- For those interested in more details about the project itself
Capture of CO₂ in a new dimension
It is not often within the CLIMIT Demo program that we can announce completion of a new doctoral degree. Ron Jacob has contributed significantly to the ELSE project (Electrified Cement Industry), and the results derived from his work hold relevance for the cement industry.
With Cement in His Blood
Professor Lars-André Tokheim, who has served as Ron’s supervisor, has been involved with the cement industry since 1994. He initially worked as a research fellow until 1998, followed by a period as a process engineer and head of the process department at Norcem until 2006. He is currently affiliated with the University of Southeast Norway (USN) and maintains a close collaboration with the cement producer, located only 10 km from the campus.
“When the opportunity arose to secure project funding from CLIMIT for 3.5 years, it was a perfect chance to bring a doctoral student into the project,” Tokheim remarks. “Having such a dedicated resource available, someone who could fully commit his time to the project, proved immensely valuable. Ron brought exceptional expertise to our team, elevating the project significantly,” he insists. “He is the most brilliant PhD candidate I have mentored. Ron has demonstrated mastery in everything from laboratory work, technical problem solving, process design, modeling, and simulation to the actual writing process,” concludes the proud professor.
This is also of grate value to the industry, as they now have access to new findings that can potentially reduce the costs associated with CO2 capture.
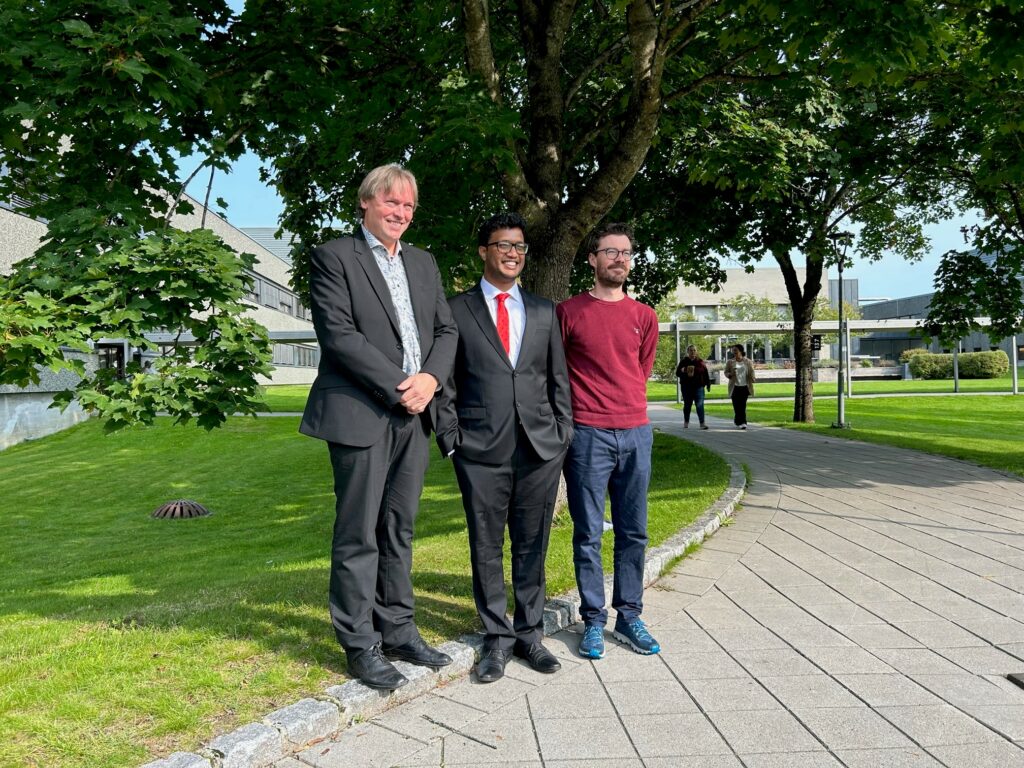
Ron Mangalam Jacob
Originally from: India
Master’s Degree: Process Technology at USN in 2017
PhD Degree: August 2023 “CO2 Capture through Electrified Calcination in Cement Clinker Production”
Employment: Commencing at Hydro, Herøya. His doctorate will prove beneficial in his new role.
