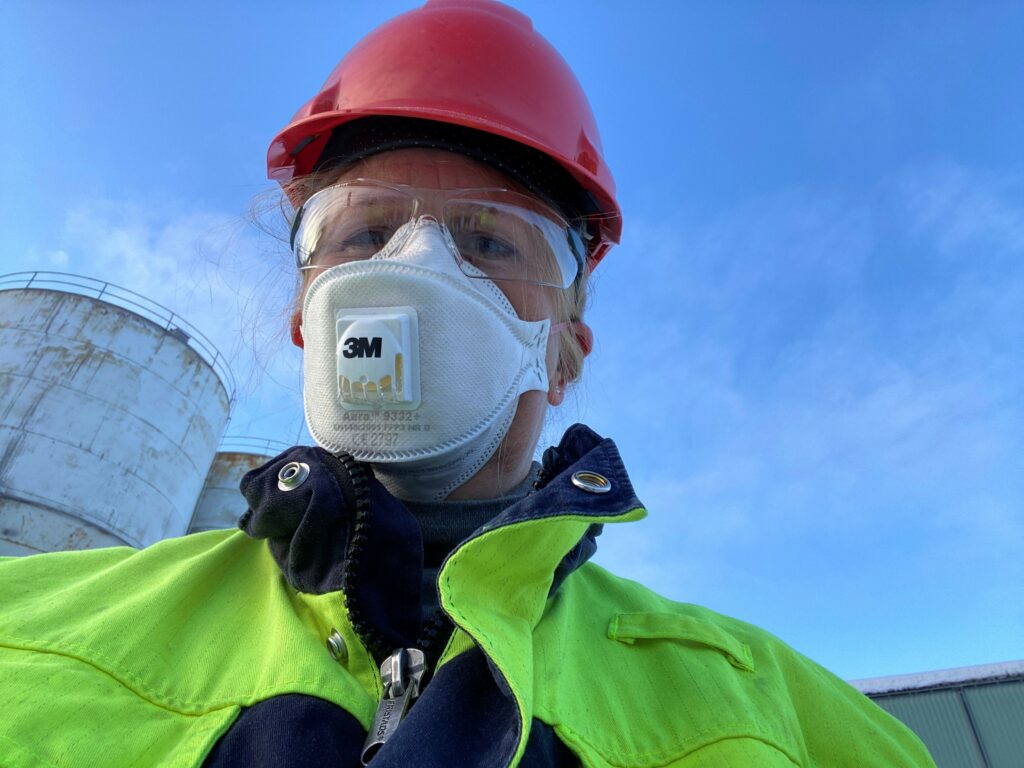
One step further
The knowhow that Elkem acquired through meticulous preparations, has been essential in order to carry out comprehensive testing at the smelter plants.
«The natural next step for us, is to verify the technology at our plants,» says Trond Sæterstad, Elkem’s climate director. «Before we can make an investment decision, the capture installations must be tested and evaluated in an operational setting.»
Now, the ferrosilicon producer Elkem is starting up – under the auspices of the CCUS industrial consortium CO2 Hub Nord – the first pilot project of its kind. During six months, the company will operate a mobile test unit from Aker Carbon Capture – a full-scale capture plant in miniature.
The capture technology from Aker Carbon Capture will be tested on separate flue gases from Elkem Rana and SMA Mineral. However, the project will also test CO2-cleaning from jointly sourced flue gas from the two producers.
The last alternative opens up for exciting prospects. The option of gathering streams of flue gas from several producers, will translate into significant cost reduction for each industrial company.
And this is critical. Because it’s imperative to reduce costs.
CO2-hub participants. Rana-MTU building site.
CCS creates new industries
Hydrogen Mem-Tech recently received NOK 170 million in new capital from major Norwegian and international stakeholders.
But for the Trondheim-based business – a leader in hydrogen technology – it has been a determined route to this milestone.
Investors
On 9 May 2022, it was announced that heavy-weight investors – AP Ventures, Yara Growth Ventures, Shell Ventures, Saudi Aramco Energy Ventures and SINTEF Venture – had chosen to provide significant backing to Hydrogen Mem-Tech. It involves investors with considerable experience and expertise in the hydrogen value chain, and who have high hopes for the hydrogen economy.
Hydrogen Mem-Tech has worked on further developing a technology involving palladium membranes to filter out hydrogen from natural gas and biogas. CO2 and waste gasses are captured during the process and can then be stored or deposited.
The technology is hitting a market that is seeing strong growth. Hydrogen is viewed as a driver of the green transition.
“Interest in hydrogen has accelerated rapidly in recent years and has opened up lots of markets – far beyond those we might have envisaged as the primary ones when we started out,” says Thomas Reinertsen, CEO of Hydrogen Mem-Tech.
Opportunities in a number of areas are being looked into around replacing other types of fuel with hydrogen, such as for cars, boats, energy generation – and in the processing industry, concepts to replace carbon as a reducing agent with hydrogen are being considered.
