BIGH2/Fase III – “Enabling safe, clean and efficient utilization of hydrogen and ammonia as the carbon-free fuels of the future”
Budget
36 MNOKCLIMIT Financing
50%Project number
617137Project partners
- • SINTEF Energi AS
- • NTNU
- • Siemens Industrial Turbomachinery AB
- • Equinor
Project leader
SINTEF EnergiProject period
12/2017-12/2021Granted
08/06/2017Introduction
Industrial gas turbines are used for power generation and for mechanical drive of other machines. Today’s industrial gas turbines use natural gas or fuel oil as fuels. CO2 emissions from industrial gas turbines can be captured in post-combustion captured plants. Alternatively, the same emissions could be reduced by using low-carbon fuels that can be produced from fossil fuels in a central location with a carbon capture plant and terminal for CO2 transport to storage.
Hydrogen-rich fuels are the most relevant group of low-carbon fuels for gas turbines. However, the use of hydrogen-rich fuels in today’s state-of-the-art industrial gas turbines results in high NOx emissions. Therefore, conventional use of hydrogen-rich fuel requires fuel blending with nitrogen or steamwater vapor injection to reach acceptable emissions of NOx is conventionally used to be able to use hydrogen-rich fuel with acceptable emissions of NOx. The disadvantage of this conventional approach is that the thermal efficiency of the gas turbine is reduced, thus increasing the operating costs. The aim of this project is to develop knowledge and technology that enable gas turbines to burn hydrogen-rich fuels with acceptable emissions of NOx without a corresponding reduction in the thermal efficiency of the turbine. The project will thus enable a new type of CCS value chain in which CO2 is captured at the plant for production of hydrogen-rich fuels, with potentially lower capture costs and increased operational flexibility of the power plant compared to post-combustion capture.
Background and project purpose?
Advanced (state-of-the-art) low-NOx gas burners for power generation are based on the mixing of fuel and oxidant (in whole or in part) prior to combustion. With today’s knowledge, this means that it is not possible to combine low NOx emissions with efficient combustion of hydrogen. The present project seeks to bridge this knowledge gap and enable scenarios for industrial use of gas turbines with zero CO2 emissions. The challenge lies mainly in issues associated with flame stability and NOx emissions when using highly reactive fuels (as hydrogen). A standard solution for limiting the reactivity of the flame and thus its instability and NOx emissions is to dilute the hydrogen supply with steam or nitrogen. However, this has a significant cost due to lost thermal efficiency (separation / compression of nitrogen constitutes about 5 percentage points lower efficiency) and reduced margin (OPEX / CAPEX) due to equipment and processes necessary for steam / nitrogen hydrogen dilution. For industrial applications, the solution outlined above will have disadvantages, among them the need for large amounts of nitrogen to dilute the gas turbine fuelbe of little use, especially in offshore installations where weight and space requirements are limited and retrofitting is often impossible. The need for large amounts of nitrogen to dilute the gas turbine fuel will also be a disadvantage.
The project therefore emphasizes the development and testing of burners for gas turbines fired with ammonia as primary fuel, partially or completely split into hydrogen or nitrogen by the waste heat from the gas turbine. Ammonia is considerably easier to transport and store than hydrogen. If the project can confirm low safe and risk-free use of ammonia as the main source of a new gas turbine fuel, and this will satisfy the requirements for industrial use, use of ammonia can will be an important contributeion to reducing the CO2 intensity in the Norwegian oil and gas industry. At the same time, the project will lay the foundation for similar projects in other sectors of industry and transport, both nationally and internationally. The project is also based on two previous phases of BIGH2 (Phase I, 2008-2011; and Phase II, 2012-2015), and uses dedicated methodology for the continuation of already achieved results related to combustion technology.
What is the project objective?