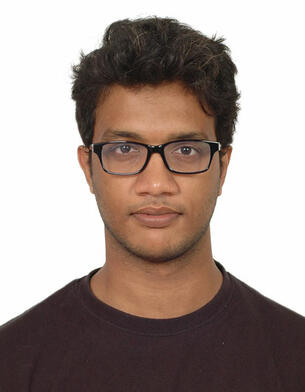
Capable of Capturing More than 78% CO2
Ron’s project revolves around the electrification of the calciner plant, which constitutes the primary source of CO2 emissions within a cement kiln. By electrifying the calciner, CO2 emissions from today’s combustion is eliminated, resulting in nearly pure CO2 emitted from the kiln. Consequently, this allows for CO2 utilization directly or CO2 transported for storage, without the need for a separate capture facility.
Most of the calcination process occurs in the calciner, and the primary objective of the project was to determine an appropriate design for the electrified reactor. The results demonstrate that the utilization of an electrified calciner instead of a fuel-fired reactor can reduce CO2 emissions by approximately 78%, provided a renewable power source is available. This represents a significant opportunity for all cement industries, potentially allowing for a substantial reduction in the area required for CO2 capture.
“Norcem in Brevik is currently constructing a capture plant based on absorption, which is expected to capture approximately 50% of the CO2 present in the flue gas. We believe that, in the long term, it may be feasible to combine absorption with electrification of the calciner, allowing for the capture of nearly all the CO2 emissions from the cement plant in Brevik. Therefore, this process holds a tremendous potential,” remarks Tokheim.
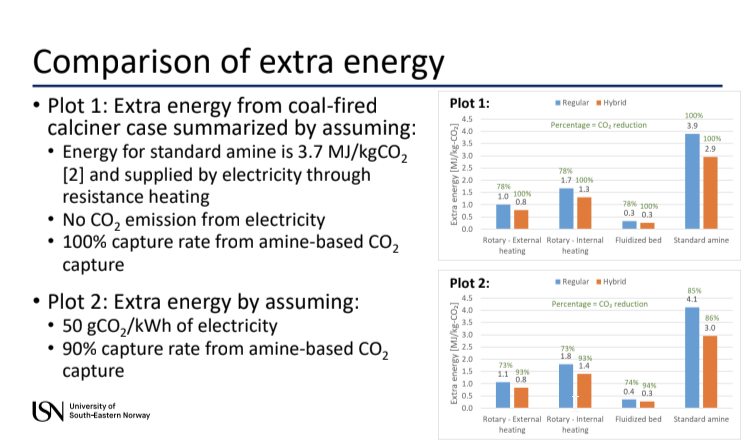
This would not have been possible without the funding from CLIMIT
Christoffer Moen, the project manager in Heidelberg Materials, emphasizes that this project could not have been executed in Norway without the funding provided by CLIMIT. “This project holds significant importance for us, as it is directly linked to our industrial processes – it is a real-world case. The project has laid a solid foundation for Heidelberg Materials’ ongoing assessments regarding the technological development of our own factories,” Moen asserts.
Electrification of Cement Production (ELSE)
A distinct production model has been developed for the cement clinker, which has been validated against full-scale experimental results. Moreover, studies have been conducted on two different electrified rotary calciners, one featuring internal heating and the other external heating, through both experimental methods and mathematical modelling. The internally heated rotary calciner represents a novel concept developed during this research.
“In my work, it was concluded that a fluidization reactor is best suited for electrification, as it demands less energy than rotary calciners,” states Ron. “For potential future endeavors, we propose the construction of an electrified fluidization reactor to conduct high-temperature experiments and validate the promising results obtained in this doctoral work.”