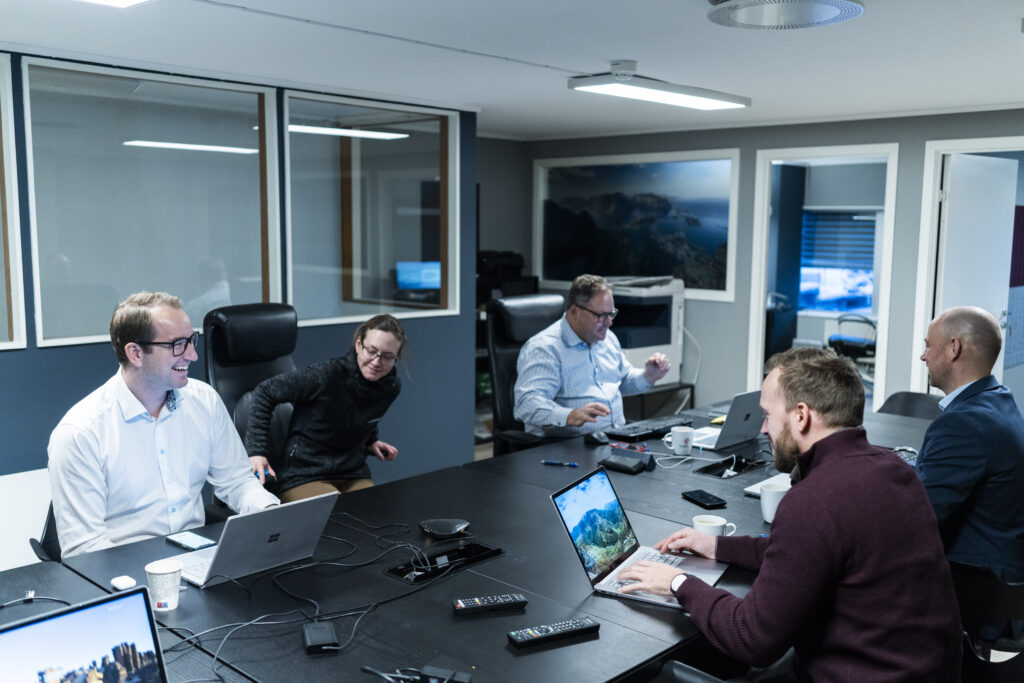
The journey to investor interest
Close contact between Hydrogen Mem-Tech and SINTEF created a breeding ground for a business idea. The starting point was looking at alternatives for carbon capture that can contribute to the green transition. SINTEF had developed a competitive and promising Palladium membrane at the laboratory scale which can filter out hydrogen from natural gas, but the research institute was looking for an industrial partner who could further develop and commercialise this technology. Hydrogen Mem-Tech – which drew on extensive experience from the oil and gas industry – was keen on the idea.
And Hydrogen Mem-Tech chose to throw itself in at the deep end. In just a short period of time, they developed the technology from lab-scale to a pilot facility.
“We decided early on to set up a pilot of this technology in an operational environment. And we were given a unique opportunity to build a pilot facility on the grounds of Equinor’s facility at Tjeldbergodden,” explains Reinertsen.
Membrane technology is a good example of successful co-operation between a leading research community and an industrial operator with knowledge about running a processing facility – and how to integrate technology into existing infrastructure.
“There are advantages and disadvantages to testing at large scale early on in the process. But trying it out in the real world early on was clearly crucial for the development of the technology as it stands today,” Reinertsen continues.
Technology in the operational environment
Hydrogen Mem-Tech has focused primarily on making the technology resilient. Our palladium membrane is much thinner than other membranes. It is therefore crucial to create a membrane and a set-up that can handle unforeseen circumstances, such as, for example, power outages and rapid shutdowns. Furthermore, the technology can be installed in both small and large facilities and has low operating costs.
“Our focus on making it more robust has proven to be worth its weight in gold. It means that we have already been able to deliver reliable products while the company is still in its early stages,” says Reinertsen.
Vital support from CLIMIT
Funds from CLIMIT have played an important role in the development of the technology and the company.
“The support we received from CLIMIT back in 2012-2014 turned out to be the ticket to being able to build a technology and a company in exclusively Norwegian hands up to today. It would have been impossible to achieve this without public support from CLIMIT.
It probably wouldn’t have been possible to attract enough private capital to develop this kind of tech company in a long-term perspective. The support we are now seeing from international stakeholders represents a great springboard for Norwegian technology in the wider world.”
Carbon-free power generation – from idea to solution
Industrial gas turbines are used in power plants and as mechanical drives. Today’s industrial gas turbines use fossil fuels such as natural gas or diesel, which causes CO2 emissions in the exhaust gas.
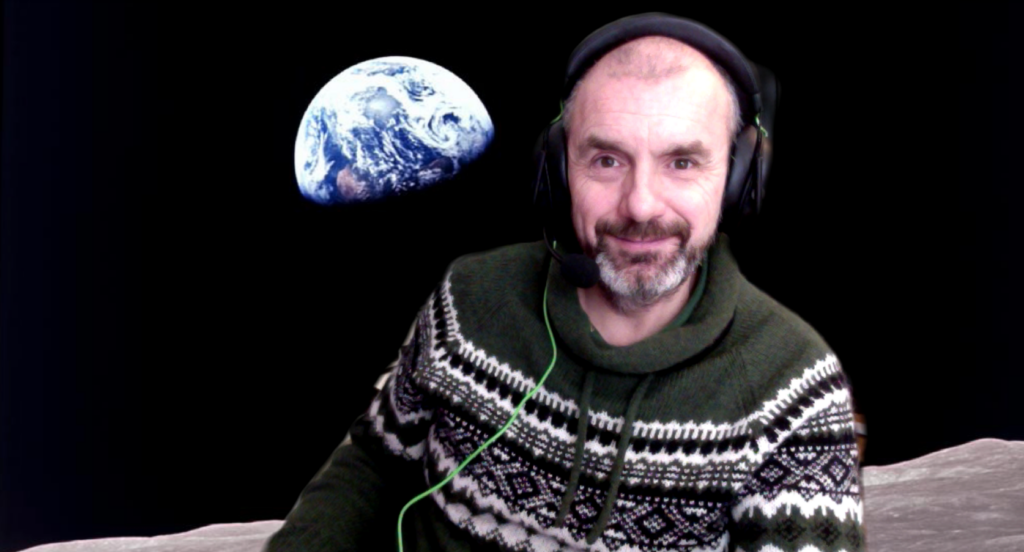
The BIGH2 project develops gas turbines that can use carbon-free fuels that eliminate CO2 emissions. The aim of the project is to develop solutions that enable gas turbines to perform as well with carbon-free fuels as with today’s fossil fuels.
