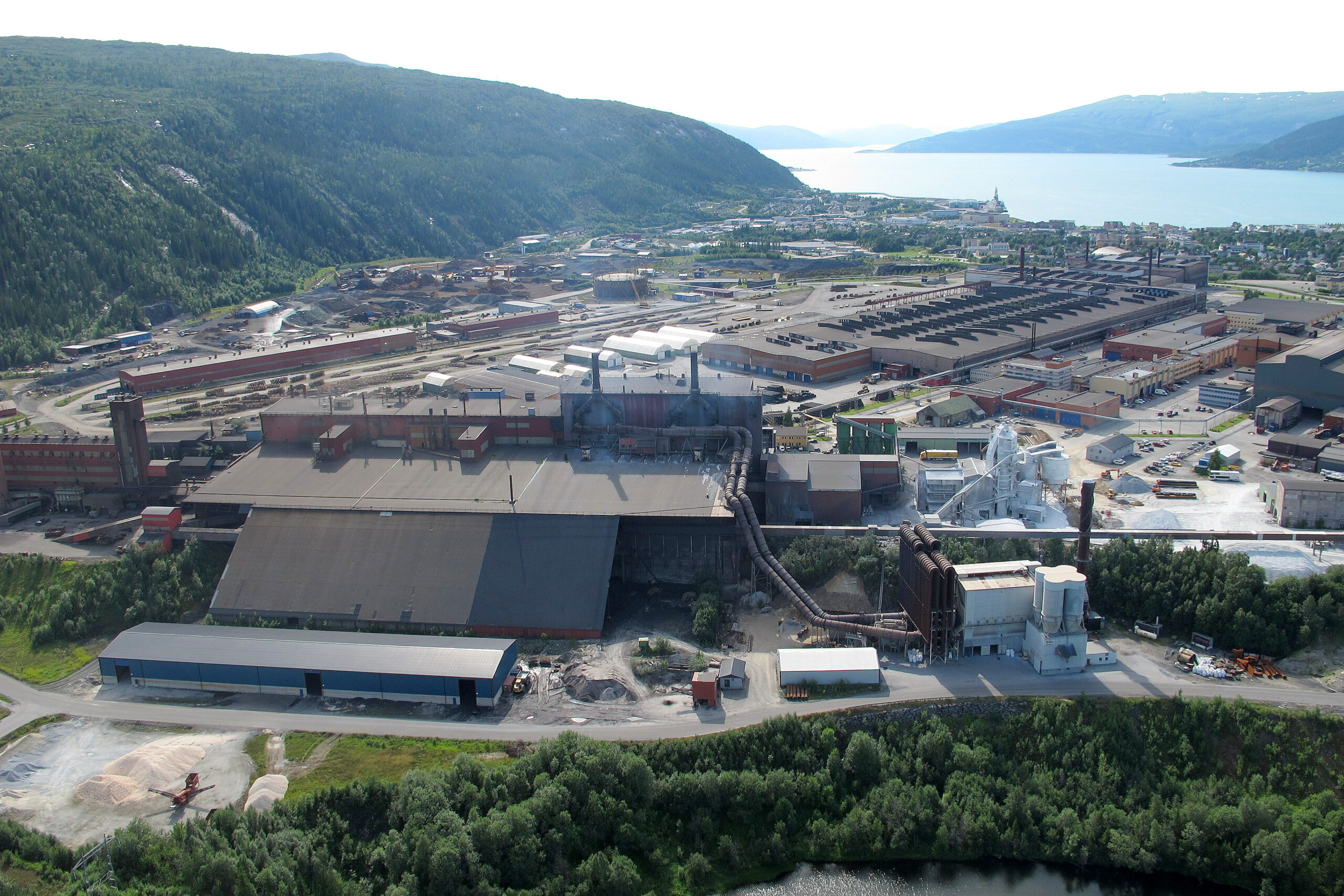
01.06.2022
The voyage towards carbon capture
Together with partners, Elkem has instigated a project for testing technology that captures CO2 from smelters. This is the first time such technology is applied to flue gas emissions in the ferroalloy industry.
The project draws on a goal-oriented, systematic effort to build competence in the field of carbon capture.
The process industry must play a central role in the struggle to achieve the overarching goal of the Paris agreement: Limiting long-term temperature increase to well below 2℃. A shift from fossil fuels to green energy, will not alone suffice to cut emissions. In fact, many industrial companies produce more CO2 than finished product. Therefore, high costs become the bottle neck for implementing carbon capture plants. This means that the research community and the industry together must find pragmatic solutions that the industry can adopt rapidly.
And one of the drivers behind CCS in the Norweigan process industry is Elkem, one of the world’s leading provider of advanced silicon–based materials.
A necessary collaboration
Bringing about substantial changes requires knowledge in new areas.