“Calciner designs”, Slide from the defense. “Electricity to heat – concept”, slide from the defense.
“We are looking forward to the exciting results from the ELSE project and are eager to see how it will progress further,” says Jørild Svalestuen, case manager at CLIMIT.
Literature index
https://drive.google.com/file/d/1vZtXq80QAIKu9Gm1CxxcT6WluGdcEbM_/view?usp=sharing
HNET: “Live” monitoring of CO₂ storage under the seabed
The HNET project develops a unique method based on knowledge and technology that already exists.
Measuring seismicity in real time is one of the few monitoring methods that can continuously provide a picture of how the stress in and around the storage site may change, and thus can say something about the risk of leakage
What is HNET?
HNET is a CLIMIT supported research and technology development project aimed at developing and demonstrating a baseline seismic monitoring network for offshore CO2 storage in the Horda platform region of the Norwegian North Sea.
The project is focused on improved assessment of natural seismicity in support of planned CO2 storage projects on the Horda Platform region. t is focused on understanding natural background seismicity before starting the actual injection.
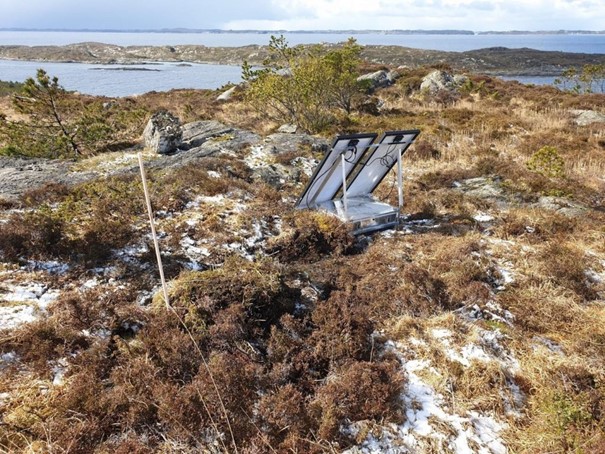
Establishing knowledge of background seismicity
The HNET project is led by Equinor, with partners NORSAR, Shell, TotalEnergies, Northern Lights JV, University of Bergen, Norwegian National Seismic Network (NNSN) and CGG. The project is divided into five phases, with decision gates between the phases (see fact box).
Own onshore seismic array
In the current phase, routine operation of the HNAR onshore seismic array (on land at Holsnøy) will be established. The data from HNAR will be integrated with available data from offshore probabilistic roadmap (PRM) nodes from Grane, Oseberg and Snorre.
In the summer of 2021, seismometers were deployed on the seabed (in the Aurora prospect, i.e., the storage location for the Northern Lights project). They were deployed for a year. The data from these nodes was recorded continuously and then incorporated with other recordings from offshore PRM nodes and onshore arrays.
An important part of this project is seismic risk assessment, data integration and information. This should be made available quickly and in an expedient manner, adapted to others than just the subject experts.
– We are very pleased with the data from the onshore array, says Volker Oye (Research at NORSAR)
Phases in the HNET Project
Phase 1
(SNS-NET Project) was carried out in the period August 2018 to July 2019.
Phase 2
(HNET) took the concepts further with the implementation of the instrumentation on land and the use of PRM nodes on the seabed, and the initiation of data collection and reporting from November 2019 to December 2020.
Phase 3
HNET3 is the ongoing project that will form the basis for the understanding of all natural, tectonic seismic activity before CO2 is injected into the ground in the Northern Lights project.
Phase 4
The last phase, which includes continuous real-time monitoring of the injection process.
Phase 5
This phase is an information and reporting phase and runs parallel to Phase 3.
Ultrasound ensures that CO₂ wells stay tight
The company Equanostic has developed new technology based on ultrasound that can check that the cementation in CO2 wells is tight. This is an important innovation when CO2 is to be stored in large volumes.