Gas power plants have higher efficiency and significantly lower CO2 emissions than coal-fired power plants, but emissions from gas power plants must nevertheless be reduced to meet climate targets.
“A fundamental idea for BIGH2 has therefore been to facilitate the transition to low carbon fuels”, says project manager Andrea Gruber at SINTEF.
Carbon fuel
Hydrogen is a promising alternative to fossil fuels because combustion of hydrogen gives water vapor (H2O) instead of CO2 as a product in the exhaust gas, but there are also challenges with the use of hydrogen as a fuel:
Hydrogen has low density, so it must be transported under high pressure, or in liquid form at very low temperature.
Higher safety risk because the hydrogen is very explosive (wide flammability range and low ignition temperature).
Combustion of hydrogen results in high flame temperatures that can result in emissions of nitrogen oxides (NOx) that exceed statutory emission limits. NOx is a local pollution that can cause people respiratory problems and cause acid rain.
Controlling combustion is more challenging for hydrogen than for hydrocarbons, and combined with high flame temperatures, it increases the risk of emergency shutdowns and damage to the turbines.
The challenges of hydrogen led the project to choose to study the use of ammonia (NH3) as fuel. Ammonia is produced in large quantities all over the world, including as a raw material for the production of fertilizers, so there is already a well-developed infrastructure for transporting ammonia.
Phase 3 of the BIGH2 project studied the combustion of hydrogen and ammonia in models of combustion chambers of an industrial gas turbine from Siemens. The combustion chamber is the part of a gas turbine where the flame stands.
Ammonia has inferior combustion properties compared to fossil fuels, and must be mixed with more reactive substances to achieve a stable flame. Splitting a share of ammonia fuel into hydrogen and nitrogen results in improved combustion properties of the fuel mixture. Since this splitting is an energy-intensive process, the project has focused on identifying the energy-optimal mixing ratio of ammonia, hydrogen and nitrogen.
“In our process, we use the waste heat from the gas turbine to split ammonia to increase the reactivity of the fuel and at the same time we achieve an increase in the efficiency of the plant. This solution may reduce the costs of different CCS chains”, says Andrea Gruber.
Reduced NOx emissions
One challenge is that the combustion of ammonia-enriched fuels, if not done correctly, can also result in significant emissions of NOX and potent greenhouse gases such as nitrous oxide (N2O). By organizing the combustion at different stages of the combustion chamber, the project has managed to reduce the formation of NOX and N2O to an acceptable level.
Andrea Gruber and his research team worked long office hours before experimental work was carried out in the laboratory. Many small-scale combustion experiments were carried out in SINTEF’s pressurized combustion rig at Gløshaugen to test the flame stability of the various fuel mixtures, and to measure the emissions of NOx. Measurement data from the experiments were then used in numerical simulation software to model flames of various compositions of ammonia, hydrogen and nitrogen. Data was exchanged with partners at NTNU in Trondheim and with Sandia National Laboratories in the USA.
“The most important result from the project is that we have now seen that it is possible to use ammonia as an energy carrier – no major obstacles have been found. BIGH2 has shown us how this can be done. We didn’t have that knowledge when the project started,” says Andrea Gruber.
Broad collaboration
SINTEF worked with NTNU, Siemens and Equinor as partners in the project, while Sandia National Laboratories (USA) and the University of California, San Diego were involved as external partners.
Future plans
“Future work will focus on the development and demonstration of a modified DLE (dry low emission) burner and combustion chamber. We now know that this can be done but we must find the optimal way to implement the solution in a gas turbine. The main goal is to achieve fuel flexibility, i.e. to create a gas turbine that can seamlessly transition between natural gas firing and the application of an optimized ammonia-based fuel, in a realistic burner design,” says Andrea Gruber.
Scientific publications
- Chemical kinetics of hydrogen/ammonia flames:
- Spatial patter of NOx formation in hydrogen/ammonia flames:
- Blow-out limits of hydrogen/ammonia vs methane turbulent flames:
- Pressure scaling of flame propagation in hydrogen-enriched flames:
- Experimental demonstration of rich-lean staging of hydrogen/ammonia combustion in a gas turbine burner:
Science publication; Electrochemical production of hydrogen from natural gas
Proton-conducting membranes enables use of electricity as process energy to produce hydrogen from natural gas with low energy loss and simplified CO2 capture.
Hydrogen from natural gas
The journal Science has published “Single-step hydrogen production from NH3 , CH4 , and biogas in stacked proton ceramic reactors” authored by researchers from CoorsTek Membrane Sciences, University of Oslo, SINTEF and the research institute ITQ in Spain. CLIMIT-Demo has supported this research.
Traditional production of hydrogen from natural gas with CO2 capture takes place in several production stages with reforming, separation and compaction. Proton-conducting membranes gather these stages in one step with lower energy loss. This technology is also more suited for CO2 capture in connection with small-scale hydrogen production.
Like other electrochemical energy technologies such as batteries and fuel cells, the proton conducting reactors are made up of many small cells or membrane tubes. The new article shows how high energy efficiency from testing of single cells is maintained when cells are assembled in scalable units.
