Solvents for the next generation of post combustion CO2 capture systems (SOLVit – Phase 3)
Budget
156.1 MNOKCLIMIT Financing
43%Project number
227647Project partners
- • Aker Engineering & Technology AS
- • SINTEF
- • NTNU
- • EnBW
Project leader
Aker Engineering & TechnologyProject period
2013-2015Granted
05/11/2013The project has the main focus on the development of energy-efficient and environmentally friendly absorption processes for CO2 capture plants (post combustion capture). The project works with areas such as the development of improved solvents, process optimization, technology development and validation. The goal is to reduce the environmental impact and costs of implementing CO2 capture through technology improvements.
Phase 3 of the SOLVit project is based on the experiences and results gained in phases 1 and 2. In order to achieve the project’s overall goals, in phase 3 of SOLVit, work has continued on two different tracks:
1. Optimization and validation of the most promising 1st generation solvents and processes from phases 1 and 2 through laboratory and pilot experiments
2. Identification and development of new promising 3rd generation processes that can provide a significant reduction in energy consumption. The purpose has been to obtain “proof of principle” for 3rd generation processes by demonstration at the Tiller pilot plant
SOLVit 3 was launched in July 2013 and completed in December 2015. Phase 3 of the project has been structured in the same way as phases 1 and 2 and consists of four work packages:
WP1: Development of chemicals including third generation processes
WP2: Modeling of solvent systems and capture facilities
WP3: Pilot and demo tests
WP4: Development of new technology
In addition, NTNU has implemented a competence building program (funded separately by the Research Council of Norway and Aker Solutions) which has assisted SOLVit with more basic research into absorption processes.
In WP1, work has continued on the characterization and improvement of the most promising amine mixtures (1st gen. Solvents) identified in phases 1 and 2. In addition, there has been a great focus on the development of chemicals for third-generation processes that are expected to give the greatest reduction in energy consumption. Blue. it has worked with concepts with two liquid phases. The most promising 3rd gen. solvents are further characterized for key properties such as VLE, corrosivity to steel, oxidative and thermal degradation. The work with the development of advanced analysis methodology for increased understanding of degradation mechanisms has continued also in phase 3 where SINTEF has developed very sensitive analysis methods for amines and degradation products. The build-up of this expertise has made it possible to analyze thousands of solvent samples from the many test campaigns at various pilot plants.
In WP 2, SINTEF has continued the development of the process simulation tool CO2SIM. In phase 3, CO2SIM has been upgraded with more sophisticated thermodynamic models for the best 1st gen. solvents so that CO2SIM can handle multicomponent chemical mixtures and thus improve accuracy. CO2SIM has been widely used to validate results from test campaigns from pilot plants and to evaluate the potential for various process improvements.
As part of the technology development in WP4, the technology for thermal purification of amines (reclaiming) has been further developed and optimized for the 1st gene. solvents. This has resulted in a reclaimer design and procedures for reclaiming with a minimum of amine loss and waste production. By applying the advanced analysis methods from WP1 to samples from reclaiming experiments, it has been possible to document the fate of the individual degradation products during reclaiming. WP4 has also worked on testing various low-cost building materials for amine plants, including polymer materials, various steel grades and concrete. This has resulted in the qualification of three new PP materials for cladding concrete absorbers with a life expectancy of more than 40 years. For the best 1st gen solvents, it has also been demonstrated that carbon steel can be used in direct contact with amine in many parts of the plant with completely insignificant corrosion rates. In addition, it has been shown that ordinary stainless steel types (304 and 316) can be used throughout the plant without significant corrosion.
An important part of SOLVit phase 3 is the work with demonstration and validation of existing and new chemical mixtures in pilot plants (WP3). More than half of the budget in phase 3 has been spent on building, modifying and operating pilot plants. A total of four different pilot plants have been used in phase 3: SINTEF’s research pilot at Tiller in Trondheim, Aker Solutions Mobile Test Unit (MTU), EnBW’s pilot plant at a coal power plant in Heilbronn, Germany and the large amine plant at TCM. A total of 11 different test campaigns have been carried out with around 20,000 operating hours during phase 3. The test campaigns at MTU, Heilbronn and TCM have played a key role in testing first-generation solvents on real exhaust gas from both gas power plants, coal power plants and cement plants. The propane-fired pilot plant at Tiller is primarily used for testing third-generation solvents in a more controlled environment.
