COMPMEM JIP
Budget
38 MNOKCLIMIT Financing
50%Project number
617322Project partners
- • Equinor
- • TotalEnergies
- • Pertamina
- • CCP (allianse av BP, Petrobras, Chevron)
Project leader
Aker Carbon Capture ASProject period
05/19-03/23Granted
25/06/2018Background
There are large oil reserves in offshore fields that cannot be produced with conventional methods, but which can be produced with CO2 flooding, so-called CO2 EOR. CO2 EOR is considered a sustainable way to produce this oil as it involves storing all the injected CO2 gas. At the same time, the large offshore reservoirs can be used as storage sites for CO2 from external capture sources after the oil extraction phase.
However, many studies have concluded that one of the obstacles to using CO2 flooding offshore is the large costs associated with rebuilding existing offshore installations to handle the CO2-rich back-flowing well stream. In addition is the challenge related to the corrosive environment caused by the CO2 content in the well stream.
The project has therefore considered using subsea technology to separate the CO2 gas in a subsea process plant and inject the gas before it reaches the topside installations. The biggest uncertainty for such a process solution has been assumed to be the functionality of a gas separation process with selective membranes. An important purpose of the project has therefore been to test relevant membranes and make an assessment of whether such a subsea solution can enable a sustainable use of CO2 EOR in offshore oil extraction.
Project objective
Obtain knowledge and data for a gas separation process with selective membranes in a process window for a subsea based separation and injection train. It was also important to establish knowledge of how robust the membrane systems are when exposed to condensable components such as carbonic acid and hydrocarbon mixtures.
Based on the knowledge that would be created through these tests, the project should also make an updated assessment of the technical-economic basis for such a subsea-based process solution in order to clarify the basis for further development and commercialization
Activities
Extensive tests have been carried out in small scale to measure the separation properties of various membrane qualities. The tests have mainly been carried out by Sintef in Trondheim and Oslo. The membranes have been tested systematically by changing various external factors that affect the separation, such as pressure, temperature, differential pressure across the membrane, gas velocity and gas mixtures with different CO2 and CH4 contents. There have also been done tests where the membranes have been exposed to H2S and H20 as well as examining the effect of membranes that have been exposed to condensing liquids.
A systematic test program has also been carried out involving exposure the various components of a membrane module to condensing liquids. The materials have been tested before and after these exposures to assess mechanical durability and whether irreversible degradation of the polymer materials could possibly occur as a result of the exposure.
Based on the results from the small-scale separation tests and the material tests, two out of four membrane qualities were qualified as relevant for subsea separation. These qualities were therefore tested on a representative industrial scale in a pilot plant. The pilot plant was designed and operated by Sintef at Tiller. The tests were carried out by systematically varying the external parameters, but with a more limited test program than in the small-scale tests.
The project used methods for statistical design of experiments in the planning of the tests and developed empirical models to describe relationships between the external parameters and membrane performance measured as permeance and selectivity. The project also prepared physical models that describe the fundamental processes for mass and energy balances around a membrane separation process.
The project has carried out extensive engineering work to design a compact membrane separation system for a modular topside solution. In addition, the focus has been on engineering work for the subsea concept to find optimal operating conditions and separation data for the process train.
Results
The project has provided important information on the feasibility and properties of different membrane qualities for the separation of CO2 from a CO2-rich gas stream under conditions that are relevant for a subsea process solution. In practice, this means knowledge of which limitations must be considered when designing a subsea gas separation plant, the consequence of operating the plant under different conditions on the need for equipment and compression solutions. From the analysis that has been made based on the results, it has been documented that up to 97 – 98% of the CO2 introduced into the gas separation train can be separated for further compression and reinjection into the reservoir.
The effect of the various process conditions on how much CO2 is included in the remaining well flow to the top side is also described.
From the material tests, knowledge has been obtained about the effect the condensing liquids have on various polymer materials, which in turn dictate requirements for conditions that should be avoided in the subsea process plant. The liquid exposures show that the polymer materials partly swell, and some are irreversibly destroyed by the exposure.
The project has delivered a solution for a modular process plant for a conventional topside application with estimates for weight and costs.