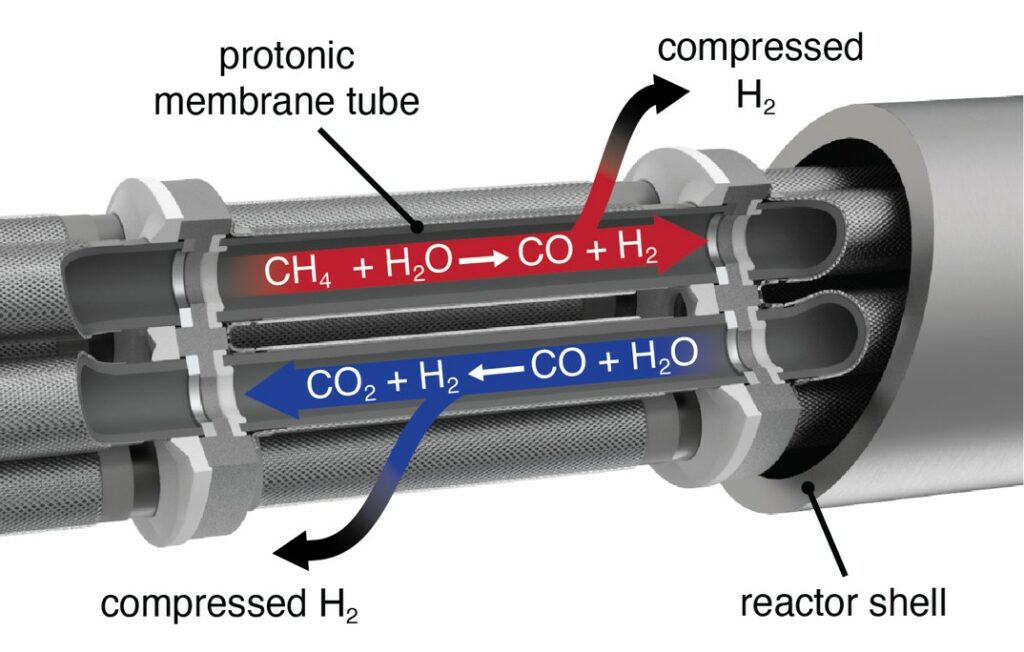
Two projects; Protonic
The development work in connection with the article is supported by CLIMIT-Demo through the project 618191 «Protonic». CLIMIT-Demo has also supported the next phase of the development work for project 620208 «Protonic Phase II».
Safe CO₂ storage using traceable noble gases
The University of Oslo has developed a new and effective method of monitoring CO2 storage sites by measuring the quantity of noble gases in CO2 streams.
When large amounts of CO2 need to be stored safely underground as a climate initiative, we need to be able to document that it stays where it is. It requires technology that measures carbon content along with the possibility for checking where carbon is coming from in a quick, affordable and accurate manner. The University of Oslo has researched a method that can provide an answer quickly and affordably. Noble gases are the key.
A new method of monitoring
During the ICO2P project, project manager Anja Sundal, PhD fellow Ulrich Weber and their team developed a method whereby analysis of noble gases and CO2 can be used to monitor CO2 capture and storage. The chemical and physical “fingerprint” of various isotopes and relative concentrations of gases can be used to identify CO2. Partners in Switzerland have created an instrument that can measure extremely low concentrations of noble gases. Researchers in ICO2P have used this instrument for the entirely new purpose of monitoring CO2.
“We have designed a mobile and cost-effective monitoring programme for CO2 capture operations and storage sites on the Norwegian continental shelf. The equipment fits in to a small, portable suitcase and can be easily transported to where we need to take measurements,” says Sundal.
During the ICO2P project, the University of Oslo worked with researchers from Eawag in Switzerland, who developed this device, a mass spectrometer, which is totally unique since it can measure extremely low concentrations of noble gases (He, Ne, Kr, Xe, Ar), as well as other environmentally relevant gases (O2, CH4, CO2 and N2) out in fields. This is a significant development as knowledge of gas compositions can provide a lot of environmentally relevant information right there and then. All origins of CO2, in the atmosphere, the ocean, produced by bacteria, or captured from industrial processes, have their own natural, unique imprint of noble gases.
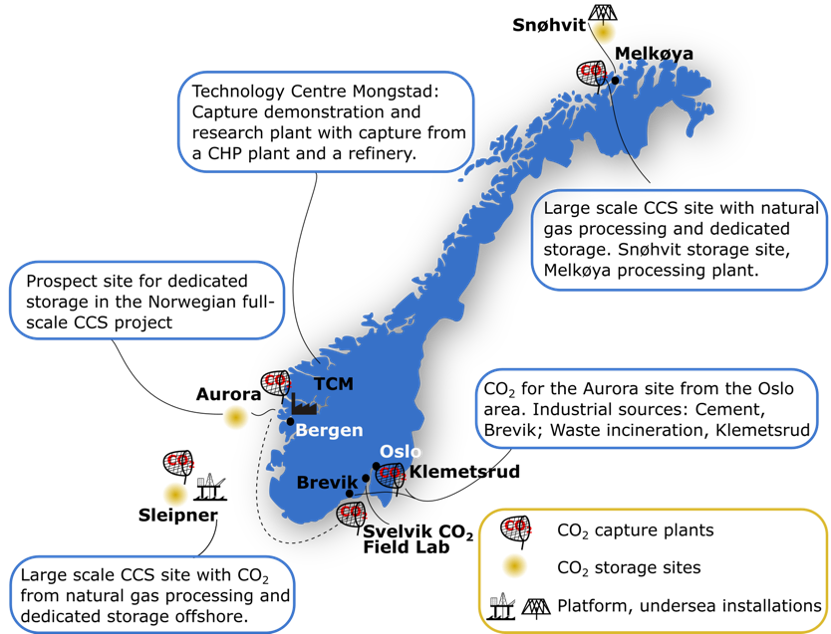
Samples gathered from natural gas fields
During the project, the ICO2P team gathered samples from Norwegian natural gas fields, CO2 capture plants and at CO2 storage sites in order to gain understanding about the geochemistry and isotope signatures of gases needing to be stored, and to find out if it is possible to identify them later and distinguish them from other gas sources.
