KNCC is a joint venture between Knutsen Group and NYK Group. They transport liquid CO2 (LCO2) to CO2 storage facilities using decades of experience, purpose-built barges, and their proprietary LCO2-EP technology.
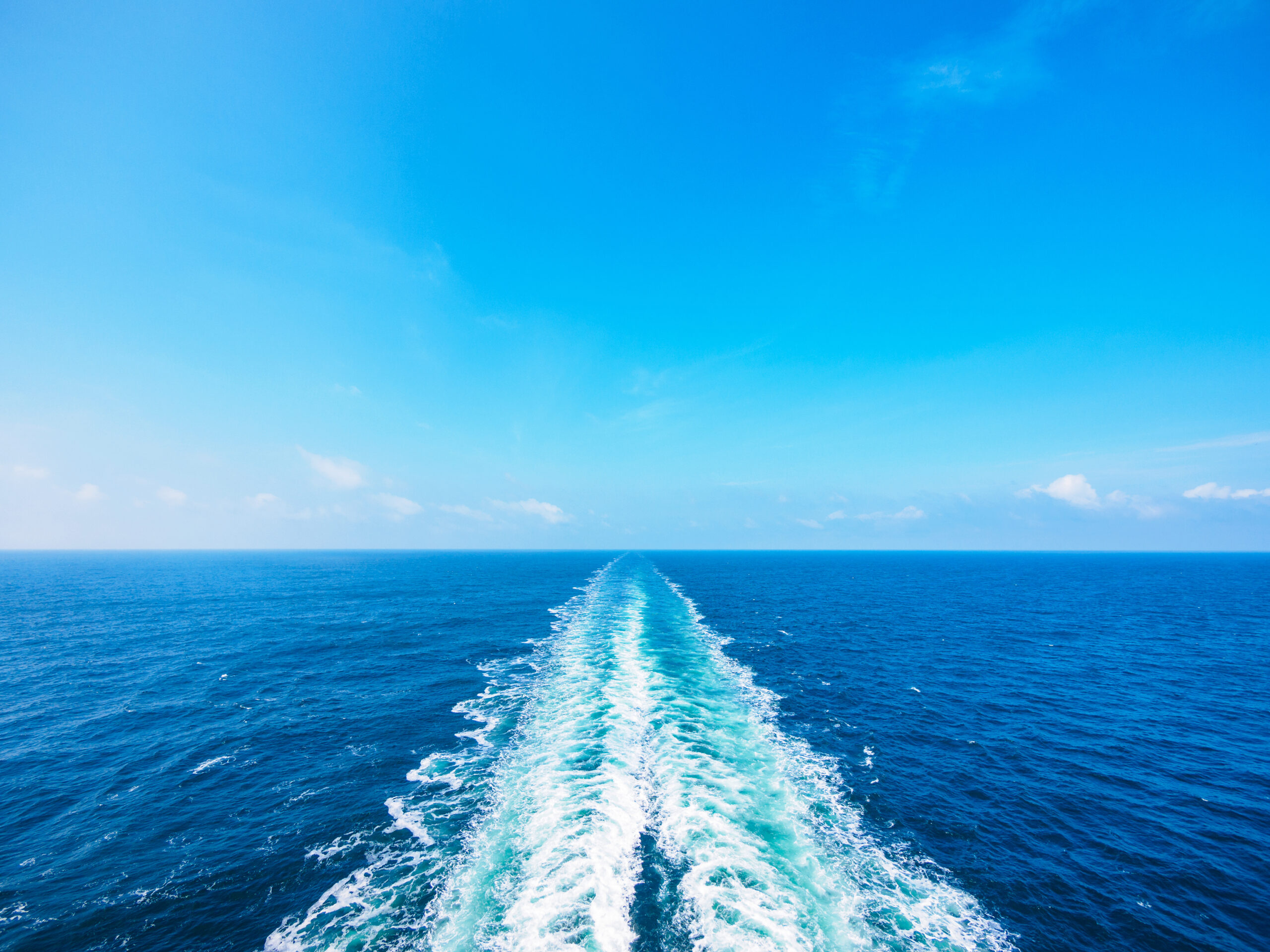
15.11.2023
KNCC: New CO₂ transport technology
The aim of the LCO2-EP project was to qualify the technology for future CO2 transport. KNCC has examined its technology in connection with both conversions and new constructions.
The project is supported by NOK 4.69 million from CLIMIT.
What has been tested?
