CO2 Capture Test Facility at Norcem Brevik, Project Phase II, Test Step 1
Budget
93.253 MNOKCLIMIT Financing
75%Project number
221323Project partners
- • Norcem
- • HeidelbergCement
- • European Cement Research Academy
- • Aker Carbon Capture, Research Triangle Institute (RTI)
- • Kema Nederland BV (DNV KEMA)
- • NTNU
- • Alstom Norway AS
Project leader
NorcemProject period
2013-2017Granted
11/06/2012In May 2013 Norcem and its partners; HeidelbergCement and ECRA (European Cement Research Academy) were granted funding by Gassnova, for establishing of a small scale test center for testing of various post-combustion carbon capture technologies on real cement process conditions.
The project was launched in May 2013 and concluded by July 2017.
Four various post-combustion technologies were selected for test Phase I (2014):
Aker Solutions (AKSO) – Amine Technology (1. Generation)
RTI – Solid Sorbent Technology (3. Generation)
KEMA GL/ NTNU & Yodfat Engineers – Membrane Technology (MC) (3. Generation)
Alstom Power – Regenerative Calcium Cycle (2. Generation)*
*Alstom Power (now General Electric) was not in the position to develop and bring a test pilot to Brevik, so therefore Alstom conducted a de-risking study and used a test facility at the University of Stuttgart for their performance testing.
Two technologies were further studied in Phase II (2016):
RTI – Solid Sorbent Technology (3. Generation)
NTNU & Air Products – Membrane Technology (MemCCC) (3. Generation)
The project objectives have been as follows:
a. Establish a small scale test centre with all utility requirements set by the technology providers
b. Testing and studying four various post-combustion carbon capture technologies on real process conditions
c. Compare the technologies in a full scale perspective and determine how suitable these are for implementation at modern cement kilns (based on the benchmark analysis)
Aker Solutions defined a six months test program and upfront the test campaigns, the green solvent; S26 was developed and tested at the Tiller rig in Trondheim. In Brevik Aker tested with their mobile test unit (MTU) and managed close to 3000 testing hours on real conditions. The test program was a success and no solvent degradation due to contamination from the flue gas was observed. During the testing, Aker managed to reduce the specific regenerator duty to 2.7 – 2.8 MJ/kg CO2. Waste heat from the cement process can be used for regeneration of the solvent in the stripper.
RTI tested their solid sorbent technology in two phases. In Phase I RTI constructed a small bench scale rig for sorbent exposure testing. A three month program was conducted with the sorbent poly-ethylene-imine (PEI). The sorbent working capacity was demonstrated to be in the range of 5-7 wt%. Due to the promising results, the project was continued into Phase II. RTI constructed a three-floor pilot and produced an optimized sorbent, expected to have a working capacity in the range of 9-11 wt%. RTI conducted a 6 months test program. The pilot was unstable most of the trial and a lot of time was used for troubleshooting and optimization of the pilot. Only in smaller time periods it was possible to collect trustworthy data which were used for the economic calculations. The technology readiness level (TRL 5 after Phase I) was not matured during the Phase II testing. RTI need to further develop the technology design and conduct new trials, in order to obtain stable operation, necessary for developing the technology further.
The fixed-site-carrier membrane technology has been tested in two phases. In Phase I; NTNU, DNV KEMA and Yodfat Engineers conducted a 6 months test program (with membranes configuration as flat-sheet membranes) where the main goal was to expose the membrane for the cement process environment. Unfortunately the test pilot was of low quality and the consortium faced serious problems with the pilot operation. Nevertheless 6-7 short term pilot campaigns were managed and a permeate purity of 72 % CO2 was achieved. The project was terminated after Phase I but a new membrane project; MemCCC with the partners NTNU and Air Products was launched in 2015. The project itself has not been part of this particular project, but the results from the trial have been used for updating the benchmark analysis. The Phase II testing was used with the same fixed-site-carrier membrane (poly-sulfone membrane with a top layer of polyvinylamine, PVAm) but now processed as hollow fibers. Air products provided a high quality test pilot and six months, successfully test program was conducted. The main focus of MemCCC was durability testing and predicting of the membrane life time, which was estimated to 5 years. Conclusion is that further optimization of the design is necessary. Air Products has signed an exclusive license for further development of the technology and as a commercial partner, Air Products need to conduct own pilot testing for maturing the technology and to move it forward from the current TRL level of 5.