The main results in phase 3 that have been achieved in relation to the project’s objective of reducing energy consumption are summarized below:
– The 1st gen has been developed. solvents with significantly improved energy consumption. Compared with the project’s references «Bellingham plant» (gas power) and Esbjerg pilot plant (coal power), the pilot plants have been demonstrated an energy saving of 10-25% with first generation solvents
– In combination with process improvements such as Energy Saver or heat integrated stripper, it is shown with CO2SIM that improvement of up to 35% is possible with first generation solvents compared to the reference value
– Test with 3rd gen. solvents at the Tiller pilot plant indicated almost 30% reduction in energy consumption using the “standard” process with the possibility of further reduction in process improvements
In addition to improvements in energy consumption, the work with the development and validation in SOLVit has offered a number of other improvements to solvent-based CO2 capture technology, including:
– More environmentally friendly amines with improved operational properties (low degradation and corrosion rate) have been developed
– Very low emissions to air of amines and degradation products have been demonstrated
– Development of highly sensitive analysis methods and identification of all significant degradation products has reduced the uncertainty associated with the environmental impact of amine processes
Demonstration of solvents and capture technology on a much larger scale than hitherto (TCM about 2-10% of full scale)
– Equipment and construction materials have been function tested
– Environmental and health aspects have been thoroughly investigated
All this has led to Aker Solutions now being very well equipped for the choice of solvents and upscaling and design of full-scale facilities for CO2 capture.
Publikasjoner (SOLVit fase 3):
A. Grimstvedt, E. F. da Silva and K. A. Hoff, Thermal degradation of MEA, effect of temperature and CO2 loading, Trondheim Conference on CO2 Capture, Transport and Storage , TCCS-7 Trondheim (2013)
G. Fytianos, S. Ucar, A. Grimstvedt, H. F. Svendsen, H. Knuutila, Corrosion evaluation of MEA solutions by SEM-EDS, ICP-MS and XRD, The 8th Trondheim Conference on Capture, Transport and Storage (2015) (also submitted to Energy Procedia 2015)
J. N. Knudsen, O. M. Bade, M. Anheden, R. Bjorklund, O. Gorset, S. Woodhouse, Novel Concept for Emission Control in Post Combustion Capture, Energy Procedia, 2013, 37, 1804-1813
M. Gupta, S. J. Vevelstad and H. F. Svendsen, Energy Procedia 2014, 63, 1115-1121.
O. Gorset, J. N. Knudsen, O. M. Bade, I. Askestad, Results from testing of Aker Solutions advanced amine solvents at CO2 Technology Centre Mongstad, Energy Procedia 2014, 63, 6267-6280
O. M. Bade, J. N. Knudsen, O. Gorset, I. Askestad, Results from testing of Aker Solutions advanced amine solvents at CO2 Technology Centre Mongstad, Energy Procedia 2014, 63, 884-892
S. J. Vevelstad, A. Grimstvedt, H. Knuutila and H. F. Svendsen, Energy Procedia 2013, 37, 2109-2117
S. J. Vevelstad, A. Grimstvedt, J. Elnan, E. F. da Silva and H. F. Svendsen, International Journal of Greenhouse Gas Control 2013, 18, 88-100
S. J. Vevelstad, A. Grimstvedt, A. Einbu, H. Knuutila, E. F. da Silva and H. F. Svendsen, International Journal of Greenhouse Gas Control 2013, 18, 1-14
S. J. Vevelstad, A. Grimstvedt, H. Knuutila, E. F. da Silva and H. F. Svendsen, International Journal of Greenhouse Gas Control 2014, 28, 156-167
S. J. Vevelstad and H. F. Svendsen, Energy Procedia 2016, 86, 181-196
Poster TCCS-8 (2015): S.J. Vevelstad & H. F. Svendsen, Challenges related to analysis of anions in degraded samples from pilot and lab experiments
Publikasjoner (SOLVit fase 1 og 2):
1. Mejdell, T., Vassbotn, T., Juliussen, O., Tobiesen, A., Einbu, A., Knuutila, H., Hoff, K.A., Andersson, V., Svendsen, H.F., ”Novel full height pilot plant for solvent development and modell validation”, GHGT-10, Energy Procedia, 4:1753-1760, (2011).
