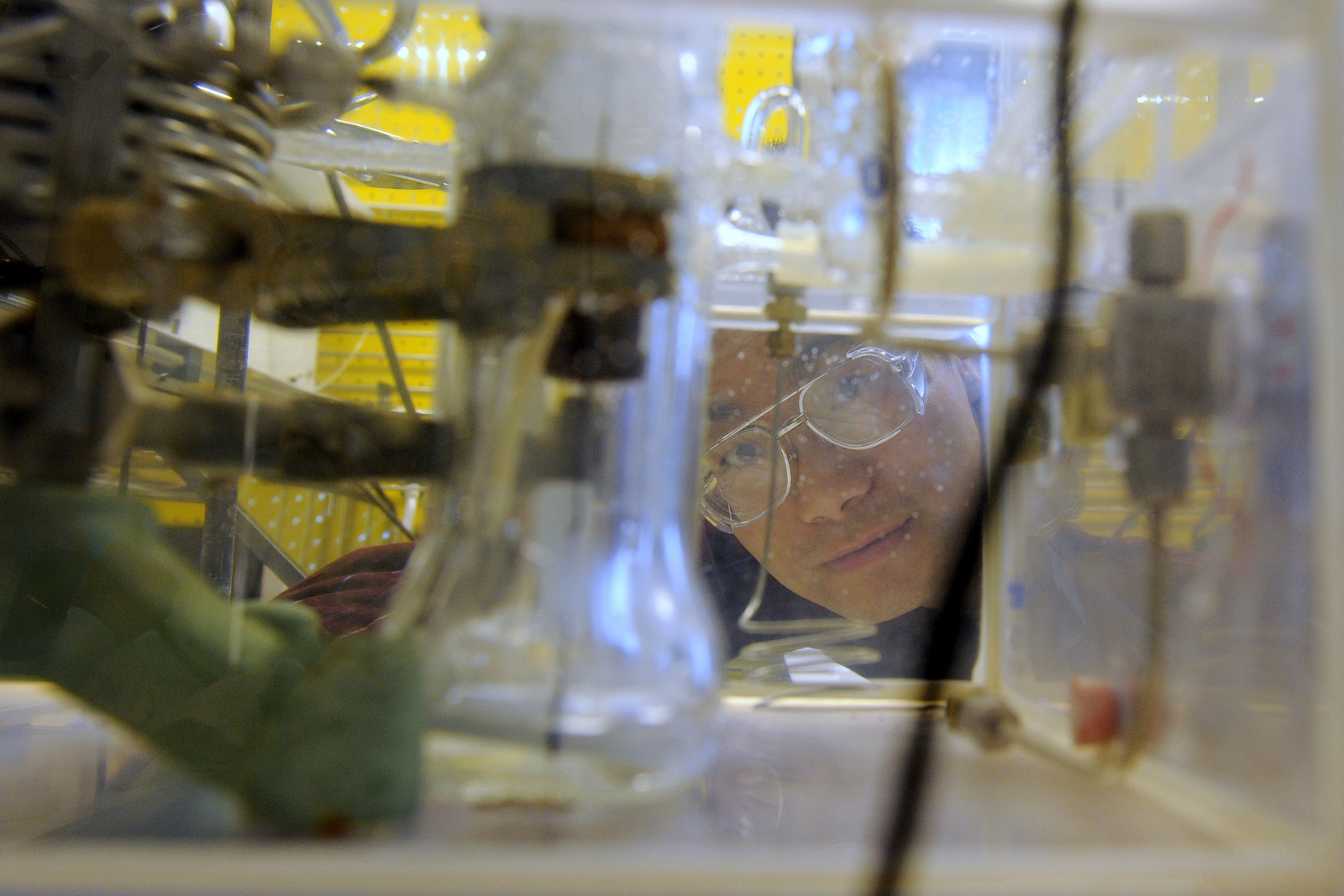
20.05.2025
From lab to Longship – with CLIMIT support
Through the Longship project, Norway has taken a leading international role in carbon capture and storage (CCS). The journey to realising the project has been long and challenging, particularly when it came to the development of practical fullscale carbon capture technology.
Support from CLIMIT true SOLVit has been vital for the development and testing of technology that are now capturing CO2 at the Heidelberg Materials capture facility at its cement factory in Brevik, “Brevik CCS”.
SLB Capturi
SLB Capturi (formerly Aker Carbon Capture) developed its amine technology through the SOLVit programme. After extensive testing at the Heidelberg Materials (formerly Norcem) test centre in Brevik, the technology was chosen as the preferred solution for fullscale demonstration of carbon capture at the cement factory. The capture facility is a core part of the Norwegian CCS demonstration project Longship.