“We have monitored noble gas variation in different carbon capture operations using this instrument and adapted calibration methods,” Sundal explains.
Measurements were carried out at the Technology Centre Mongstad (TCM), at Melkøya (Snøhvit) and at the Klemsterud waste incineration plant. This has not previously been surveyed and provides new scientific insight into the processes that causes stored gas to have a unique signature. Noble gas concentrations in “captured” CO2 appear to be much lower than in the atmosphere, while there are significant differences in concentrations and signatures between various capture operations. Time variations have also been documented in the gases’ signatures, something which offers insight into capture processes.
Knowledge about gases’ chemical and physical “fingerprint” can later be used to identify the source. This is vitally important for being able to monitor the CO2 if it should flow out of a storage site, because you need to be able to distinguish between anthropogenic and natural gases that seep out from the seabed.
Noble gas signatures
PhD fellow Ulrich Weber has utilised knowledge about noble gas signatures in captured and anthropogenic CO2 to model how signatures change when injected CO2 comes into contact with fluids (fossil saltwater) in geological reservoirs. Calculations show that with time, the injected gas will change its signature, since it will absorb more noble gases from the reservoir. The signature will nevertheless be recognisable and distinguishable from both atmospheric gas, fossil natural gas, gas produced by bacteria and gas hydrates.
There has been excellent collaboration between academia and industry. Industrial partners have contributed as supervisors, made significant contributions to publications, made data available for the project, and contributed with finances to the project.
The results from the project are useful for industry. The project presents a measurement system that fits in to a small suitcase. This means both researchers and industrial operators can take it with them to where they need to make CO2 and noble gas measurements to verify safe gas storage. A simple, affordable and practical solution.
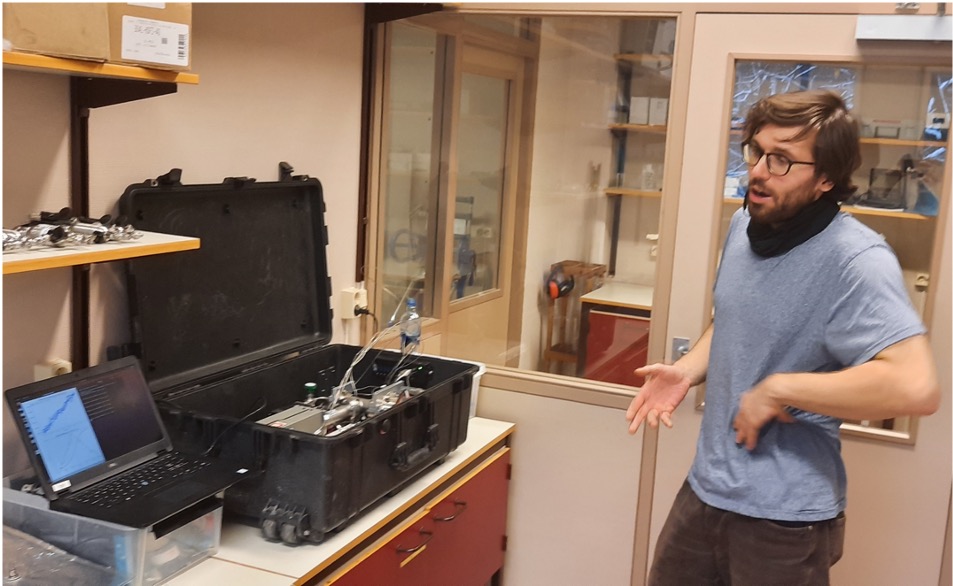
Key data about the project
Title: ICO2P – Application of noble gas signatures in monitoring schemes for offshore CO2 storage
Project number: 280551
Partners: University of Oslo (project owner), Equinor, Shell, Eawag
Project period: 2018–2021
Budget: NOK 9.2 million, including NOK 5.5 million in funding from CLIMIT
Meeting goals through international cooperation
For the last five years, CLIMIT has built up a strong portfolio of international projects through ACT, Accelerating CCS Technologies. This has led to research that delivers the results needed to construct fullscale CCS facilities.
ACT is a network of 16 countries and regions which work together on calls for project proposals and knowledge sharing. The Research Council of Norway is the coordinator of ACT and Gassnova is also a Norwegian partner.
