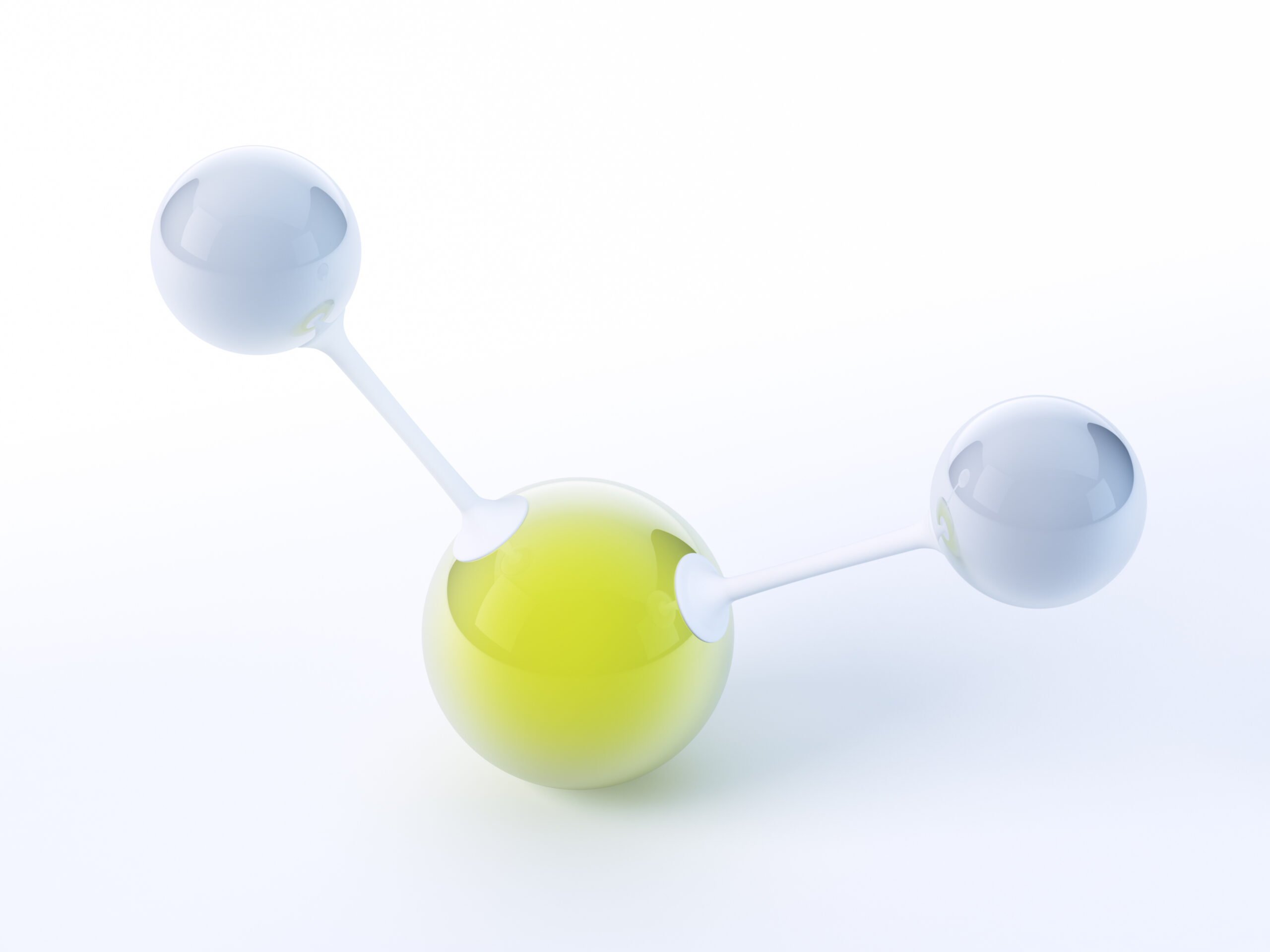
29.04.2025
Clean Hydrogen with Hybrid CO₂ Capture
The MACH-2 project has developed a hybrid process for hydrogen production from natural gas, achieving high efficiency and a high CO2 capture rate.
Combination of membrane technology and liquefaction results in excellent energy efficiency and high purity of the end products. The project MACH-2 was a collaboration between SINTEF Industry, SINTEF Energy, and NTNU. CLIMIT supported the project with NOK 7.5 million.
A Key Energy Carrier
Hydrogen is a crucial energy carrier in the transition to a low-emission society. To reduce greenhouse gas emissions associated with hydrogen production from natural gas, CO2 must be effectively captured and managed. The MACH-2 project, which ran from 2019 to 2024, developed a novel process that integrates two established capture technologies.
– Our approach was to combine hydrogen production using Protonic Membrane Reformer (PMR) technology with low-temperature CO2 capture via liquefaction in a new, integrated process – where both technologies operate within their optimal performance ranges, says Thijs Peters, Project Manager at SINTEF Industry.