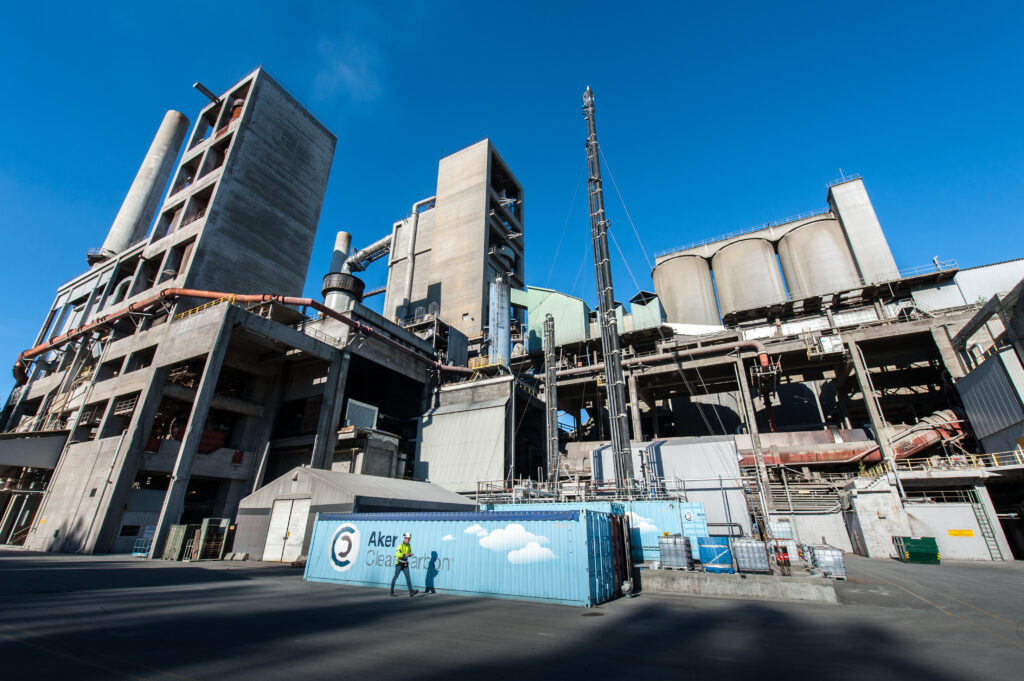
Aker’s test facility in operation at Brevik CCS. Photo: Styrk Fjørtoft
SOLVit-programmet
The SOLVit programme (2008-2015) was a major research and development programme that focussed on improving carbon capture solvent and process technologies. The programme was led by Aker, with research activities carried out by SINTEF Industry in Trondheim in collaboration with Aker and the Department of Chemistry at NTNU. A number of industry partners and potential end users of carbon capture technologies, including EnBW, E.ON, Scottish Power and Statkraft, contributed actively to various parts of SOLVIT
The programme was partially funded by CLIMIT and the Research Council of Norway, with a budget of NOK 332 million, of which NOK 132 million (40 percent) came from CLIMIT.
“The SOLVit programme and CLIMIT’s support contributed to the maturation of SLB Capturi’s capture technology, in particular our energy-efficient and robust solvent which was developed to have the smallest possible environmental impact. The further testing at the Heidelberg Materials cement factory in Brevik demonstrated that our amine technology was mature and ready for fullscale implementation. Now in December 2024, the plant in Brevik is complete and ready for start-up and testing, and the carbon capture will begin over the course of 2025. A fantastic development from the SOLVit programme so far.”
Jim Stian Olsen, CTO, SLB CapturiObjectives for the SOLVit Programme
The primary goal was to reduce the cost of carbon capture from emission sources through the development of more energy-efficient solvent systems and adjusted process technologies. Other goals included developing more environmentally-friendly solvents and demonstrations of performance improvements of the new solvents at pilot scale.
Programme overview
The SOLVit programme was implemented in three phases, with each phase building on experience from the previous ones:
- Phase 1 (2008-2010): The development of functional solvents, establishing laboratory facilities and a stationary pilot facility at SINTEF Tiller.
- Phase 2 (2011-2012): Characterisation and pilot testing of first-generation solvents, focussing on the development of new, ground-breaking environmentally-friendly solvents and a reduction in the environmental impact of the carbon capture process.
- Phase 3 (2013-2015): Qualification of solvents through pilot testing of various industrial waste gases, demonstration at the Test Centre Mongstad, as well as the development of technology for cost reductions for carbon capture.
Organisation and training
SOLVit’s work was organised into four main areas: Basic studies, modelling, technology development, and pilot testing and demonstration. Through the SOLVit project, highly sensitive LCMS methods were also developed for quantifying degradation products in solvents, with sensitivity of less than 1 ng/ml. Methods were developed for over 50 amines, as well as specific methods for alkylamines, nitrosamines and other degradation products.
A training programme was also introduced at NTNU, which contributed to basic research on solvent-based capture processes. Many doctoral and masters students carried out their studies through this programme, contributing to the training of qualified researchers within carbon capture technologies.