Impermeable plug
In order to reach international climate targets, it will be necessary to store billions of tons of CO2 deep underground. Wells must be drilled so that CO2 can be injected into suitable reservoirs. A steel pipe is placed in the wells to prevent fluids from the surrounding formation from leaking out. It is completely dependent on the back of the steel pipe being filled with cement and creating an impermeable plug. If you cannot verify the cementing job, there will quickly be large expenses if you must drill a sidestep. Alternatively, if misinterpreted and the annulus is not sealed, the consequences can be enormous in terms of environmental damage and financial costs
Equanostic
The well cementation can be verified using ultrasound. The theory behind the verification is extremely complex and Equanostic has now developed new methods for processing measurement results from wells.
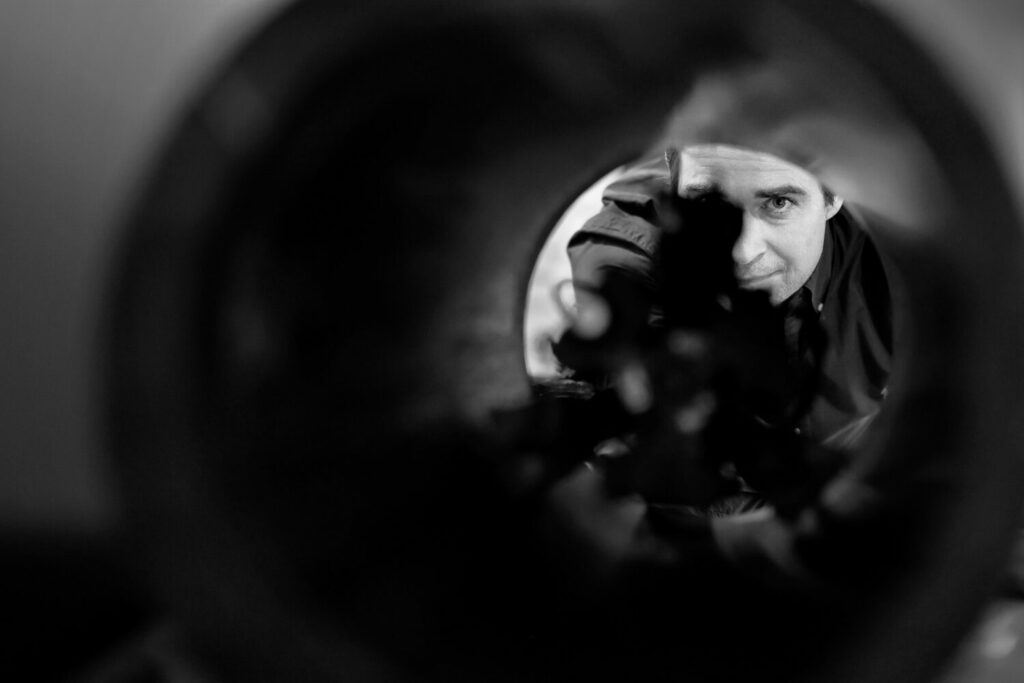
Positive results
The project goes by the name VRI and has been part-financed through the CLIMIT programme. Project manager Stig Støa from Equanostic is very satisfied with the results that have been achieved. Through the VRI project, a solution has been developed that provides far better verification than existing alternatives.
A separate framework
In the VRI project, new algorithms and new software have been developed for verification based on ultrasound. Through advanced machine learning algorithms, processing algorithms have been established that consider all relevant physical parameters in well operations. A separate framework has been built to handle the various formats in which field data is delivered, and field data from various wells in the North Sea and Barents Sea has been processed.
According to project manager Stig Støa, there is great industrial interest in the new software. Equanostic is now working on testing the product in collaboration with both Norwegian and European operators.

