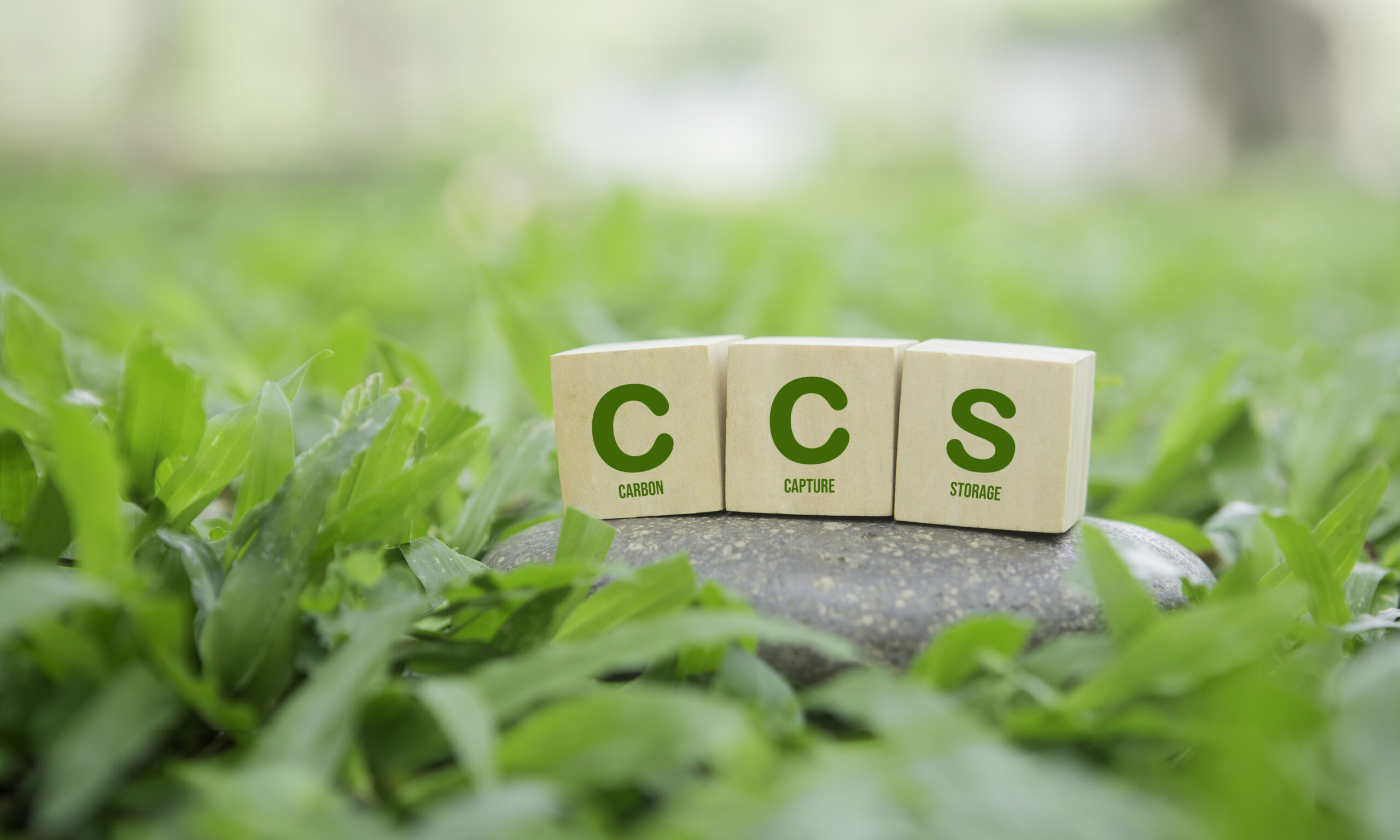
08.04.2025
Carbon Management; Project Aims to Transform CO₂ Adsorption Technology
The mission, jointly led by SINTEF and TotalEnergies, is focused on developing next-generation CO2 adsorption technology, which could significantly outperform today’s state-of-the-art solvent-based absorption systems.
The “Disruptive CO2 Capture” (CO2 Adsorption Technology) project has total budget of NOK 24 million, of which 50 % is financed by CLIMIT.
While CO2 capture using solvents is currently the dominant method, it remains expensive and energy intensive. Adsorption, where CO2 is captured by solid materials called sorbents, offers a promising alternative. The goal is clear; reduce both capital expenditure (CAPEX) and operating costs (OPEX), by at least 20 % compared to current leading absorption systems.
– We’re trying to find the best material-process combination. Ambition is to optimize both the sorbent material and the process design to reduce costs and improve efficiency, says Dr Shreenath Krishnamurthy, Senior researcher and Project Manager at SINTEF.