«Elkem’s voyage started around 2017,» says Elkem’s climate director Trond Sæterstad. «At that time, Elkem joined CO2 Hub Nord.» This initiative for collaboration on CCS and infrastructure, consists of industrial players in Mo i Rana industrial park and companies further north, as well as in the county of Trøndelag.
Since Elkem has production plants at several locations in Norway, the company has been a proactive contributor in an array of CCUS industrial collaborations – such as the Eyde cluster, the Mid-Norway cluster, in addition to CO2 Hub Nord. The latter is currently starting up tests of CO2 capture from the flue gases of Elkem and SMA Mineral.
In these cluster projects – all of which receives financial support from CLIMIT – the member companies are investigating solutions for CCS, local infrastructure and logistics.
«It’s a huge advantage for adjacent industry to collaborate in order to establish sound solutions for local infrastructure and logistics. That’s why the cluster projects are so important. This way, it’s possible to source large volumes of CO2 for storage, and the companies can share costs related to infrastructure and transport,» says CLIMIT’s Jørild Svalestuen.
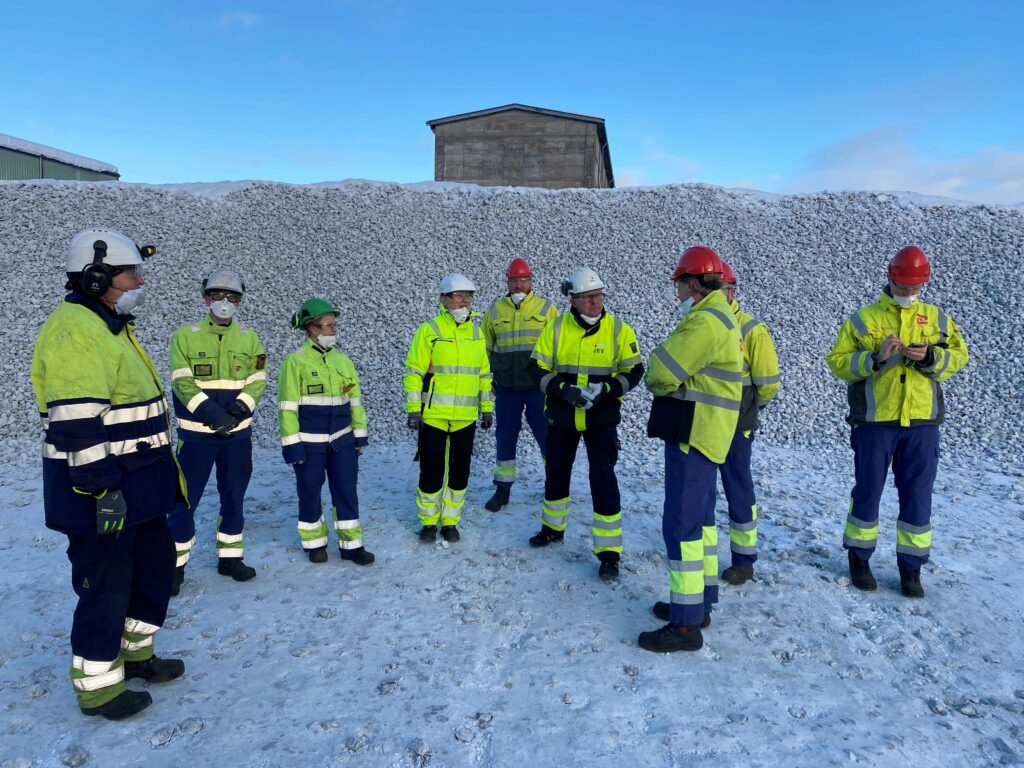
A learning process
Elkem has focused on several areas.
Between 2015 and 2019, the company participated in the CLIMIT-supported project CO2stCAP, a cooperation between Norwegian and Swedish industrial companies and research communities. The purpose was to analyze processes and identify factors that drive down costs in carbon capture projects.
Elkem also participated in Process 21, a cooperation and knowledge sharing initiative between Norwegian companies. The forum directed attention toward identifying solutions to reduce the total emission of the national process industry. The steering committee was headed by Håvard Moe, Elkem’s senior vice president for technology.
In 2021, Elkem launched the Global Climate Roadmap. This strategy defines CCS as central to reaching the company’s goal of sustainable production of materials.
A study of opportunities
Through this multi-faceted work, Elkem acquired the competence required to take the next step. The company was ready to investigate practical, operational carbon capture solutions for its smelter plants. In parallel with CO2 Hub Nord, the company executed a feasibility study, which was completed in 2021.