Key data for the project
Title: Ultrasound to verify that the cementation of the annulus
Project owner: Equanostic AS by project manager Stig Støa
Project partners: Equanostic AS and Aker BP ASA
Support from the CLIMIT programme: NOK 11.2 million.
Project period: 2020-2023
More details available from the Research Council’s project bank.
DigiMon – Digital Monitoring of CO₂ Storage projects
Affordable and flexible monitoring systems for CO2 storage are important for successful deployment of CCS value chains.
A key component of any CCS project is measurement, monitoring and verification (MMV), which must demonstrate that projects are planned and executed in a societally acceptable manner and that adequate technologies are implemented to ensure safety and security.
Multiple technologies at lower cost
A key scientific challenge is to deploy a cost-effective optimal combination of technologies that can collectively improve the probability of successfully verifying containment or detecting breaches in CO2 barriers. The overall objective of the DigiMon project was to “accelerate the implementation of CCS by developing and demonstrating an affordable, flexible, societally embedded and smart Digital Monitoring early-warning system”, for monitoring any CO2 storage reservoir and subsurface barrier system. The project included laboratory experimental studies and collection of field test data along with modelling and optimization. A strong focus on interdisciplinarity, between technical and social sciences, characterized the research.
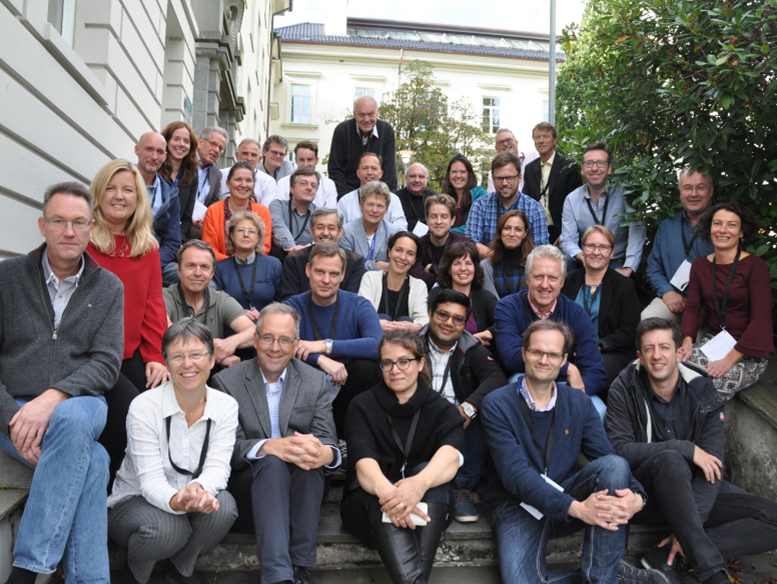
New knowledge with the help of DigiMon
DigiMon has contributed to improving individual system components and development of workflows for processing and interpretation of monitoring data, particularly a framework for inversion of multiple geophysical data. In addition, it has developed unique methodology for evaluating CCS technologies from the point of view of societal acceptability and benefit.
DigiMon was funded by ACT (Accelerating CCS Technologies) and hosted by NORCE. Other Norwegian partners included NTNU, MonViro, Equinor and Repsol. International partners counted CRES (Greece), Geotomographie and UFZ (Germany), Lawrence Livermore (US), Sedona (Romania), Silixa and Universities of Bristol and Oxford (UK) and TNO (The Netherlands). The project started in 2021 and was completed by end of 2022.