CO2 Purity and Calorific Value
The membrane technology uses ceramic materials to produce hydrogen from natural gas, which is reformed directly on the membranes. The process is powered by electricity and internal heat generated during hydrogen separation through the membrane. The retentate gas, what does not pass through the membrane, contains CO2, water vapor and residual hydrogen.
– Membranes are excellent for extracting hydrogen, but there is a limit to how much can be recovered before efficiency declines. Therefore, we allow a portion to remain and capture CO2 in the subsequent stage, Peters explains. The retentate is then processed in a separate unit, where CO2 is liquefied through cooling and pressurization.
“This allows for high CO2 purity while recovering the remaining valuable molecules in the retentate, which can either be recycled back into the membrane process, or used as an energy source within the system. At the system level, the proposed concept separates approximately 99 % of both H2 and CO2, even when the membrane operates at relatively low hydrogen recovery rates. This results in energy-efficient H2 production with low carbon intensity”
Thijs Peters, project Manager at SINTEF Industry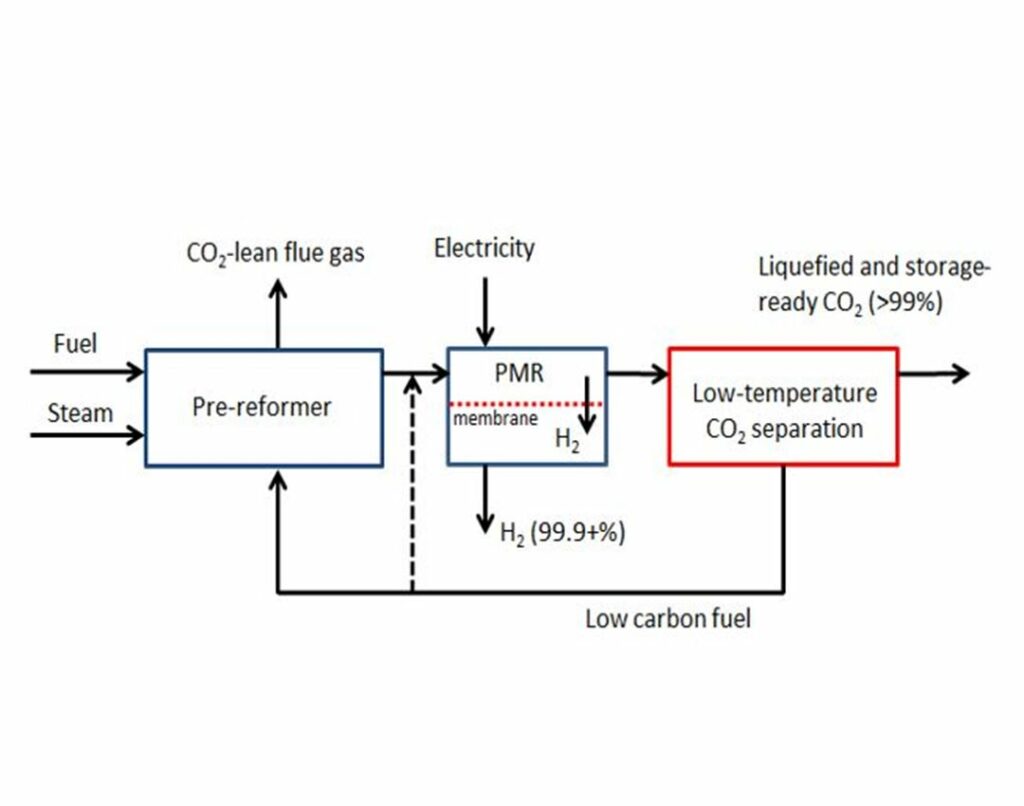
Model Validation
Several experiments were conducted during the project period. Membrane stability was tested for up to 1800 hours, including variations in gas composition and hydrogen withdrawal. Liquefaction experiments were performed using gas mixtures containing hydrogen, methane and carbon monoxide. To accommodate these experiments, the Cold Carbon Capture Pilot rig in Trondheim was upgraded. The tests demonstrated that CO2 could be separated at up to 99.9 % purity, under pressures between 40 and 70 bar and temperatures as low as -55 °C. – We compared the results with simulation models. The models aligned well with the experiments, which gives us confidence in relying on simulations for designing future systems, says the SINTEF Industry project manager.
Low Energy Loss and High Capture Rate
Through simulation and optimization, MACH-2 developed a process flow model for the entire system. It demonstrates that an integrated process provides higher energy efficiency and lower CO2 emissions, compared to more conventional hydrogen production methods with CO2 capture. This indicates that the concept is economically competitive.
Ready for Next Phase
Results are now being carried forward in new projects, including a planned demonstration facility with a hydrogen production capacity of 50 kg per day. The technology is also being applied in European projects where membranes are used for biogas capture.