The aim of the project is to enable use of carbon-free fuels in modern gas turbines. Thus, the need for CO2 handling is shifted from the site where the fuel is burned (distributed) to the place where the fuel is produced / processed (centrally). The proposed project is aimed at Siemens SGT750 gas turbine and the use of carbon-free fuels in industrial applications in the power range ~40MWe (especially relevant in offshore applications). The project will develop, test and demonstrate safe, efficient and clean combustion (low NOx) of selected carbon-free fuels based on mixtures of hydrogen, nitrogen and ammonia. The project will increase technological maturity for burners tested and verified at laboratory scale (TRL4) and include a full-scale demonstration of a single Siemens DLE burner at relevant conditions, aimed at industrial use offshore and onshore (TRL6). In addition, the project will aim to ensure stable operation of the whole gas turbines. The combustion chambers shall be protected against thermo-acoustic instability by mapping combustion dynamics (interaction between flame heat emission and acoustics in an annular combustion chamber) related to new and untested carbon-free fuel combinations (mixing ratios). The project will also clarify HSE aspects related to the introduction of ammonia as fuel in gas turbines in offshore and onshore industrial plants.
What has the project done in terms of activities?
The project has conducted the following research activities: 1) studied in detail the fundamental combustion properties of hydrogen/ammonia mixtures as gas turbine fuels, through extensive use of chemical kinetics (in collaboration with UCSD) and Direct Numerical Simulation of relevant combustion configurations (in collaboration with Sandia NL); 2) investigated experimentally, on simplified burner configurations, the thermo-acoustic and blowout properties of hydrogen/ammonia flames; 3) investigated experimentally the flame stability and NOx emissions from a downscaled SGT750-burner (4th generation DLE burner) fired, at atmospheric and pressurized conditions, with different blends of ammonia, hydrogen and nitrogen, ranging from pure ammonia to fully-decomposed ammonia (75%-25% hydrogen/nitrogen fuel mixture); 4) investigated with advanced numerical modelling (Large Eddy Simulation/LES and Chemical Reactors Network/CRN) flame stability and NOx emissions from a similar downscaled SGT750/burner; 5) assessed the risk related to the deployment of ammonia as main energy carrier for power generation in off-shore applications; 6) investigated the flammability and detonation limits for hydrogen/ammonia-air mixtures; 7) demonstrated 100% hydrogen firing in a single Siemens SGT600-burner (3rd generation DLE burner) at full-size and full-load conditions and demonstrated 60% (by volume) hydrogen firing of the whole SGT600 gas turbine (engine testing) up to full-load conditions.
What has the project achieved? Did the project achieve its objective?
The project has achieved the following results:
1) The first “short” chemical kinetics scheme for numerical modelling of hydrogen/ammonia flames is developed in collaboration with UCSD and has become a recognized “standard” tool for large-scale numerical simulations (DNS/LES) of combustion at conditions relevant to gas turbines and internal combustion engines.
2) The first detailed characterization of blow-out in laminar and turbulent premixed hydrogen/ammonia flame is obtained conducting a comparison between these and more conventional methane-air flames with (nominally) similar combustion properties. This result has important implications for the correct derivation of empirical correlations used to estimate the turbulent burning rate.
3) The first detailed characterization of thermo-acoustic instabilities that arise in single-flame and multi-flame (annular) combustion chambers is conducted by comparing the thermo-acoustic response of hydrogen/ammonia-air flames with conventional methane-air flames. These findings have important implications for an accurate assessment of the transferability of results obtained in downscaled lab-experiments, numerical simulations and full-size, single-burner testing to annular or hybrid (i.e. can-annular) combustion system layouts, found on the SGT600 and SGT750 gas turbine respectively.
4) The combined effect of pressure and of the fast molecular diffusion of the hydrogen molecule, resulting in a significant acceleration of the turbulent flame front for hydrogen-enriched flames at fuel-lean conditions, is revealed for the first time and discussed in detail based on results from highly accurate, large-scale numerical simulations (DNS).
5) The positive effect on NOx and N2O emissions from a Siemens 4th generation DLE burner design (from the SGT750 gas turbine), based on a rich-lean combustion staging approach, is demonstrated for hydrogen/ammonia-air flames, between atmospheric pressure and 10 bar, in SINTEF high pressure combustion rig (“HIPROX”).