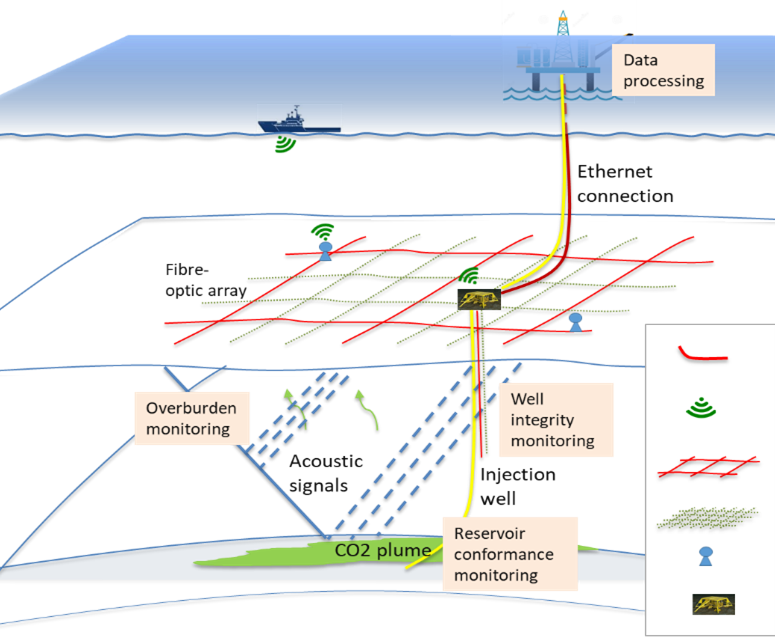
Sub-objectives for the DigiMon project included:
- Provide a system for monitoring the CO2 plume and identify and provide early-warning of actual or potential breaches in the subsurface barriers.
- Provide a flexible and interchangeable system with respect to the environment (offshore or onshore) and new system components provided by market-driven technology development.
- Provide a societally relevant monitoring system that addresses the views and worries of various stakeholder groups and citizens.
- Provide knowledge communication and dissemination to the public and policy makers.
Read more about the DigiMon project at CLIMIT-Demo.
Risk of corrosion “H₂S Challenges in CO₂ Pipelines”
The project (621269) awarded NOK 4.9 million in support in October 2021. Project owner DNV started up the project in March 2022 with partners Equinor, Shell, Gassco and TotalEnergies. IFE and Wood are involved as subcontractors.
In January 2023 the JIP was expanded to include ExxonMobil, Woodside, ArcelorMittal, Vallourec, Subsea7, Tenaris and Corinth as partners. The project is scheduled for completion in summer 2024.
How H2S affects the risk of corrosion
The project will investigate how hydrogen sulfide (H2S) as an impurity in CO2 streams affects the risk of stress corrosion and “normal” corrosion in transport systems. Project manager Klas Solberg, Senior Engineer at the Veritas Centre (DNV) in Høvik, has a PhD from NTNU, specialising in fatigue and fractures in pipeline systems. Solberg sums up the dilemma addressed by the project as such:
“Higher tolerance of impurities in the CO2 stream could make CCS achievable to more companies, but on the other hand, too much H2S in the CO2 stream could damage the pipeline system. Our project is trying to find the ideal balance.”
CO2 streams from capture plants will contain small amounts of impurities, such as H2O, NO2, SO2, H2S and O2. If the CO2 stream is liquefied, then a proportion of the impurities will be removed, but there will still be impurities at the “parts per million (ppm)” level in the CO2 stream.
Impurities can lead to corrosion and precipitation of solid reactive products in the transport system. Corrosion poses a risk to HSE, costs and the reputation of CCS. This risk can be reduced by cleaning the CO2 stream of impurities, and through the use of more corrosion-resistant materials and of greater safety margins (thicker and stronger materials in pipes and tanks). These measures will increase the cost of the transport system. More knowledge about the concentrations and combinations of impurities which can lead to corrosion will contribute to optimised designs of transport systems.
May result in changes to the CO2 specification
The Northern Lights (NL) project has set limits for impurities in a CO2 specification, but this does not mean that the NL specification is optimal for future CCS chains. New knowledge and new materials can lead to changes in the CO2 specification, providing better optimisation of risks and costs.