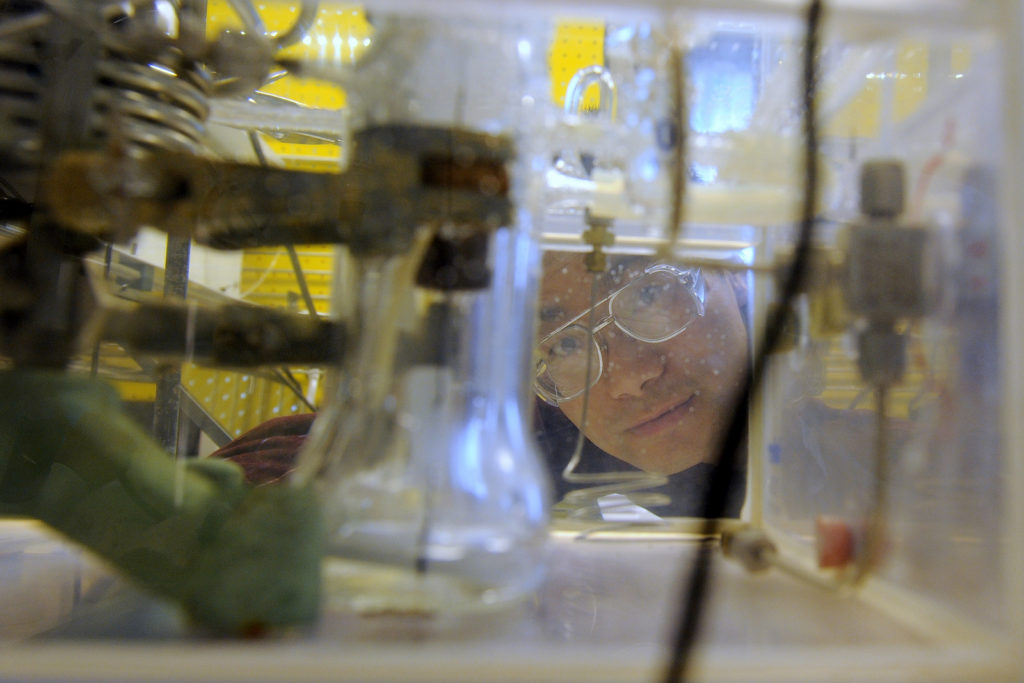
Why Adsorption?
Unlike solvent-based absorption systems, which rely on chemicals to bind CO2, adsorption uses solid materials to capture CO2 molecules directly from flue gases. Potential advantages are many; lower energy requirements, better atmospheric emission profiles, and possibly more compact plant designs. Adsorption is not yet mature for point source CO2 capture, with many technical hurdles to overcome.
“There are thousands of potential sorbents out there, from traditional to newly engineered materials. But which material works best with which process in terms of cost efficiency? That’s the question we’re trying to answer.”
Dr Samuel Heng, R&D Project Manager at TotalEnergiesA Theoretical Backbone
At the heart of the project is a sophisticated simulation model designed to test different combinations of materials and processes. DCC3 aims to evaluate temperature swing adsorption processes for NGCC flue gas. The team is building a flexible mathematical framework and cost framework which can simulate a range of adsorption processes from fixed beds, rotary beds, fluidized bed and moving bed processes, by switching specific parameters on and off. These simulations are grounded in gas-phase thermodynamics, adsorption kinetics, and equilibrium data.
The model will help the team optimize each process and adsorbent for performance and cost, validate key parameters, and ultimately select the most promising adsorbent and process configuration for future pilot testing.
– It’s not just about the best material; it’s also about finding the right process design. We’re doing a lot of simulation work to forecast CAPEX and OPEX, and we’re collecting and feeding experimental data to refine our models, Dr Shreenath Krishnamurthy continues.
Overcoming Data Gaps
One of the key challenges is the lack of publicly available data, especially concerning how sorbents interact with water vapor in flue gases. This has required new experiments and delayed some parts of the project. – In many cases, we don’t have the data we need from literature, so we’re measuring some properties ourselves, and also testing hypothetical ideal sorbents to understand the performance gap and identify research objectives to decrease carbon capture cost, says Dr Heng
The lack of data hasn’t stopped progress, but it has shaped the project’s direction. By exploring both existing and hypothetical materials, the team can map out what an ideal system would look like, and what would need to improve in current technologies to get there.
Broader Implications
Although this project focuses on post-combustion capture from natural gas combined cycle (NGCC) plants, its outcomes could influence other CO2 capture applications, including direct air capture.
The collaboration has already sparked two additional joint projects between SINTEF and TotalEnergies, focusing on carbon capture. The projects coordinated by SINTEF are funded by the clean energy transition partnership (CETP) and TotalEnergies plays an active role in the project.
One technical objective which stands out is minimizing the physical footprint of future carbon capture units. If adsorption technology can achieve both cost and space efficiency, it could make retrofitting existing plants, especially in space-constrained brownfield sites, much more feasible. – In greenfield cases, we have more flexibility. In brownfield projects, integration is very complex. This is why we need compact, efficient solutions, says Dr Heng at TotalEnergies.
Looking Ahead
The project aims to reach Technology Readiness Level (TRL) 4 within four years. By the end, partners will conduct a thorough comparison between the newly developed adsorption technology, and current solvent-based systems. This will form the basis for a “go/no-go” decision regarding future development.If successful, the project could pave the way for design of a pilot unit, taking a major step toward commercial implementation.