The project has tested the tank design for Knutsen NYK Carbon Carrier’s (KNCC) LCO2-EP technology on an experimental scale at ResQ’s Safety and Emergency Response Centre close to the city of Haugesund. The LCO2-EP containment system is not a new technology but is based on the already well-documented development of pressurised natural gas (PNG) technology and gas pipeline design.
“Our test rig confirms that CO2 transport at elevated pressure (34 to 45 bar) is ready for deployment,” says Per Lothe, Special Technical Advisor Technology at Knutsen NYK Carbon Carrier. The test rig has also become a unique tool to increase the knowledge of how CO2 behaves at different pressures. The next phase of the project will be to test new CO2 equipment, in our case corrosion monitoring technology, and to investigate how impurities in the CO2 can affect KNCC’s technology.
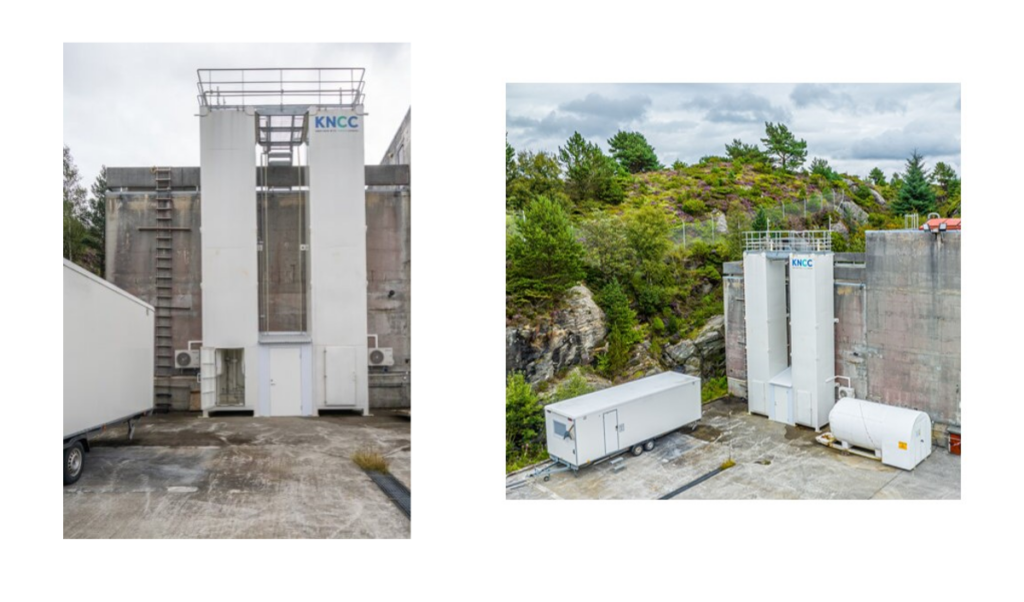
KNCC’s test rig
The test rig consists of two containers representing two independent CO2 tanks, each containing four pipe sections. The containers replicate a ship installation in scale design. The test program and procedures were developed with the operational needs of a CO2 cargo ship in mind. The test program followed the usual process of preparing a ship’s cargo system for receiving, loading, unloading CO2 and finally preparing for scheduled maintenance.
Solid results in collaboration with qualified partners
In this project, KNCC has collaborated with Equinor, DNV, Horizon Energy and CapeOmega. DNV and CapeOmega, together with the CLIMIT programme, contributed financially.
New ways of organising and implementing CO2 transport are possible and this project has shown that:
- The start-up, gassing and pressurisation of the CO2 was successfully carried out according to the procedures.
- New knowledge about heat transfer between CO2 phases and contact with steel provided important insights for further design and operation, including leak management.
- Minor leaks are easily detected and can be dealt with. Minimal cooling was observed during LCO2 recovery when tank pressure was maintained.
“Having access to a rig with CO2, where we can test equipment and observe adverse events, gives us confidence that the final transport of CO2 is safe,” concludes Per Lothe. The company has ambitions to become a major CO2 transporter in the future. Having a test rig for verification and crew training is important in this context.
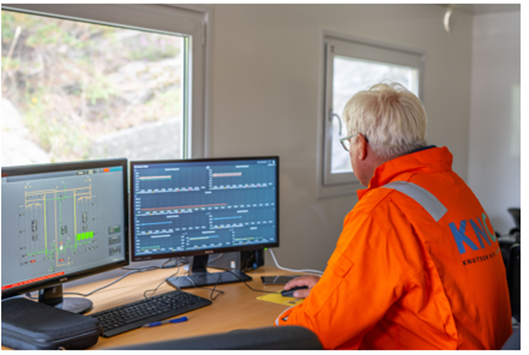