FSC-PVAm Membrane for CO2 Capture (Phase 2)
Budget
14 MNOKCLIMIT Financing
46.4%Project number
229949Project partners
- • NTNU
- • Air Products & Chemicals Inc. (US)
- • Equinor, Alberta Innovates – Energy and Environment Solutions (Canada)
- • SINTEF
- • DNV (Arnhem,The Netherlands)
Project leader
NTNUProject period
2013 - 2016Granted
10/06/2013The project FSC2– Fixed-Site-Carrier Membrane (FSCM) Phase 2, has been a continuation of the CLIMIT-project 1933891, and has had the following goals:
1. Upscaling and verification of the good results which were documented in Phase 1 of the project
2. Develop the coating procedures from flat sheets to commercial hollow fiber membranes on a scale up to 10 m2
The FSC2 project started in June 2013 and terminated December 2016. The work in the project has been divided into the following four activities:
1. Development, coating and characterization of hollow fiber membrane modules
2. Construction and commissioning of the test rig
3. Testing the membrane separation with relevant gas streams, and at relevant conditions
4. Further development of the membrane simulation code for including facilitated transport. Simulations of relevant processes for energy calculations, membrane area demand and cost evaluations with comparison to chosen base case
The membranes have been tested both in lab and under various process conditions in a special designed and constructed membrane pilot rig at Tiller, Trondheim. The facilitated transport mechanism for CO2-tranport through the membrane has been studied in depth in order to further develop the simulation model which is used for the membrane process. Large scale membrane processes have been simulated and cost estimated for flue gas contained different concentrations of CO2.
The development of the hollow fiber membranes has been done in collaboration with Air Products (USA), while the membrane technology is patented by NTNU. Other project partners have been Statoil and oil companies in Canada through Alberta Innovates. DNV GL and Sintef MC have contributed together with NTNU.
The FSC-membrane is a composite membrane where the membrane is a very thin layer of polyvinylamine (PVAm) where the amine group on the polymer backbone chain is a “carrier” contributing to the quick transport of CO2 through the membrane when this is humidified. This gives the membrane the superior separation properties compared to a standard polymeric membrane. The hollow fibers are made of polysulfone (PSf) which forms the support structure for the thin membrane layer. In-situ coating of the fibers with PVAm was done; this means that Air Products delivered the commercial modules containing the PSf fibers, and the coating was done at NTNU according to their developed method.
In Activity 1 the fibers were firstly spun at NTNU, then coated with PVAm in lab and mounted in small modules (724 cm2). Then the next step was using the commercial small AP modules (0.83m2), and starting to develop the method for in-situ coating. The importance of parameters like gas feed flow, sweep gas and pressure were investigated with respect to their influence on the separation of CO2. The modules were scaled up step-by-step, and the coating method adjusted – a suitable module size was chosen to be 4.2 m2. 10 m2 modules were also coated with the PVAm membrane, but the 4.2 m2 modules turned out to be more flexible for the testing and several modules could be run at the same time.
Activity 2 consisted mainly of designing and building the test rig – this was done in the workshop at NTNU with the assistance of highly qualified mechanics. The rig was then transported in two large sections to Sintef’s test facilities at Tiller. The dimensions of piping and equipment were based on data obtained in tests with the small hollow fiber membrane modules. The gas flow to the pilot was a side-stream of the flue gas from the propane burner, and could be adjusted up to 50 Nm3/h. Thorough hazop analysis were conducted before and after the building of the pilot rig.
In Activity 3 which lasted for about 6 months, several test regimes were conducted, and the following parameters were varied: Feed flow, pressure ratio of feed-permeate side, temperature, composition of the gas (CO2 volumes in the range from 8vol% to 12.4 vol%). It was a bit difficult to conclude on which conditions gave optimum separation. It was, however, very well documented that a purity of CO2 well above 60% could be achieved for a one stage process for the high concentrations of CO2 in the flue gas at Tiller, and the measured flux would give an acceptable membrane area if two stages were to be used. The optimum material properties were difficult to measure due to restrictions in the gas flow and too high stage cut. (These values are more easily measured in lab on a small scale system.)