A study has also been submitted that describes a complete subsea solution for a process train. This process package provides information on the technical solutions, assessments of the technology gaps, mass and energy balance for all components in the well flow and an estimate for the carbon footprint.
The project has thus achieved the specified objectives with the exception of cash flow analyses, which were not carried out. The primary reason for this is that the design basis that was used was aimed at testing membrane functionality to the greatest extent possible under various conditions. The design basis was not applicable for a cash flow analysis considering the value of increased oil production, costs for CO2, etc.
Future plans
The Aker companies are in ongoing discussions with relevant stakeholders who see the commercial application of the technology. Further qualifications will therefore depend on the commercial interest.
The clients consider that the most short-term commercial use is for the development of CO2-rich gas fields, which are considered to have very relevance and simpler technological solutions than for the main case used in the COMPMEM project.
The most important area for qualification of the concept is considered to be the compact solution for arranging membrane modules in a pressure tank suitable for installation in a subsea process train.
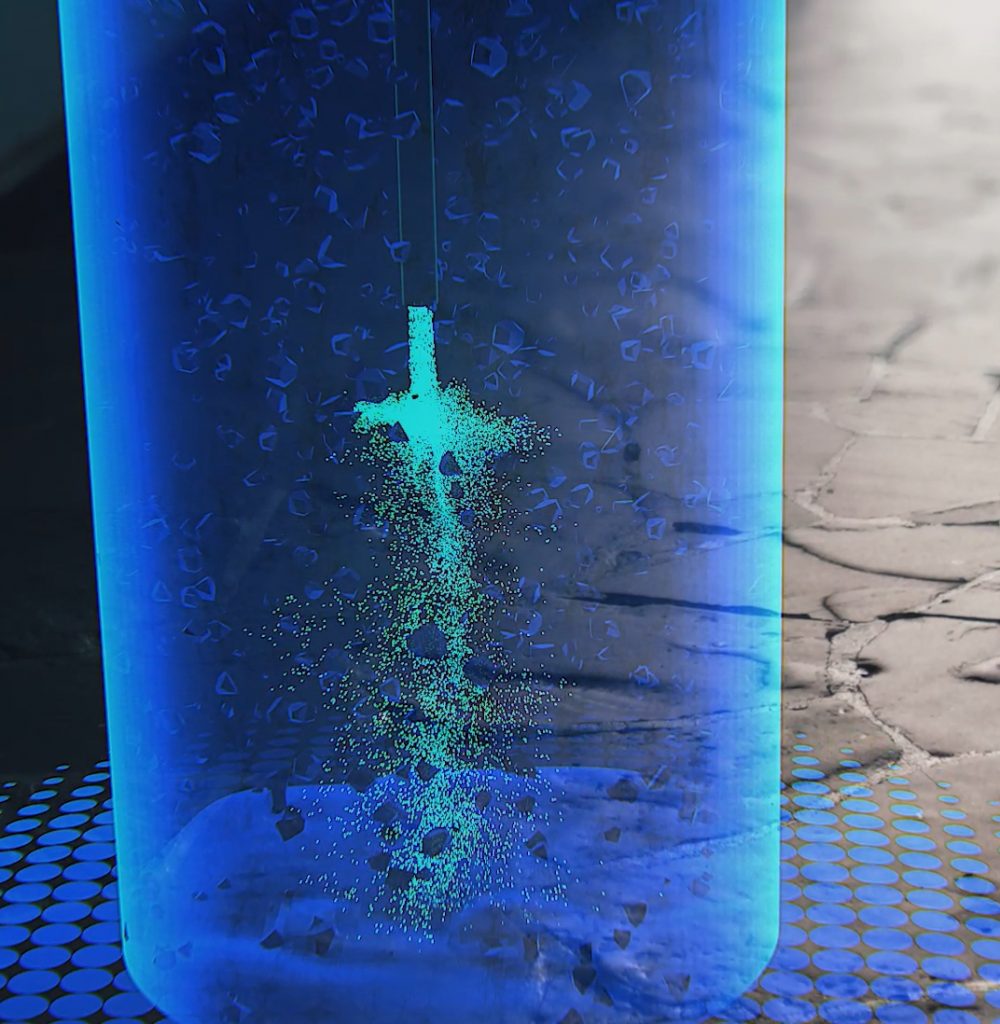