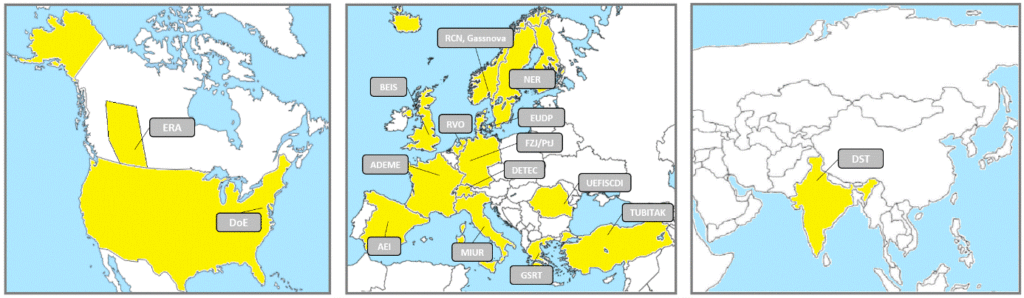
Achieved good results
ACT was established in 2016 after which it signed a five-year contract with the European Commission. The expiry of the contract at the end of 2021 marked an important milestone for ACT. Strong results were achieved, and new opportunities are being explored to continue ACT.
ACT stands for Accelerating CCS Technologies, and its aim is in the name – accelerate the development of CCS technologies. The collaboration began as an ERA-NET Cofund. This was an instrument of the EU’s Horizon Europe programme for research and innovation, where the European Commission would provide top-up financing for European countries collaborating on international joint calls for research and development on key topics. Many ERA-NET Cofunds were established across a broad range of topics, but ACT was the only ERA-NET Cofund relating to CCS.
33 research and innovation projects
Over the period 2016-2021, ACT carried out three calls for proposals giving R&D organisations and industry the opportunity to apply for funding for new CCS-related projects. These have resulted in 33 research and innovation projects with a total budget of NOK 1.4 billion, with ACT providing close to NOK 1 billion of that (close to € 1 M).
The projects supported by the first ACT call are now complete, while projects from the second call are now into their final year. 13 projects from the third ACT call are in their start-up phase. You can find details about the projects on the ACT website.
Norway has been a key pioneer of ACT, and Norwegian partners are involved in 23 of 33 projects. Financial support from ACT for Norwegian partners totals around NOK 230 million, with NOK 200 million coming from CLIMIT and roughly NOK 30 million coming from the European Commission. In other words, CLIMIT has been a key and major investor in ACT, and ACT projects account for around a fifth of CLIMITs total portfolio.
Solid results
ACT can boast five years of solid results. Importantly, ACT-supported projects have led to significant technology development in line with CLIMIT’s programme plan. New knowledge and expertise have been uncovered through ACT, and we have seen new and promising innovations in carbon capture, transport and storage. That said, the results and impacts of ACT go far beyond technological innovations:
- Thanks to ACT, many countries helped in financing the projects. Sharing costs like this means that each country gains more knowledge and expertise for each penny invested than would have been possible through national calls for proposals alone.
- ACT has helped coordinate research priorities across national borders.
- Thanks to ACT, many countries have invested much more in CCS research and innovation than they would have without ACT.
- ACT projects have proved attractive for industrial partners, helping mobilise industry.
- ACT projects have engaged in knowledge sharing activities that have given decision makers and industrial operators increased understanding of CCS.
- Both the ACT projects and the policy agencies behind ACT have facilitated fantastic knowledge sharing across national borders.
Just before Christmas, ACT presented their final report to the European Commission.
Many ACT projects have delivered results needed to construct large-scale CCS facilities. We have provided some examples below:
- The Pre-ACT project, coordinated by SINTEF, has examined how pressure build-up can be managed while storing CO2. This has led to new knowledge important for partners in the Northern Lights project.
- ELEGANCY, also coordinated by SINTEF, has examined how hydrogen value chains combined with CCS can be established. The results are vital now that hydrogen is an important priority for Norway and other countries.
- Many ongoing projects are examining monitoring technologies for CO2 storage sites. Large-scale storage sites will require accurate and cost-effective technologies that document how CO2 flows, so that we can ensure it is being stored safely. The projects DigiMon (coordinated by NORCE), SENSE (coordinated by NGI) and ACTOM (coordinated by the University of Bergen) are examining different monitoring technologies for storage sites.
- The NEWEST-CCUS project is researching new solutions for CO2 capture at waste management facilities. SINTEF and many Norwegian industrial operators from the waste management industry are involved in the project.
- The AC2OCEM project is developing new technology for CO2 capture at cement factories. SINTEF and NTNU are Norwegian partners. Many large industrial companies are involved in the project.