Durability tests were not performed in this project, as there in parallel were running tests at the cement plant at Norcem in Brevik, under much more aggressive conditions. From tests run over about 8 months, the indications are that the FSC-membrane can tolerate SOx and NOx very well.
In Activity 4 the facilitated transport of CO2 through the membrane was studied in depth; likewise the importance of water (humidity) for the reaction with CO2 when separating this component from the flue gas. A facilitation factor for the transport could be calculated, and thus contributed to estimate the best operational process conditions.
In order to achieve a purity for CO2 of 95% and capture >80% CO2, a two-stage process must be used – this was documented by simulations. The measured permeances from Activity 3 were used in Activity 4 to simulate several alternative processes, and results compared to a chosen base case in a published article2. Permeance and selectivity are input to the simulation program (Chembrain – proprietary) and will have a large influence on how easily the set goals can be achieved (purity of 95% CO2 and >80% CO2 capture) with an acceptable membrane area. Likewise, the CO2 content in the flue gas will be of major importance: Low CO2-content (in this project 8-9.6%) can be purified to 95%, but the capture rate will in general be lower than 80% for an economical process – in the current project the simulations demonstrated an economical capture rate up to 70% for the low CO2 content. High CO2 content (in the project the flue gas contained up to 12.4%) can easily capture >80%.
The calculated capture and cost data for the processes in the project which were based on measured data for the membrane pilot at Tiller, were lying a bit higher than the published “base case”2. It was however clearly documented that the FSC-membrane has a nice potential for optimization and commercialization through i) improved and professional coating method, ii) re-design of the module with respect to packing density and fiber aspect ratio, iii) optimized process design with respect to temperature (60°C), pressure ratio and feed flow.
The FSC membrane development, process design included, were evaluated to be on TRL 5-6 at the end of the project. The membrane is judged to have a nice potential for scaling up to the next level towards commercialization. In conclusion; the goals of the project were reached with the exception of not being able to fully complete the incorporation of the facilitated transport mechanism in the simulation model.
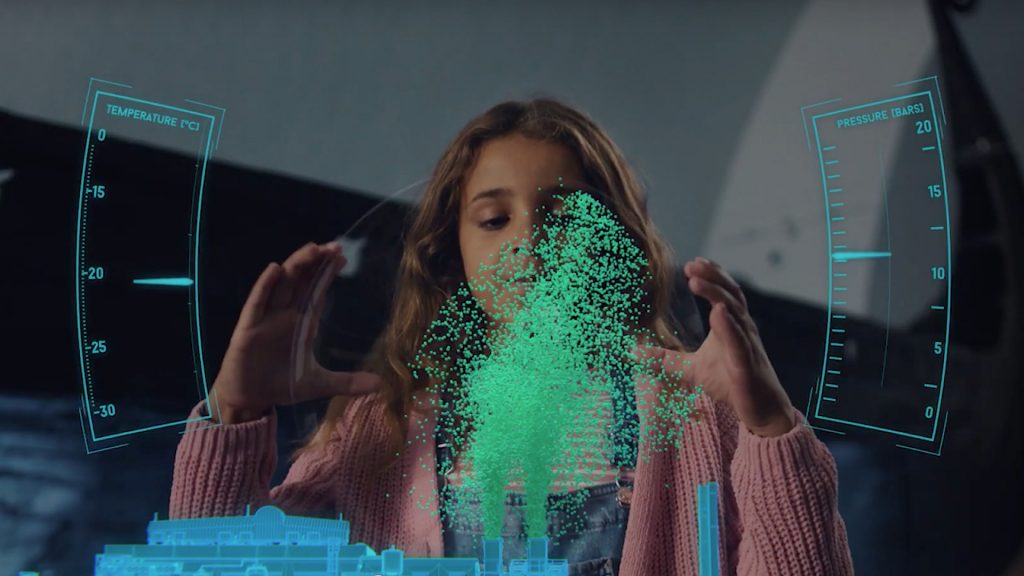