SOLVit provided vital results
Pilot testing showed that SOLVit solvents were robust, energy-efficient and environmentally friendly. An improvement of up to 35 percent in energy consumption compared with MEA (Monoethanolamine) was demonstrated, as well as significantly lower solvent consumption and degradation rates. Amine emissions and degradation products could be kept at far lower levels, reducing uncertainty related to the environmental impact of amine-based capture processes.
In summary, the eight-year-long SOLVit programme provided increased understanding of solvent-based capture processes at both the basic and industrial level. Many new solvents for carbon capture from waste gases were developed. The programme contributed significantly to the maturation of Aker’s carbon capture technology, and reduced the risks related to scaling up and large-scale implementation.
For more information about SOLVit, see here:
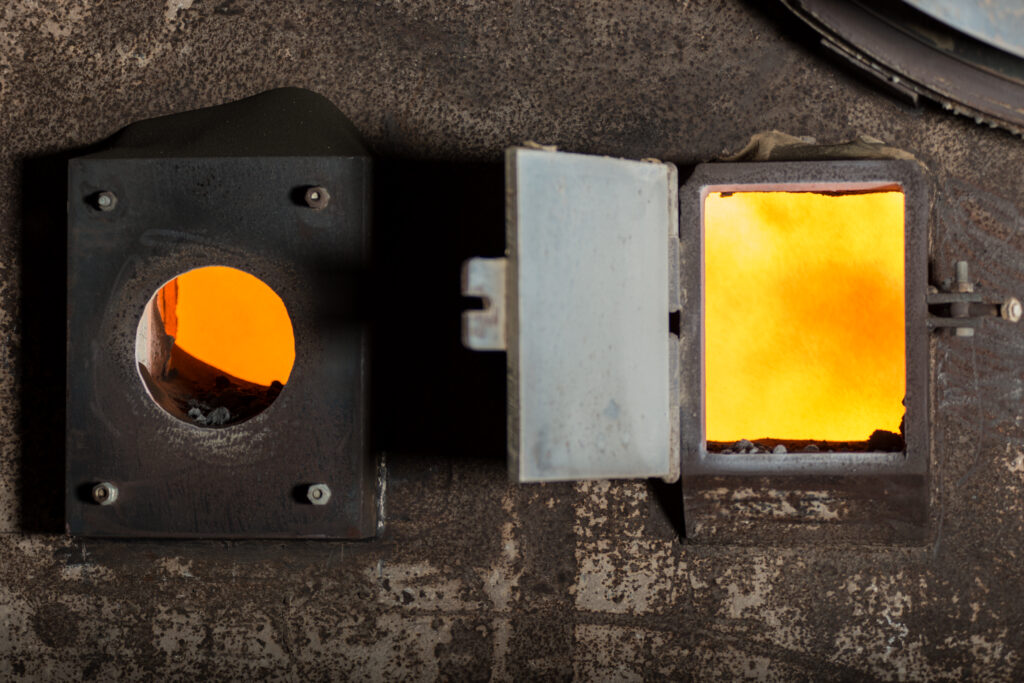
Norcem Test Centre (Heidelberg Materials Brevik)
The primary aim of the test centre was to evaluate and compare selected carbon capture technologies to find the most suitable option for emissions from the Heidelberg Materials cement factory in Brevik. The project had a total budget of NOK 93 million and received NOK 70 million (75 percent) from CLIMIT Demo. ESA (European Surveillance Authority) approved the high level of state support. The project ran from 2013 to 2015.
The project focussed on the capture part of the CCS chain, with a focus on CO2 capture capacity, energy consumption, impact of pollutants and costs. The utilisation of residual heat from the factory was also important.
The test centre project consisted of two main parts:
1) Pilot testing:Testing under real-world conditions on emission sources from the cement factory in Brevik
2) Fullscale evaluations: Field testing and modelling for fullscale implementation
In Phase I, four technologies were selected: Aker Carbon Capture Amine Technology, RTI Solid Sorbent Technology, KEMA GL/NTNU & Yodfat Engineers Membrane Technology, and Alstom Power Regenerative Calcium Cycle. In Phase 2, RTI Solid Sorbent Technology Phase II and Air Products & NTNU Membrane Technology were studied.
“CLIMIT’s support for our test centre in Brevik has been key to our work on developing and implementing ground-breaking carbon capture and storage technologies. The support has been a vital driving force in Heidelberg Materials’ development of the world’s first CCS cement, evoZero, which will allow the construction and engineering sector to cut out significant volumes of CO2 by using climate-neutral cement.”
Pia Prestmo, Manager Public Affairs Norway, Heidelberg MaterialsResults and further work
Testing covered needs for technological optimisations. Aker’s amine technology was identified as the most mature and ready for fullscale demonstration. As a result, SLB Capturi (formerly Aker Carbon Capture) is chosen as the technology supplier for Heidelberg Materials’ fullscale carbon capture project, which is today a part of Longship.
For more information about the Norcem test centre (Heidelberg Materials in Brevik)