The purpose of the study was to devise a business model for the installation of CCS technology at Elkem’s smelter plants. The model evaluates all critical factors related to operating such technology. By closely considering a diverse set of operating conditions – such as technical status – at the smelter plants, the model calculates with a high level of precision, what it will cost to implement capture installations at the local plants.
Two solvent technologies – from Saipem and Aker Carbon Capture – were evaluated according to the needs of the smelter plants. How could the technologies be adapted to the operational environments? How well suited were they to extract CO2 from the flue gas emitted during the production process?
«It was an incredibly exiting exercise,» says Ragnhild Jensen, project director in Elkem. «We needed to learn more about the practical aspects of CCS. What do we have to do on our side of the interface? How must the plants prepare and facilitate the installation of the new technology? What happens in the capture process? What’s the output? And – not least – what is required in terms of energy integration?»
Elkem brought in Norsk Energy, a consultancy specializing in environmentally friendly and safe use of energy, in order to evaluate the energy integration aspects of the technology from the two suppliers.
«The project gave us a better understanding of the efficiency of capture, the technical requirements that the vendors specified for Elkem’s flue gas, and the output of the technologies,» says Ragnhild Jensen.
The result was a significantly improved process design for the implementation of CCS technology.
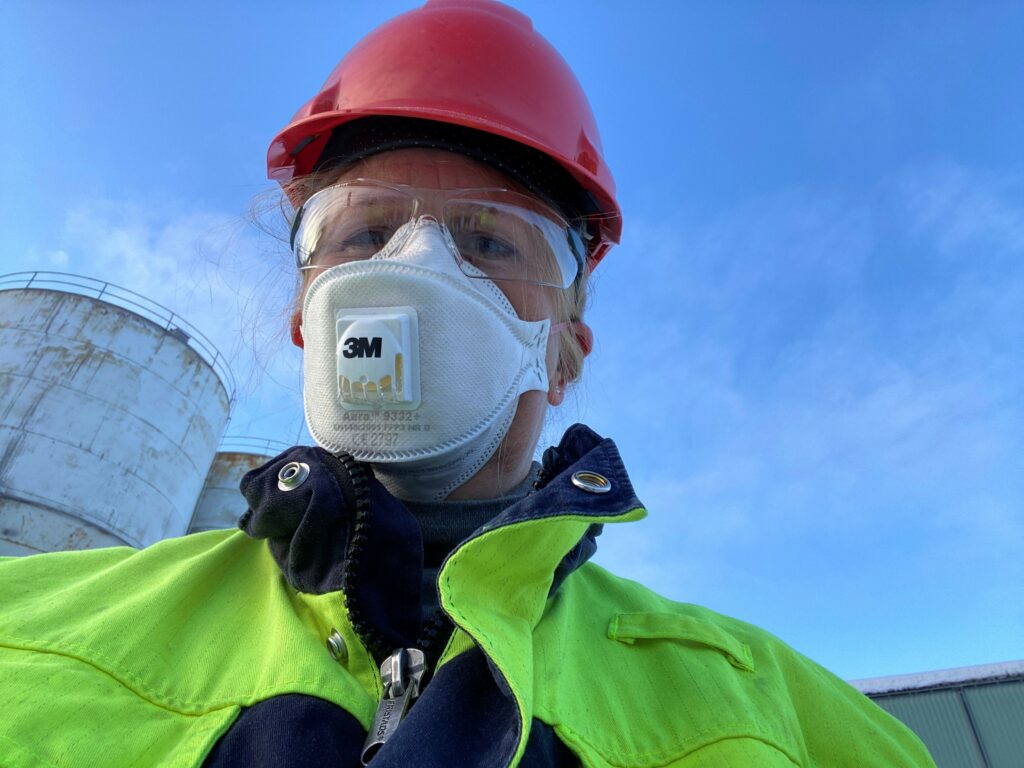
One step further
The knowhow that Elkem acquired through meticulous preparations, has been essential in order to carry out comprehensive testing at the smelter plants.
«The natural next step for us, is to verify the technology at our plants,» says Trond Sæterstad, Elkem’s climate director. «Before we can make an investment decision, the capture installations must be tested and evaluated in an operational setting.»
Now, the ferrosilicon producer Elkem is starting up – under the auspices of the CCUS industrial consortium CO2 Hub Nord – the first pilot project of its kind. During six months, the company will operate a mobile test unit from Aker Carbon Capture – a full-scale capture plant in miniature.
The capture technology from Aker Carbon Capture will be tested on separate flue gases from Elkem Rana and SMA Mineral. However, the project will also test CO2-cleaning from jointly sourced flue gas from the two producers.
The last alternative opens up for exciting prospects. The option of gathering streams of flue gas from several producers, will translate into significant cost reduction for each industrial company.
And this is critical. Because it’s imperative to reduce costs.
CO2-hub participants. Rana-MTU building site.