6) Low-NOx 100% hydrogen firing of a single Siemens 3rd generation DLE burner (from the SGT600 gas turbine) at full-size and full-load conditions is demonstrated. Low-NOx operation of the whole SGT600 gas turbine (engine testing) is also demonstrated for 60% hydrogen firing up to full-load.
7) The risk connected to the deployment of ammonia as energy carrier and the consequences of an eventual large-scale ammonia leakage on a FPSO-vessel is assessed.
Future plans?
Results from BIGH2/Phase III haves shown that, implementing a rich-lean combustion staging approach in an existing DLE burner design, it is possible to achieve a stable flame and relatively low NOx/N2O emissions from combustion of an ammonia-derived fuel mixture (NH3/H2/N2 blend). However, because only marginal modifications of an existing burner/combustion chamber design were attempted, there still is a significant uncertainty about the best approach to rich-lean combustion staging. In order to proceed beyond the results achieved in BIGH2/Phase III, an optimization of the burner and of the combustion chamber is required to ensure that, on one side, in the fuel-rich (and very hot) primary combustion zone, heat load from the flame to the most exposed metal parts does not exceed the material properties’ limitations and, on the other side, the injection of secondary air achieves optimal mixing with and combustion of the leftover fuel (hydrogen) from the primary combustion zone. Therefore, future plans include research, development and demonstration of an opportunely modified DLE burner and combustion chamber that ensure fuel flexibility, i.e. seamless transition between natura gas and ammonia-based firing of the engine, in a realistic gas turbine burner design. In this context it is important with continued focus on the Siemens 4th generation DLE burner and the SGT750 gas turbine because: 1) The SGT750 is the newest and most modern gas turbine in Siemens’ portfolio for the 30-50 MWe class; 2) This gas turbine class is the most relevant in the Norwegian context, and for the transition to a low-carbon oil and gas industry in particular; 3) The SGT750 is characterized by a so-called “can-annular” layout of the combustion system that ensures optimal and seamless transferability between research, development and demonstration conducted on a downscaled or full-size single burner/combustion chamber assembly and later pilot testing of the whole gas turbine (engine testing).
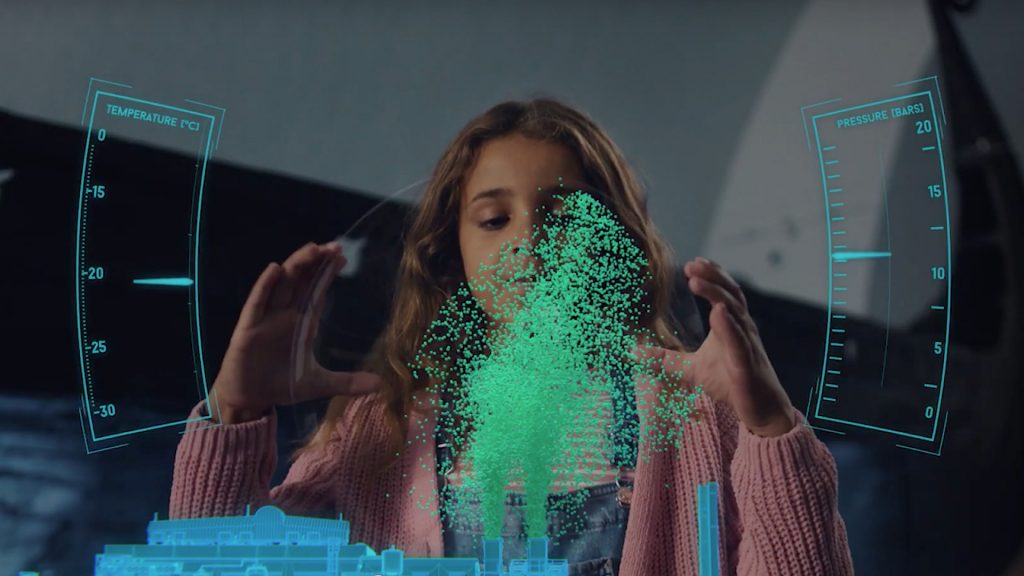