CO2 streams from refineries and steelworks, for example, may contain H2S. To avoid stress corrosion, current industry guidelines (standards and recommended practice) recommend that stress levels of steel exposed to H2S is kept well below the yieldstress. For pipelines operators allowing higher than recommended stress levels may reduce the cost of rock dumping for subsea pipelines.
The project will carry out experimental testing to map the relationship between H2S concentrations and stress corrosion and normal corrosion. The testing is being carried out by DNV, IFE and Wood.
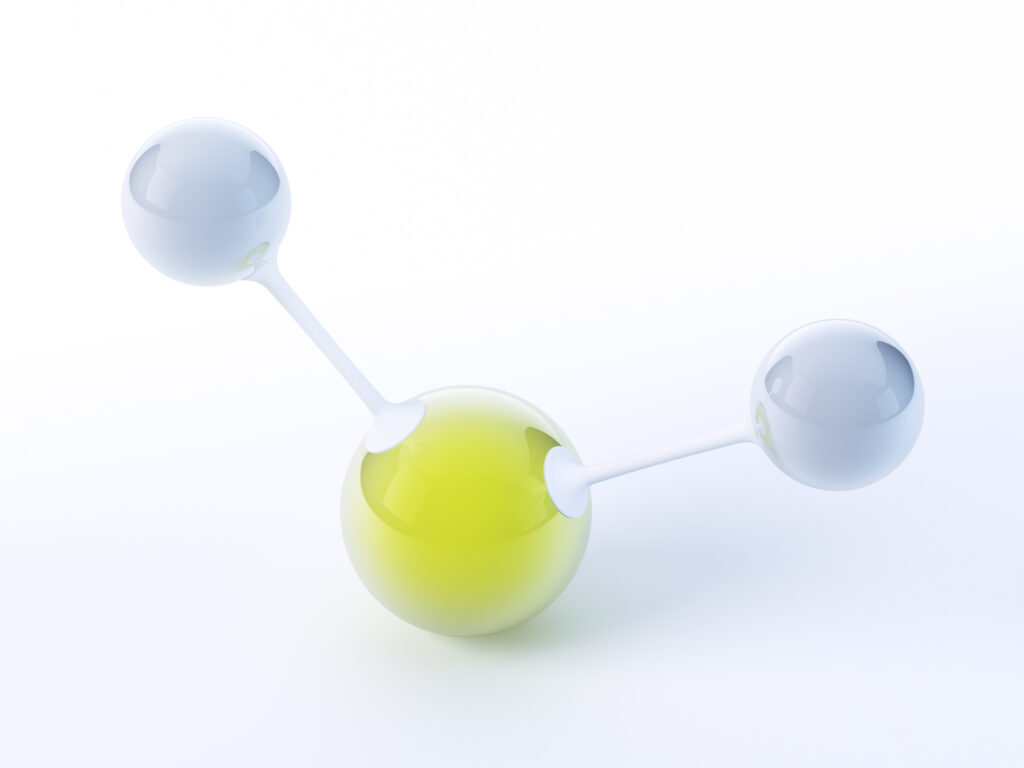
The project consists of four technical work packages
- Analysis of risks and challenges resulting from increased H2S concentrations. Investigate current concentrations of H2S from selected industries and processes.
- Define the risk of sulfide stress cracking (SSC) at relevant concentrations.
- Investigate how increased concentrations of H2S will affect the chemical environment in the transport system, and whether it might create a corrosive environment and affect the normal rate of corrosion.
- Assess solutions for removing H2S from the CO2 stream before it enters the transport system.
The results of the project will be used for two main deliveries
- Report on recommended H2S limit for the Northern Lights project, which may increase the H2S limit for future CO2 streams.
- Update DNV’s recommended practice document DNV-RP-F104 “Design and operation of carbon dioxide pipelines”. This will mean the results of the project will be available to actors beyond those in the partnership.
An increase of the upper limits for H2S may reduce the cost of future CCS chains. Knowledge from this project will also be important input to requalification of used oil and gas pipelines for CO2 transport.