- A newly started project, RETURN, coordinated by SINTEF, will examine how empty oil and gas fields can be re-used for CO2
- Another new project, CEMENTEGRITY, coordinated by IFE, will research how cement can be used in CO2
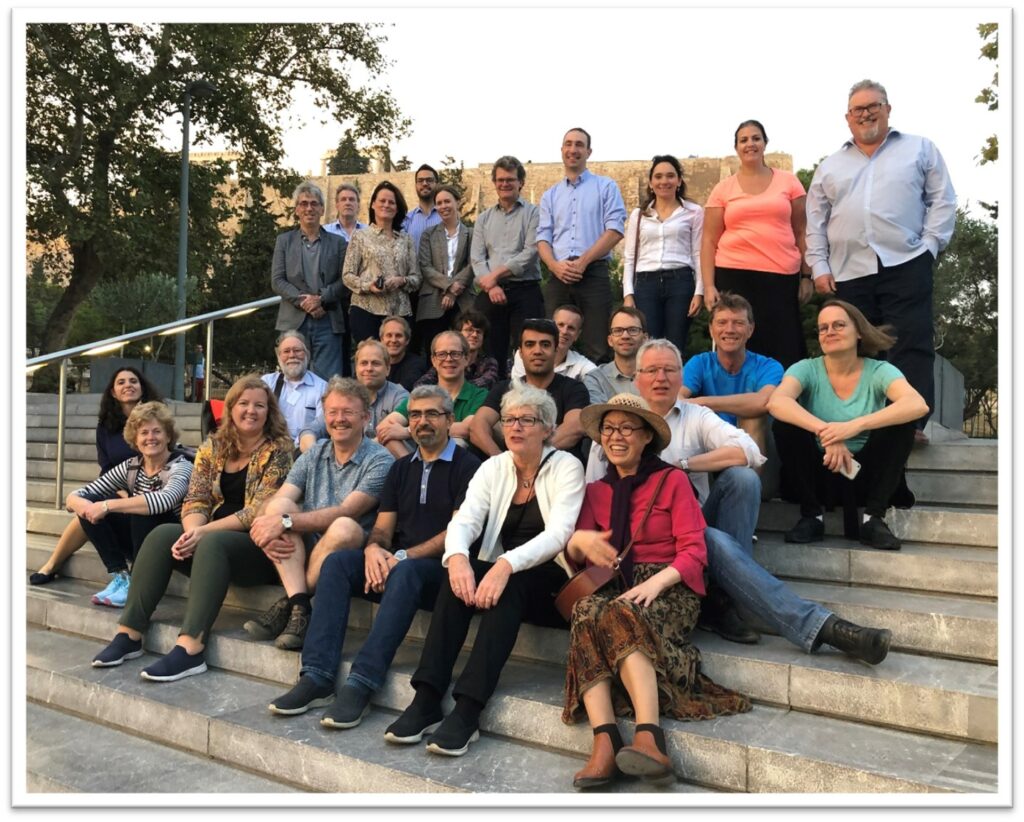
All policy agencies involved in ACT are prepared to continue working together. One aim is to continue ACT through the EU’s new Clean Energy Transition Partnership (CETP), which is in its early phase as of spring 2022. Some countries involved in ACT are also planning an ACT4 call for proposals. This proposal will be available on the ACT website in April or May 2022.
Towards a new CO₂ deposit on the NCS
The SWAP and SWAP 2 projects confirmed that the CO2 storage capacity in the Smeaheia area is as significant as expected. Now Industry and researchers can present data that uphold previous estimates with higher confidence.
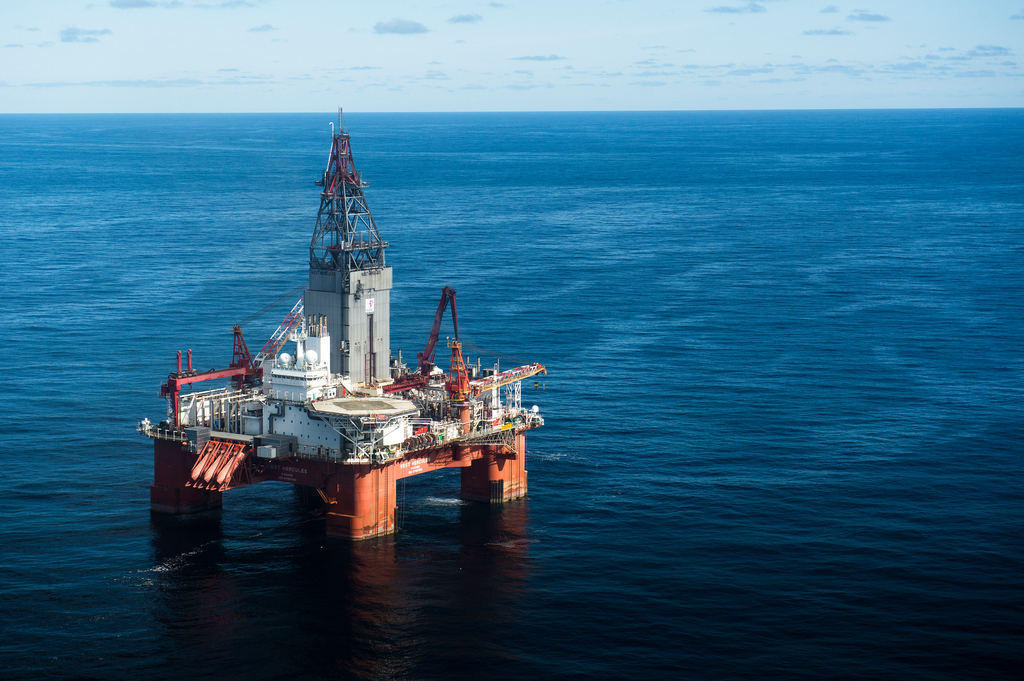
In the spring of 2018, Equinor was awarded a licence to drill an exploration well in the southern part of the Smeaheia area. The subsequent drilling on the Gladsheim structure during 2019, represented a rare opportunity to collect subsurface data, paving the way for a future CO2 repository. SWAP (Strategic Well Acquisition Project), supported financially by CLIMIT, was established in 2019 in order to gather data that operators usually do not collect when drilling exploration wells.
«The idea was that even if the well turned out to be dry, it would still be important to extract extensive data from the subsurface, since the area is a prospective CO2 storage location, explains Equinor’s Rune Thorsen, project manager for SWAP.
Comprehensive scope
A large part of the extra collection consisted of data from the cap rock. The data confirmed that the cap rock is strong and will remain impermeable if CO2 should be injected into the reservoir. Core samples were taken and rock-mechanical tests executed in order to find the quality and strength of the cap rock. Equinor also measured the porosity, permeability and fracture pressure of the rock in a thick shale, the Draupne formation. Usually, these types of samples of the cap rock are not taken in an exploration well.
In addition, a set of pressure measurements were conducted in the different reservoirs, in order to measure the degree of communication with the Troll field.