2. Lepaumier, H., da Silva, E.F., Einbu, A., Grimstvedt, A., Knudsen, J. N., Zahlsen, K., Svendsen, H.F., ”Comparison of MEA degradation in pilot-scale with lab-scale experiments”, GHGT-10, Energy Procedia, 4:1652-1659, (2011).
3. Vevelstad, S.J., Eide-Haugmo, I., da Silva, E.F., Svendsen, H.F., ”Degradation of MEA; a theoretical study”, GHGT-10, Energy Procedia, 4:1608-1615, (2011).
4. Tobiesen, A., Schumann-Olsen, H., “Obtaining optimum operation of CO2 absorption plants”, GHGT-10, Energy Procedia 4:1745-1752, (2011).
5. Gupta M., da Silva E.F., Svendsen H.F., “Temperature Sensitivity of Piperazine and its Derivatives using Polarizable Continuum Solvation Model” published in the proceedings of the ICBEE 2010 by IEEE.
6. Owrang F., Svendsen H.F., “Estimating the Heat Losses from a Laboratory Pilot Plant For CO2 Absorption”, ICBEE, Egypt, November 2-4, 2010.
7. Gupta M., “Temperature sensitivity of Piperazine and its derivatives using Polarizable Continuum Solvation Model”, 2nd International Conference on Chemical, Biological and Environmental Engineering (ICBEE 2010), Cairo, Egypt.
8. Vevelstad S.J., Grimstvedt A., Lepaumier H., Zahlsen K., Kjos M. and Svendsen H.F., “Identification and quantification of amine degradation products by Ion Chromatography”, The PACIFICHEM 2010, Honolulu, Hawaii, USA, 15-20 December 2010.8. Owrang F., Svendsen H.F., Knuutila H., Juliussen O., “Detailed Estimation of Heat Losses from a Laboratory Pilot Plant for CO2 Absorption”, submitted to 1st Post Combustion Capture Conference 17th -19th Abu Dhabi, May 2011.
9. Trollebø A.A., Svendsen H.F. (2010), Third generation solvents for post-combustion CO2 capture, Pacifichem conference, 15-20 December 2010, Honolulu, HI, USA (OP).
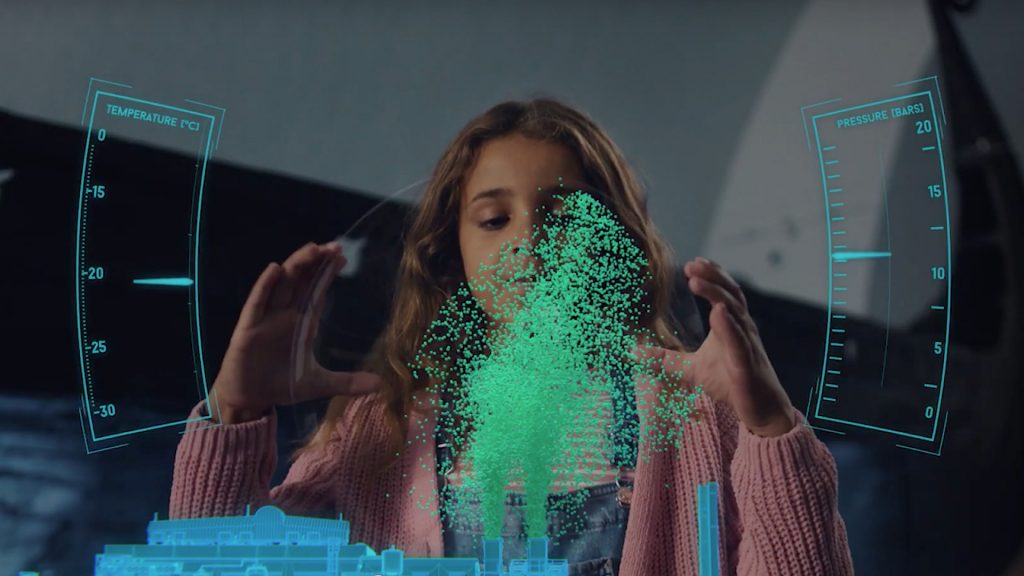