A de-risking study was conducted by Alstom in order to develop their regenerative calcium cycle (RCC) technology. The RCC test facility at IFK at the University of Stuttgart was used for the trials. The de-risking study was divided into two parts; 1) limestone deactivation characterization (TGA-testing) and 2) confirmation of the sorbent performance through pilot testing. The deactivation study showed that the limestones deactivated faster than anticipated. Two test campaigns were carried out and one of the limestone used, was the Verdal limestone from Brevik. Stable operation was achieved and data were collected for full-scale simulations. Further development of the technology will required a test pilot and trials on real conditions must be performed. Norcem evaluate the RCC technology to be more suited for greenfield cement plant and a TRL of 3 seems to describe the present state of the technology applied to a cement plant.
Based on the results from the field testing in Phase I, a benchmark study was conducted. The aim of the analysis was to study and compare the four selected post-combustion technologies and investigate how suitable these technologies are for full scale installation at modern cement kiln systems. Technical, environmental and economic aspects of a commercial scale installation have been investigated.
The benchmark analysis in Phase I concluded that Aker Solutions amine technology is by far the more developed technology. Aker has developed a solvent mixture (S26) and a solvent regeneration concept well suited for CO2 capture in the cement kiln flue gas, with a low reclaimer waste generation rate. Successful pilot-scale testing of the technology has been performed with Aker’s mobile test unit (MTU) in Brevik. With a technology readiness level (TRL) of 8, the technology is more or less ready for full-scale implementation in a cement plant. An innovative combination of waste heat utilization and internal process integration is used to eliminate the need for an external steam generation plant. Partial CO2 capture, with a capture rate as high as 48% is likely possible with this system.
Based on the updated benchmark analysis in Phase II with updated data from RTI and MemCCC, Aker’s case has strengthened its position in comparison with the three other technologies when it comes to costs. The Aker technology is definitely also more mature than the three other technologies. Updating the benchmark analysis with values from Phase II was very useful as some of the key uncertainties regarding the RTI and MemCCC technologies could be further investigated and used as a basis for an improved overall analysis.
Even if the amine technology is today (2017) more mature and basically ready for implementation in the cement industry, it is likely that a palette of technologies will be available and suitable in the future. Local conditions may be decisive when determining which technology should be applied at a given plant.
The Brevik project has shown that development of capture technologies are demanding, time consuming and requires considerably resources. Norcem has experienced the importance of setting clear targets but at the same time take small steps towards the goals. The support from Gassnova has been vital for the project and the technology development.
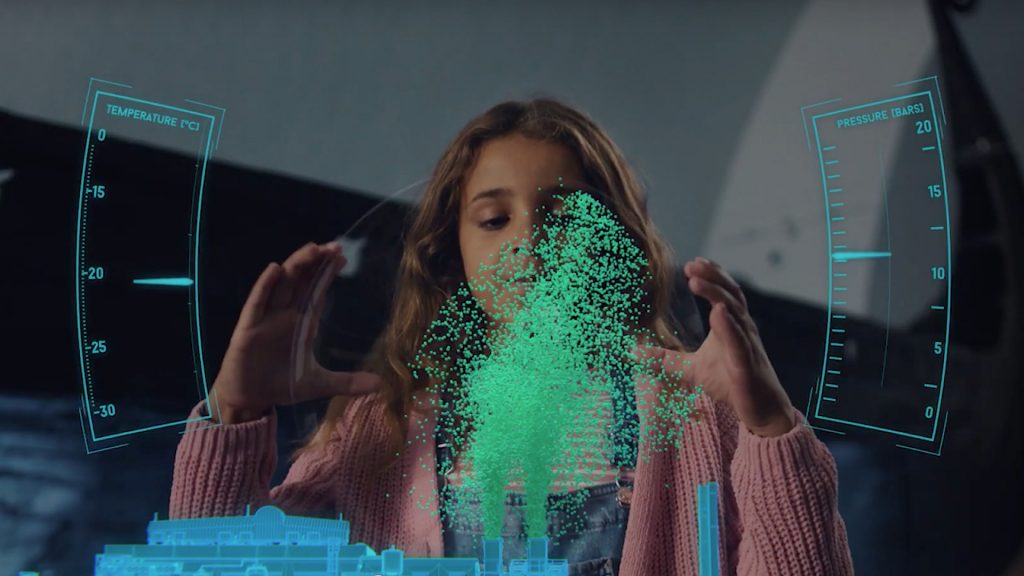