And the analyses yielded positive results
«It was confirmed that the reservoirs are well suited for CO2 sequestration. There is ample communication with the Troll field, and core samples extracted in the Gladsheim well confirms that the strength of the cap rock is good. This means that we can inject very large volumes of CO2,» says Thorsen.
In the SWAP 2 project, extra data was captured from another exploration drilling, this time at Stovegolvet, in the southern part of the Horda platform.
«When we exploration drill on the Horda platform around Troll, the chances of finding commercial quantities of hydrocarbons typically lie between 20–30 percent. But our long experience and understanding of the area tell us that the geology can safely retain CO2. If we collect comprehensive amounts of data during exploration drilling, we can avoid injecting only small volumes of CO2 initiallybefore ramping up volumes after several years of injection experience. Retrieving data during exploration drilling enables us to scale up volumes faster,» explains Thorsen.
A step closer to realization
And these are exciting times for the CCS community. In June 2021, Equinor nominated Smeaheia for licensing by the Norwegian Ministry of Petroleum and Energy. In September, the licensing round for the next significant areas for CO2 storage on the Norwegian Continental Shelf, was opened. And Equinor was one of the five companies that submitted bids.
«At Smeaheia, we have proposed developing a storage solution for 20 million tonnes of CO2 per year. This represents a formidable and necessary increase in global CO2 injection capacity and should be regarded as an explicit benefits realisation of the pioneering Norwegian Longship project » says Thorsen.
Equinor has ambitious plans to stay ahead as one of the global leaders in the field of CCS.
«We hope that we will be awarded the licence on Smeaheia, and that the second well at Stovegolvet can open up for further CO2 storage licenses in the area. I believe that the entire Horda platform – which includes the current Northern Lights licence, Stovegolvet, Smeaheia and the surrounding region – has the potential to become a huge central deposit area for CO2 on the NCS.»
Financial support from CLIMIT represented an important contribution to the project
«CLIMIT awarded financial support that made it possible to execute SWAP and SWAP 2. Without this support and results from drilling, CO2 sequestration on Smeaheia would probably have been delayed by several years,» says Rune Thorsen.
Partners in SWAP were Equinor and licence partners in PL921: Lundin Norge, Petoro and DNO Norge AS. Partners in SWAP2 were Equinor and license partner in PL785S, TotalEnergies.
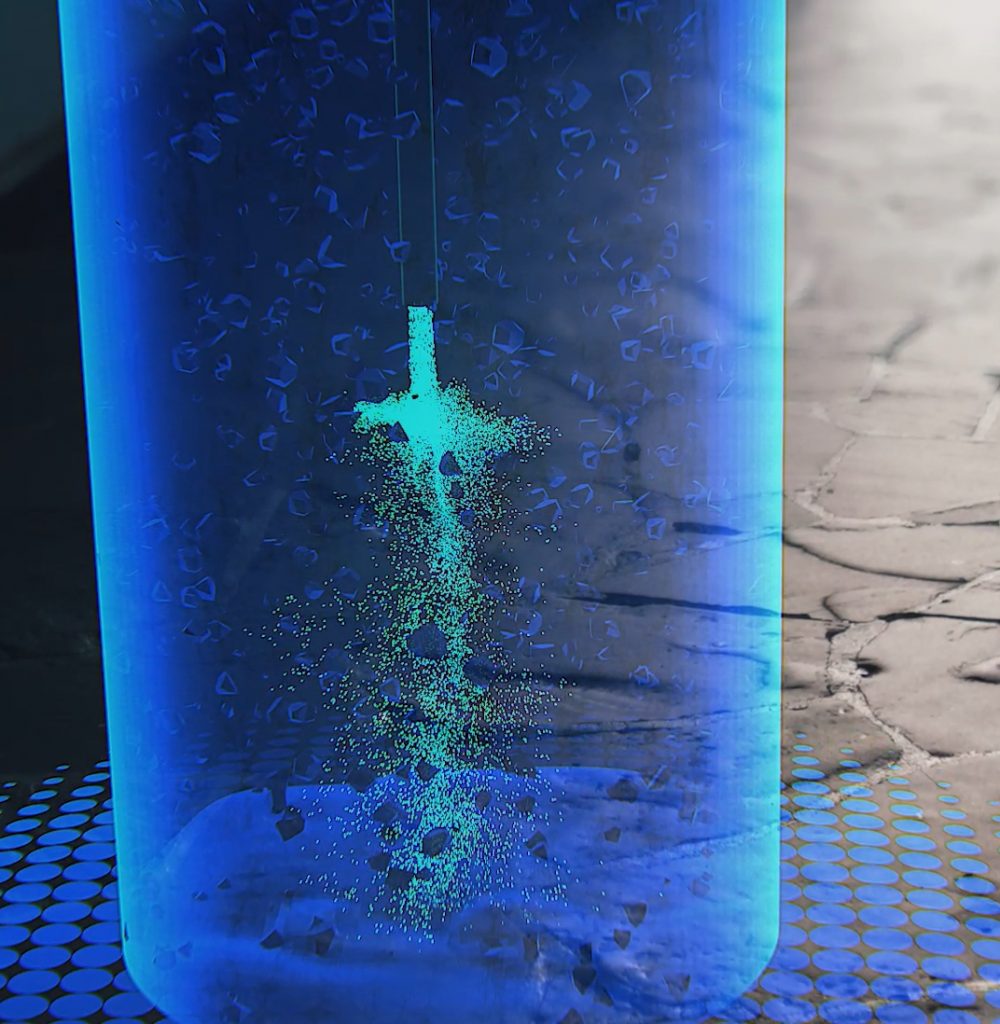